Catalyst for alcohol alcohol condensation reaction, preparation method and application thereof
A condensation reaction and catalyst technology, applied in the field of catalysts, can solve problems such as the mismatch of active centers on catalysts, and achieve the effects of extending the methanol industry chain, simple preparation methods, and simple process flow
- Summary
- Abstract
- Description
- Claims
- Application Information
AI Technical Summary
Problems solved by technology
Method used
Examples
Embodiment 1
[0033] 0.53g Cu(NO 3 ) 2.3H 2 O, 38.62g Mg(NO 3 ) 2 .6H 2 O, 16.96g Al(NO 3 ) 3 .9H 2 O and 0.87gCe(NO 3 ) 3 ·6H 2 O was dissolved in 400ml deionized water to obtain solution A with a total concentration of metal ions of 0.5mol / L. Combine 56.1gKOH and 69.1gK 2 CO 3 Dissolve in 1000ml deionized water to obtain OH- ion concentration of 1mol / L, CO 3 2- Solution B with a concentration of 0.5 mol / L. Under stirring conditions, at a temperature of 50° C. and a pH of 9.5, A and B co-precipitate to obtain slurry C. Slurry C was dynamically crystallized under hydrothermal conditions at 80° C. for 10 h to obtain slurry D. The slurry D was filtered, washed and dried at 120°C for 10 hours, and then calcined at 750°C for 4 hours to obtain the desired catalyst. The molar composition of the catalyst was: Cu:Mg:Al:Ce=1.1:75.3:22.6:1.
[0034] Above-mentioned catalyzer is applied to tubular fixed-bed reactor: before reaction, in containing 5v%H 2 Under a nitrogen atmosphere, t...
Embodiment 2
[0036] 3.92g Ni(NO 3 ) 2 .6H 2 O, 80.19g Mg(NO 3 ) 2 .6H 2 O, 39.16g Al(NO 3 ) 3 .9H 2 O and 8.31gZr(NO 3 ) 4 ·5H 2 O was dissolved in 300ml deionized water to obtain solution A with a total concentration of metal ions of 1.5mol / L. Combine 67.32gKOH and 82.92gK 2 CO 3 Dissolve in 800ml deionized water to obtain OH- ion concentration of 1.5mol / L, CO 3 2- Solution B with a concentration of 0.75 mol / L. Under stirring conditions, at a temperature of 60° C. and a pH of 10.0, A and B co-precipitate to obtain a slurry C. Slurry C was dynamically crystallized under hydrothermal conditions at 120° C. for 15 hours to obtain slurry D. The slurry D was filtered, washed and dried at 100°C for 20 hours, and then calcined at 450°C for 5 hours to obtain the desired catalyst. The molar composition of the catalyst was: Ni:Mg:Al:Zr=3:69.5:23.2:4.3.
[0037] Apply above-mentioned catalyzer to tubular fixed-bed reactor: before reaction, in containing 8v%H 2 Under the argon atmosp...
Embodiment 3
[0039] 1.49g Cu(NO 3 ) 2 .3H 2 O, 1.79g Co(NO 3 ) 2 .6H 2 Og, 46.24gMg (NO 3 ) 2 .6H 2 O, 15.41g Al(NO 3 ) 3 .9H 2 O and 5.33g La(NO 3 ) 3 ·6H 2 O was dissolved in 410ml of deionized water to obtain solution A with a total concentration of metal ions of 0.6mol / L. Combine 40.00gNaOH and 53.00gNa 2 CO 3 Dissolve in 500ml deionized water to obtain OH- ion concentration of 2mol / L, CO 3 2- Solution B with a concentration of 1 mol / L. Under stirring conditions, at a temperature of 65° C. and a pH of 10.2, A and B co-precipitate to obtain slurry C. Slurry C was dynamically crystallized under hydrothermal conditions at 100° C. for 12 hours to obtain slurry D. The slurry D was filtered, washed, dried at 110°C for 15 hours, and then calcined at 600°C for 5 hours to obtain the desired catalyst. The molar composition of the catalyst was: (Cu+Co):Mg:Al:Zr=5:73.3:16.7:5.
[0040] Apply above-mentioned catalyzer to tubular fixed-bed reactor: before reaction, in containing ...
PUM
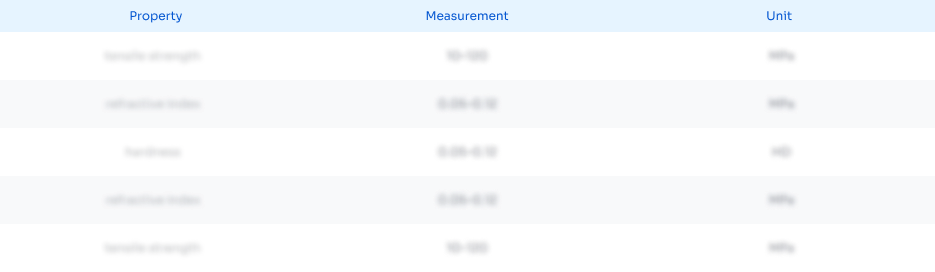
Abstract
Description
Claims
Application Information

- R&D Engineer
- R&D Manager
- IP Professional
- Industry Leading Data Capabilities
- Powerful AI technology
- Patent DNA Extraction
Browse by: Latest US Patents, China's latest patents, Technical Efficacy Thesaurus, Application Domain, Technology Topic, Popular Technical Reports.
© 2024 PatSnap. All rights reserved.Legal|Privacy policy|Modern Slavery Act Transparency Statement|Sitemap|About US| Contact US: help@patsnap.com