Machining method of narrow and small grinding undercuts of roller bearing
A technology of roller bearing and processing method, which is applied to bearing components, shafts and bearings, mechanical equipment, etc., can solve the problems of large dispersion of the size of the overtravel groove, excessive size of the overtravel groove, and low qualified rate of finished products, etc. Avoid the outflow of defective products, improve the anti-wear ability, and control the effect of heat treatment deformation
- Summary
- Abstract
- Description
- Claims
- Application Information
AI Technical Summary
Problems solved by technology
Method used
Image
Examples
specific Embodiment approach 1
[0039] Specific implementation mode one: combine Figure 1 to Figure 4 Describe this embodiment, a method for processing a narrow overrun groove of a roller bearing according to this embodiment, the method includes the following steps,
[0040] Step 1. Fine turning the first plane A, the second plane B and the outer diameter of the ferrule 1:
[0041] The first plane A, the second plane B of the roller bearing ring and the outer diameter 1 of the ring are finely machined by two knives in turn by using the method of split cutting;
[0042] Step 2. Inner diameter of thin turning ferrule 2:
[0043] Using the method of cutting with separate knives, the inner diameter 2 of the ferrule is finely machined with two knives;
[0044] Step 3, thin car rib 3 and raceway 4:
[0045] Carry out fine turning on the rib 3 and the raceway 4 of the roller bearing ring in turn;
[0046] Step 4, fine car overrun slot 5:
[0047] The overrun groove 5 of the roller bearing ring is finely machi...
specific Embodiment approach 2
[0058] Specific implementation mode two: combination figure 2 To illustrate this embodiment, the cutting parameters of the first plane A, the second plane B, and the outer diameter 1 of the ferrule in step 1 of the first fine turning are: the cutting allowance is 60%, and the feed rate is 0.2 mm / r, the cutting speed is 180m / min; the cutting parameters of the first plane A, the second plane B and the outer diameter of the ferrule 1 of the second fine turning are: the cutting allowance is 40%, and the feed rate is 0.22mm / r, the cutting speed is 200m / min. In such a setting, using the method of split cutting, a reasonable amount of back cutting is given in the process of the first plane A, the second plane B and the outer diameter of the ferrule to reduce the residual stress on the surface of the ferrule, so that Control the heat treatment deformation to ensure the size of the overrun groove of the final product. Other compositions and connections are the same as in the first ...
specific Embodiment approach 3
[0059] Specific implementation mode three: combination figure 2 To illustrate this embodiment, the cutting parameters of the inner diameter 2 of the first fine turning ring in step 2 of this embodiment are: the cutting allowance is 60%, the feed rate is 0.2mm / r, and the cutting speed is 160m / min; The cutting parameters of the inner diameter 2 of the second fine turning ring are: the cutting allowance is 40%, the feed rate is 0.22mm / r, and the cutting speed is 180m / min. In such a setting, using the method of split cutting, a reasonable amount of back cutting is given in the 2nd process of the inner diameter of the fine turning ferrule, so as to reduce the surface residual stress of the ferrule, thereby controlling the heat treatment deformation and ensuring the size of the overtravel groove of the final product . Other compositions and connections are the same as those in Embodiment 1 or Embodiment 2.
PUM
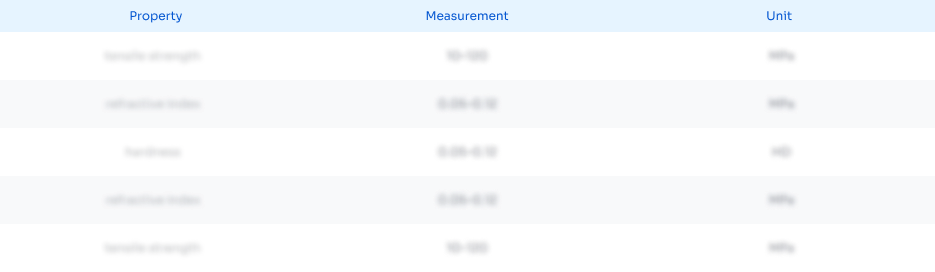
Abstract
Description
Claims
Application Information

- R&D
- Intellectual Property
- Life Sciences
- Materials
- Tech Scout
- Unparalleled Data Quality
- Higher Quality Content
- 60% Fewer Hallucinations
Browse by: Latest US Patents, China's latest patents, Technical Efficacy Thesaurus, Application Domain, Technology Topic, Popular Technical Reports.
© 2025 PatSnap. All rights reserved.Legal|Privacy policy|Modern Slavery Act Transparency Statement|Sitemap|About US| Contact US: help@patsnap.com