Method for comprehensively recovering useful metals from APT tungsten smelting slag
A kind of smelting slag, a useful technology, applied to the improvement of process efficiency, solid separation, etc., can solve the problems of large environmental impact, low recovery rate, high cost, etc., and achieve the effect of low investment cost, wide application range, and easy industrial application
- Summary
- Abstract
- Description
- Claims
- Application Information
AI Technical Summary
Problems solved by technology
Method used
Image
Examples
Embodiment 1
[0025] Useful metals are recovered from the tungsten smelting slag sample whose element content is shown in Table 1:
[0026] Table 1: Sample chemical multi-element analysis / %
[0027]
[0028] 1. Sieve and mix samples according to step (1). The mass concentration of the pulp is 15%, the stirring time is 30 minutes, the dosage of dispersant is 300g / t, and the stirring speed is 1800r / min. The sieve hole is 0.074mm) for classification, the product on the sieve is returned to the mixing drum, and the product under the sieve is subjected to the process of step (2).
[0029] 2. The under-screen material obtained in step (1) is sent into a high gradient magnetic separator to reclaim magnetic iron minerals with a mass concentration of 15% in the form of pulp. The magnetic field strength is 8000 Oersted. After two selection operations, the obtained iron The concentrate grade is 47.84%, and the recovery rate is 85.34%.
[0030] 3. Use the rotary vibrating disk concentrator to reco...
Embodiment 2
[0039] Useful metals are recovered from the tungsten smelting slag sample whose element content is shown in Table 2:
[0040] Table 2: Sample chemical multi-element analysis / %
[0041]
[0042] 1. Sieve and mix samples according to step (1). The mass concentration of the pulp is 10%, the stirring time is 60 minutes, the dosage of dispersant is 500g / t, and the stirring speed is 2000r / min. After stirring, it is sent into a high-frequency vibration fine screen ( The sieve hole is 0.074mm) for classification, the product on the sieve is returned to the mixing drum, and the product under the sieve is subjected to the process of step (2).
[0043] 2. The under-screen material obtained in step (1) is sent into a high gradient magnetic separator to reclaim magnetic iron minerals with a mass concentration of 15% in the form of pulp. The magnetic field strength is 8000 Oersted. After two selection operations, the obtained iron The concentrate grade is 43.25%, and the recovery rate i...
PUM
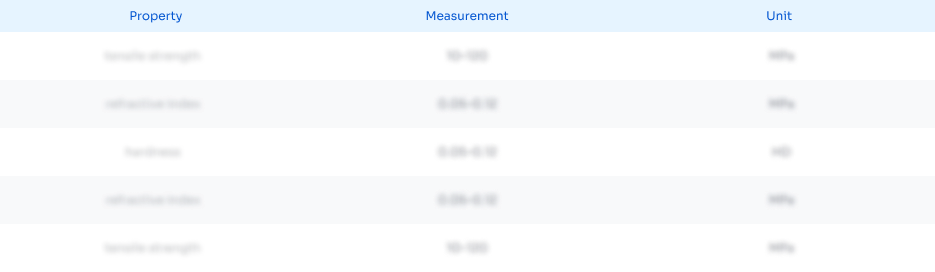
Abstract
Description
Claims
Application Information

- R&D
- Intellectual Property
- Life Sciences
- Materials
- Tech Scout
- Unparalleled Data Quality
- Higher Quality Content
- 60% Fewer Hallucinations
Browse by: Latest US Patents, China's latest patents, Technical Efficacy Thesaurus, Application Domain, Technology Topic, Popular Technical Reports.
© 2025 PatSnap. All rights reserved.Legal|Privacy policy|Modern Slavery Act Transparency Statement|Sitemap|About US| Contact US: help@patsnap.com