Phosphorus and nitrogen containing flame-retardant finishing agent and flame-retardant cellulose fiber fabric preparation method
A technology of flame retardant finishing agent and cellulose fiber, which is applied in the direction of flame retardant fiber, fiber treatment, plant fiber, etc. It can solve the problems of low solubility and unfavorable flame retardant application of natural cellulose and regenerated cellulose, and achieve durability Effect
- Summary
- Abstract
- Description
- Claims
- Application Information
AI Technical Summary
Problems solved by technology
Method used
Examples
Embodiment 1
[0019] In this example, the preparation of the flame retardant finishing agent and the specific steps of the flame retardant finishing of the cellulose fiber fabric are as follows:
[0020] 1. Weigh 400 grams of phytic acid solution with a mass fraction of 70%, and pour it into a 2-liter reactor equipped with a mechanical stirrer and a thermometer; weigh 151 grams of urea and slowly pour it into the reactor; start the agitator, Electronically controlled heating, when the temperature rises to 90°C, the reaction lasts for 5 hours to obtain the flame retardant ammonium phytate;
[0021] 2. Weigh 150 grams of ammonium phytate obtained in step 1, and 50 grams of urea and 50 grams of dicyandiamide are dissolved in 0.75 liters of water, and fully stirred to obtain a flame retardant finishing agent;
[0022] 3. Immerse 1 kg of Lyocell fiber fabric in the flame-retardant finishing solution described in step 2, and immerse it for 90 minutes at 50°C, then press the Lyocell fiber fabric w...
Embodiment 2
[0024] In this example, the preparation of flame retardant finishing agent and the specific steps of flame retardant finishing of cellulose fiber / fabric are:
[0025] 1. Weigh 400 grams of phytic acid solution with a mass fraction of 70%, and pour it into a 2-liter reactor equipped with a mechanical stirrer and a thermometer; weigh 154 grams of hydrazine hydrate with a mass fraction of 80% and slowly pour it into the reaction In the kettle; start the agitator, electric control heating, when the temperature rises to 50 ℃, continue to react for 5 hours, that is, the flame retardant ammonium phytate;
[0026] 2. Weigh 140 grams of ammonium phytate obtained in step 1, and 60 grams of urea, and 50 grams of dicyandiamide are dissolved in 0.75 liters of water, and fully stirred to obtain a flame retardant finishing agent;
[0027] 3. Immerse 1 kg of cotton fiber fabric in the flame-retardant finishing solution described in step 2, soak it for 60 minutes at 70°C, and then press the co...
Embodiment 3
[0029] In this example, the preparation of flame retardant finishing agent and the specific steps of flame retardant finishing of cellulose fiber / fabric are:
[0030] 1. Weigh 400 grams of phytic acid solution with a mass fraction of 70%, and pour it into a 2-liter reactor equipped with a mechanical stirrer and a thermometer; weigh 352 grams of ammonia water with a mass fraction of 25%, and slowly pour it into the reactor In the middle; start the stirrer, electric control heating, when the temperature rises to 40 ℃, continue to react for 2 hours, that is, the flame retardant ammonium phytate;
[0031] 2. Weigh 160 grams of ammonium phytate obtained in step 1, and dissolve 40 grams of urea and 50 grams of dicyandiamide in 0.75 liters of water, and stir fully to obtain a flame retardant finishing agent;
[0032] 3. Immerse 1 kg of viscose fiber fabric in the flame-retardant finishing solution described in step 2, dip for 120 minutes at 60°C, and then press the viscose fiber fabr...
PUM
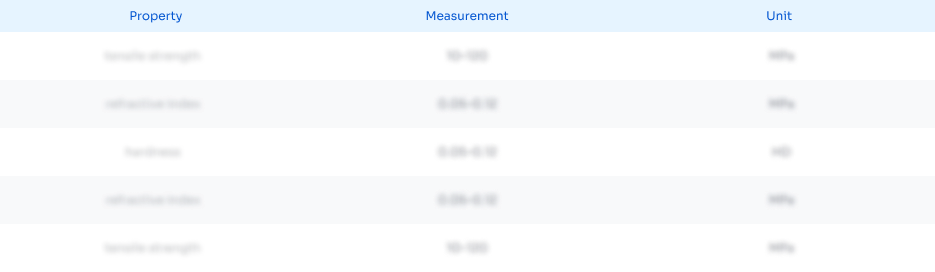
Abstract
Description
Claims
Application Information

- R&D Engineer
- R&D Manager
- IP Professional
- Industry Leading Data Capabilities
- Powerful AI technology
- Patent DNA Extraction
Browse by: Latest US Patents, China's latest patents, Technical Efficacy Thesaurus, Application Domain, Technology Topic, Popular Technical Reports.
© 2024 PatSnap. All rights reserved.Legal|Privacy policy|Modern Slavery Act Transparency Statement|Sitemap|About US| Contact US: help@patsnap.com