Liquid fuel cutting torch control valve and automatic-cutting cutting torch
An automatic cutting and liquid fuel technology, applied in valve details, multi-way valves, valve devices, etc., can solve the problems of large waste, tempering and flashing, and the inability to realize standardization and automation, etc., to achieve precise control and sufficient fuel combustion Effect
- Summary
- Abstract
- Description
- Claims
- Application Information
AI Technical Summary
Problems solved by technology
Method used
Image
Examples
Embodiment 1
[0087] Figure 19 Some process holes are drawn in the middle, such as the second gun head mixed oxygen channel 4-6 and the second gun head hyperbaric oxygen channel 4-5, both of which are right-angle bent channels and also include two passages, which need to be connected to the body To start perforating the outer wall of the device, the formation of each channel must leave a process hole on the outer wall of the connecting body, and these process holes need to be blocked later.
[0088] Such as Figure 1-Figure 19 As shown,
[0089] An automatic cutting torch, comprising the above-mentioned control valve 1 and a cutting unit 4, the cutting unit 4 and the control valve 1 are connected through a hyperbaric oxygen pipe 2 and a mixed oxygen pipe 3, the hyperbaric oxygen pipe 2 and the The mixed oxygen pipes 3 are all hoses; the second valve body hyperbaric oxygen channels 1-14 and the valve body mixed oxygen channels 1-17 are respectively connected to the cutting unit 4 through the hyp...
Embodiment 2
[0102] The difference from embodiment 1 lies in: Picture 20 As shown, the hyperbaric oxygen interface 4-1 and the mixed oxygen interface 4-2 are axially consistent, and the hyperbaric oxygen interface 4-1 and the mixed oxygen interface 4-2 are axially consistent with the connecting body. , The second torch head hyperbaric oxygen passage 4-6 and the second torch head mixed oxygen passage 4-5 are both bent channels, and the axial direction of the mixed oxygen flow regulating valve is the same as that of the torch head body The axis is vertical.
[0103] The working principle of the present invention is as follows:
[0104] Rotate the valve stem 1-2 to Figure 8-10 When shown, the marbles in the first high-pressure oxygen passage, the first valve body preheating oxygen passage, and the first valve body fuel passage are not pushed open, and the high pressure oxygen, preheating oxygen and fuel cannot pass through. At this time, the cutting torch Is closed.
[0105] Rotate the valve ste...
PUM
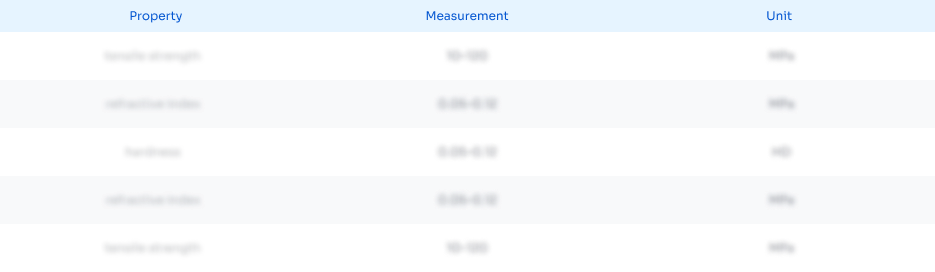
Abstract
Description
Claims
Application Information

- R&D Engineer
- R&D Manager
- IP Professional
- Industry Leading Data Capabilities
- Powerful AI technology
- Patent DNA Extraction
Browse by: Latest US Patents, China's latest patents, Technical Efficacy Thesaurus, Application Domain, Technology Topic, Popular Technical Reports.
© 2024 PatSnap. All rights reserved.Legal|Privacy policy|Modern Slavery Act Transparency Statement|Sitemap|About US| Contact US: help@patsnap.com