Preparation of lignin nano-carbon fibers for supercapacitor
A technology of supercapacitor and nano carbon fiber, which is applied in the direction of hybrid capacitor electrodes, etc., to achieve the effect of good flexibility, wide source and low price
- Summary
- Abstract
- Description
- Claims
- Application Information
AI Technical Summary
Problems solved by technology
Method used
Image
Examples
Embodiment 1
[0020] Take by weighing nitrogen, nitrogen-dimethylformamide (DMF) 8g as solvent, take by weighing alkali lignin 1.6g, take by weighing polyvinylpyrrolidone (PVP) 0.4g, wherein the ratio of polyvinylpyrrolidone (PVP) to alkali lignin It is 1:4. Dissolve alkali lignin in nitrogen, nitrogen-dimethylformamide (DMF), stir for 30 minutes, then add polyvinylpyrrolidone (PVP), and continue stirring for 4 hours to obtain a spinning dope with a uniform mass fraction of 20%. Electrospinning was carried out, and the spinning parameters were as follows: the flow rate of the spinning solution was 0.5ml / h, the applied voltage was 10kV, and the receiving distance was 15cm. Transfer the obtained as-spun fiber film into a tube furnace, raise the temperature to 150°C at a heating rate of 0.2°C / min and keep it for 20 hours in an air atmosphere, then raise the temperature to 360°C at a heating rate of 3°C / min and hold it for 5 hours Carry out pre-oxidation treatment; then raise the temperature t...
Embodiment 2
[0022] Take by weighing nitrogen, nitrogen-dimethylformamide (DMF) 8.5g as solvent, take by weighing alkali lignin 1g, take by weighing polyethylene oxide (PEO) 0.5g, wherein polyethylene oxide (PEO) and alkali The ratio of lignin is 1:2. Dissolve alkali lignin in DMF, stir for 30 min, add polyethylene oxide (PEO), and continue stirring for 4 h to obtain a spinning dope with a uniform mass fraction of 15%. Electrospinning was carried out, and the spinning parameters were as follows: the flow rate of the spinning solution was 2ml / h, the applied voltage was 15kV, and the receiving distance was 20cm. Transfer the obtained as-spun fiber film into a tube furnace, raise the temperature to 160°C at a heating rate of 0.8°C / min and keep it for 24 hours in an air atmosphere, then raise the temperature to 320°C at a heating rate of 1.5°C / min and hold it for 4 hours Carry out pre-oxidation treatment; then raise the temperature to 800°C at a heating rate of 3°C / min under a nitrogen atmosp...
Embodiment 3
[0024] Weigh 7.5 g of distilled water as a solvent, weigh 1.25 g of lignosulfonate, and weigh 1.25 g of polyvinylpyrrolidone (PVP), wherein the ratio of polyvinylpyrrolidone (PVP) to lignosulfonate is 1:1. Dissolve lignosulfonate in distilled water, stir for 30 minutes, add polyvinylpyrrolidone (PVP), and continue stirring for 4 hours to obtain a spinning dope with a uniform mass fraction of 25%. Electrospinning was carried out, and the spinning parameters were as follows: the flow rate of the spinning solution was 1 ml / h, the applied voltage was 20 kV, and the receiving distance was 25 cm. Transfer the obtained as-spun fiber film into a tube furnace, raise the temperature to 180°C at a heating rate of 1.2°C / min and keep it for 30 hours in an air atmosphere, then raise the temperature to 350°C at a heating rate of 0.2°C / min and keep it for 6 hours Carry out pre-oxidation treatment; then raise the temperature to 800°C at a heating rate of 3°C / min under a nitrogen atmosphere, an...
PUM
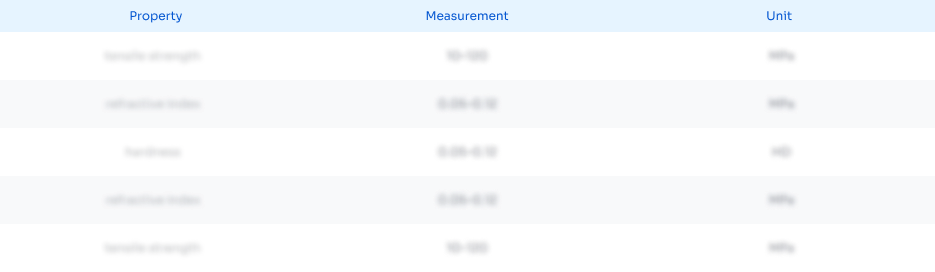
Abstract
Description
Claims
Application Information

- Generate Ideas
- Intellectual Property
- Life Sciences
- Materials
- Tech Scout
- Unparalleled Data Quality
- Higher Quality Content
- 60% Fewer Hallucinations
Browse by: Latest US Patents, China's latest patents, Technical Efficacy Thesaurus, Application Domain, Technology Topic, Popular Technical Reports.
© 2025 PatSnap. All rights reserved.Legal|Privacy policy|Modern Slavery Act Transparency Statement|Sitemap|About US| Contact US: help@patsnap.com