Preparation method for metal deactivator applied to catalytic cracking, and metal deactivator prepared by using same
A metal deactivator and catalytic cracking technology, applied in catalyst protection, chemical instruments and methods, physical/chemical process catalysts, etc., can solve problems such as poor product stability, complicated process, time-consuming and energy-consuming, and achieve low cost, The preparation process is simple and the economic benefit is remarkable
- Summary
- Abstract
- Description
- Claims
- Application Information
AI Technical Summary
Problems solved by technology
Method used
Image
Examples
preparation example Construction
[0016] The first aspect of the present invention: provide a kind of preparation method of catalytic cracking metal deactivator, this method comprises: a, antimony trioxide, hydroxy carboxylic acid, rare earth salt, pH adjusting agent and water are mixed, at a temperature of 20- The first product is obtained by reacting at 90°C for 30-60 minutes, wherein the mass ratio of antimony trioxide, hydroxycarboxylic acid, rare earth salt, pH regulator and water is 1:(2-4):( 0.1-0.6): (0.6-1.2): (2-10); b. Mix the oxidant with the first product obtained in step a, and react in a closed container at a temperature of 100-150°C 1- After 2 hours, a catalytic cracking metal passivator was obtained, wherein the mass ratio of the oxidant to antimony trioxide was (0.4-1.1):1. It should be noted that, since the catalytic cracking metal passivator prepared by the method of the present invention is generally used in the form of an aqueous solution after adding water for dissolution, in the prepara...
Embodiment 1
[0027] Add 3kg of ethanolamine, 10kg of tartaric acid, 5kg of antimony trioxide, 0.5kg of lanthanum carbonate and 50kg of deionized water into the reactor, stir at room temperature for 30 minutes, then add 2kg of 30% by mass hydrogen peroxide dropwise, and then close the reactor and heat it React at 100°C for 1 hour, then cool out of the kettle to obtain a catalytic cracking metal passivator, the product is clear and transparent, and the pH value is 7.0.
Embodiment 2
[0029] Add 3.6kg of triethanolamine, 12kg of citric acid, 3kg of antimony trioxide, 1.8kg of lanthanum nitrate and 6kg of deionized water into the reaction kettle, stir at room temperature, raise the temperature to 90°C and stir for 60 minutes, then add the total amount of After adding 2kg of benzoyl peroxide, close the reactor and heat it to 150°C for 1 hour, then cool it out of the reactor to obtain a catalytic cracking metal passivator. The product is clear and transparent, and the pH value is 7.8.
PUM
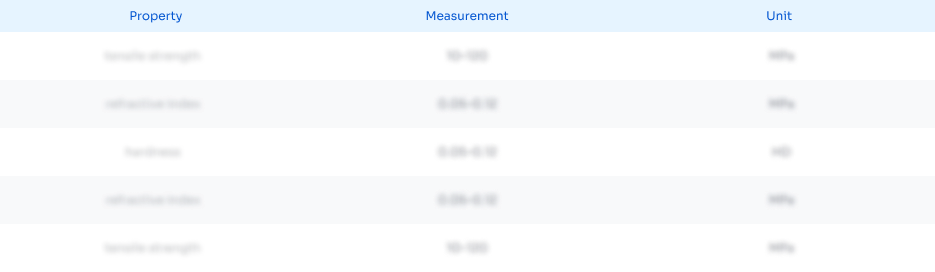
Abstract
Description
Claims
Application Information

- R&D
- Intellectual Property
- Life Sciences
- Materials
- Tech Scout
- Unparalleled Data Quality
- Higher Quality Content
- 60% Fewer Hallucinations
Browse by: Latest US Patents, China's latest patents, Technical Efficacy Thesaurus, Application Domain, Technology Topic, Popular Technical Reports.
© 2025 PatSnap. All rights reserved.Legal|Privacy policy|Modern Slavery Act Transparency Statement|Sitemap|About US| Contact US: help@patsnap.com