Method for separating copper and molybdenum from slime-containing sulfur-containing low-grade copper-molybdenum ore
A separation method and technology for copper-molybdenum ore, which are applied in solid separation, wet separation, chemical instruments and methods, etc., can solve the problems of reducing the recovery rate of copper-molybdenum mixed separation, unfavorable production efficiency, and difficulty in separation of copper and molybdenum.
- Summary
- Abstract
- Description
- Claims
- Application Information
AI Technical Summary
Problems solved by technology
Method used
Image
Examples
Embodiment 1
[0038] A copper-molybdenum separation method for low-grade copper-molybdenum ore containing sludge and sulfur. The process flow of the method is: grinding-copper-molybdenum mixed flotation process-desilting and desulfurization process-copper-molybdenum separation flotation process, wherein each process The specific process is as follows:
[0039] The copper-molybdenum mixed flotation process includes a mixed flotation roughing process, a mixed flotation sweeping process and a mixed flotation beneficiation process. The tailings after the mixed flotation roughing process enter the mixed flotation sweeping process. The mixed-float coarse concentrate enters the mixed-flotation concentration process, and the mixed-float concentrate after the mixed-flotation concentration process enters the desilting and desulfurization process.
[0040] Preferably, the copper-molybdenum mixed flotation process includes two mixed flotation roughing processes, two mixed flotation sweeping processes, and t...
Embodiment 2
[0052] A copper-molybdenum separation method for low-grade copper-molybdenum ore containing sludge and sulfur. The process flow of the method is: grinding-copper-molybdenum mixed flotation process-desilting and desulfurization process-copper-molybdenum separation flotation process, wherein each process The specific process is as follows:
[0053] The copper-molybdenum mixed flotation process includes a mixed flotation roughing process, a mixed flotation sweeping process and a mixed flotation beneficiation process. The tailings after the mixed flotation roughing process enter the mixed flotation sweeping process. The mixed-float coarse concentrate enters the mixed-flotation concentration process, and the mixed-float concentrate after the mixed-flotation concentration process enters the desilting and desulfurization process.
[0054] Preferably, the copper-molybdenum mixed flotation process includes two mixed flotation roughing processes, two mixed flotation sweeping processes, and t...
Embodiment 3
[0066] A copper-molybdenum separation method for low-grade copper-molybdenum ore containing sludge and sulfur. The process flow of the method is: grinding-copper-molybdenum mixed flotation process-desilting and desulfurization process-copper-molybdenum separation flotation process, wherein each process The specific process is as follows:
[0067] The copper-molybdenum mixed flotation process includes a mixed flotation roughing process, a mixed flotation sweeping process and a mixed flotation beneficiation process. The tailings after the mixed flotation roughing process enter the mixed flotation sweeping process. The mixed-float coarse concentrate enters the mixed-flotation concentration process, and the mixed-float concentrate after the mixed-flotation concentration process enters the desilting and desulfurization process.
[0068] Preferably, the copper-molybdenum mixed flotation process includes two mixed flotation roughing processes, two mixed flotation sweeping processes, and t...
PUM
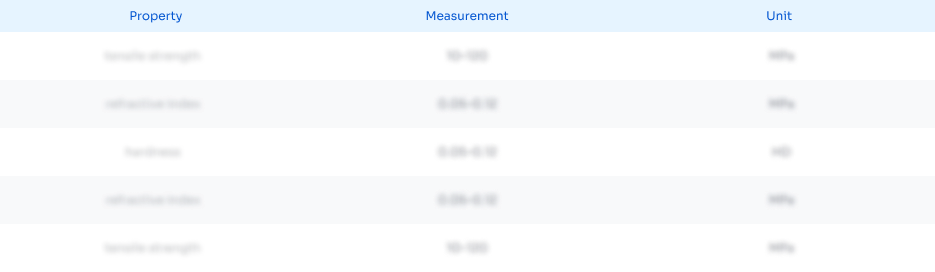
Abstract
Description
Claims
Application Information

- R&D
- Intellectual Property
- Life Sciences
- Materials
- Tech Scout
- Unparalleled Data Quality
- Higher Quality Content
- 60% Fewer Hallucinations
Browse by: Latest US Patents, China's latest patents, Technical Efficacy Thesaurus, Application Domain, Technology Topic, Popular Technical Reports.
© 2025 PatSnap. All rights reserved.Legal|Privacy policy|Modern Slavery Act Transparency Statement|Sitemap|About US| Contact US: help@patsnap.com