Pre-tensioning method prestressed concrete track board production line pouring vibrating system and application thereof
A technology of pouring and vibrating and track slabs, which is applied to auxiliary molding equipment, supply devices, ceramic molding machines, etc., can solve problems such as human interference, difficult placement, noise pollution, etc., to ensure stable and synchronous lifting, facilitate independent control, Stable and reliable structure
- Summary
- Abstract
- Description
- Claims
- Application Information
AI Technical Summary
Problems solved by technology
Method used
Image
Examples
Embodiment Construction
[0065] The present invention will be further described below in conjunction with the examples, but it should not be interpreted as a limitation of the present invention. The protection scope of the present invention is based on the content recorded in the claims, and any equivalent technical means made according to the specification is replaced without departing protection scope of the present invention.
[0066] The overall concept of the pouring and vibrating system in this embodiment is as shown in the figure, including a distribution mechanism arranged above the track slab mold 21 traveling along the travel track 29, a jacking mechanism arranged below the track slab mold 21 and adapted to it, and The vibrating mechanism, the distributing mechanism, the jacking mechanism and the vibrating mechanism are respectively connected with the control mechanism, wherein:
[0067] A. The material distribution mechanism includes a walking truss 1 fixed above the track plate mold 21 and...
PUM
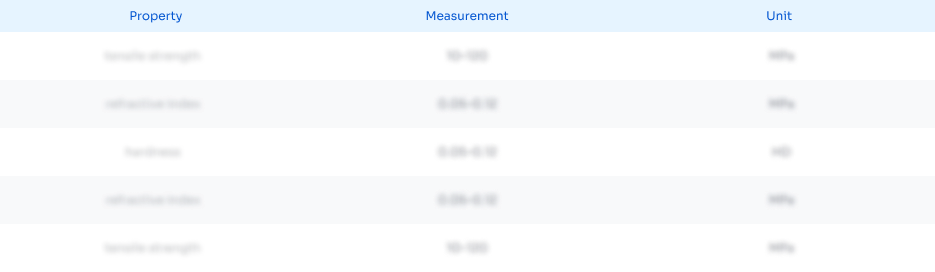
Abstract
Description
Claims
Application Information

- R&D
- Intellectual Property
- Life Sciences
- Materials
- Tech Scout
- Unparalleled Data Quality
- Higher Quality Content
- 60% Fewer Hallucinations
Browse by: Latest US Patents, China's latest patents, Technical Efficacy Thesaurus, Application Domain, Technology Topic, Popular Technical Reports.
© 2025 PatSnap. All rights reserved.Legal|Privacy policy|Modern Slavery Act Transparency Statement|Sitemap|About US| Contact US: help@patsnap.com