Preparation method for permanently antistatic and conductive EVA
An anti-static and permanent technology, applied in the field of conductive materials and anti-static, can solve the problems of large loss of electrical properties of conductive carbon black, excessive temperature rise of the melt, affecting the dispersibility of materials, etc.
- Summary
- Abstract
- Description
- Claims
- Application Information
AI Technical Summary
Problems solved by technology
Method used
Image
Examples
Embodiment 1
[0026] A preparation method of permanent antistatic and conductive EVA, the specific steps are: (1) put LDPE, EVA and calcium powder into an internal mixer for stirring, raise the temperature to 95-105°C, and start the temperature control system of the internal mixer.
[0027] (2) Keep the temperature at 95-105°C, put conductive carbon black, aromatic oil, crosslinking agent and zinc oxide into the internal mixer, continue stirring, and raise the temperature of the internal mixer to 110-120°C.
[0028] (3) Keep the temperature at 110-120°C, add foaming agent to the internal mixer, turn off the temperature control system of the internal mixer, and continue stirring to raise the temperature to 125°C.
[0029] (4) Material discharge, put the material into the 18" open mill and pass it twice, and then go to the 16" open mill to discharge the sheet, and finally go to the press to foam to obtain the finished product.
[0030] Step (1) Put LDPE, EVA and calcium powder into the intern...
Embodiment 2
[0040]A preparation method of permanent antistatic and conductive EVA, the steps are as follows: (1) Put 35 parts of LDPE2426H, 35 parts of EVA5110J and 4 parts of calcium powder into the internal mixer, press the cover to the bottom, and stir the raw materials When the temperature of the internal mixer is 100°C, turn on the water temperature control system of the internal mixer.
[0041] (2) Put 1.4 parts of aromatic oil in PE bags, 6.5 parts of conductive carbon black in PE bags, 1 part of zinc oxide, 3 parts of zinc stearate and 0.8 parts of crosslinking agent DCP into the hopper, and Press the pressure cover to the mouth of the hopper, and after stirring for 30 seconds, press down the pressure cover to the bottom. After 60 seconds, lift the pressure cover, and sweep the carbon black and other powder materials on the pressure cover and around the hopper into the hopper. Press down on the pressure cap until it reaches temperature. Afterwards, when the temperature of the int...
Embodiment 3
[0046] A preparation method of permanent antistatic and conductive EVA, the specific steps are the same as those in Examples 1 and 2, the difference is: conductive / antistatic EVA material, in parts by weight: LDPE2426H: 30 parts, EVA5110J: 40 parts, calcium Powder: 12 parts, aromatic hydrocarbon oil: 1.6 parts, conductive carbon black: 6 parts, crosslinking agent DCP: 0.7 parts, zinc oxide: 1.5 parts, zinc stearate: 3.5 parts and blowing agent AC: 3.8 parts.
[0047] The product obtained by the preparation method can be permanently antistatic and conductive, and has good surface controllability, smooth surface and no holes. The solution of this embodiment has particularly good performance.
PUM
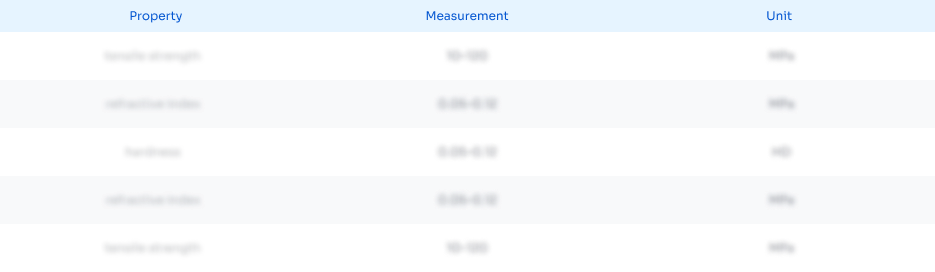
Abstract
Description
Claims
Application Information

- R&D
- Intellectual Property
- Life Sciences
- Materials
- Tech Scout
- Unparalleled Data Quality
- Higher Quality Content
- 60% Fewer Hallucinations
Browse by: Latest US Patents, China's latest patents, Technical Efficacy Thesaurus, Application Domain, Technology Topic, Popular Technical Reports.
© 2025 PatSnap. All rights reserved.Legal|Privacy policy|Modern Slavery Act Transparency Statement|Sitemap|About US| Contact US: help@patsnap.com