Method for preparing single-piece talc powder
A talcum powder and monolithic technology, applied in chemical instruments and methods, silicates, fibrous fillers, etc., can solve the problems of talcum powder damage, affecting the application of talc powder, uncontrollable force of talc powder particles, etc.
- Summary
- Abstract
- Description
- Claims
- Application Information
AI Technical Summary
Problems solved by technology
Method used
Image
Examples
Embodiment 1
[0026] (1) In parts by weight, add 10 parts of talc powder and 1 part of titanate coupling agent to a high-speed mixer, control the speed at 800 rpm, and disperse for 15 minutes to obtain a premix;
[0027] (2) Add the premix obtained in step (1) and the foaming agent composed of sodium lauryl sulfate, ammonium oxide, and water mixed in a mass ratio of 1:2:1 into a rotary homogenizer, and rotate The speed of the homogenizer is controlled at 1000rpm, the temperature is 60°C, and the talcum powder is peeled off step by step under the shearing action of the rotating blade to obtain the primary product of monolithic talc powder;
[0028] (3) The monolithic talc primary product obtained in step (2) is washed with water and acetone respectively and dried to obtain monolithic talc.
Embodiment 2
[0030] (1) In parts by weight, 12 parts of talcum powder and 1 part of aluminate coupling agent were added to a high-speed mixing mixer, the speed was controlled at 1200 rpm, and the premix was obtained by dispersing for 20 minutes;
[0031] (2) Add the premix obtained in step (1) and the foaming agent composed of sodium lauryl sulfate, ammonium oxide, and water mixed in a mass ratio of 1:3:2 into a rotary homogenizer, and rotate The speed of the homogenizer is controlled at 3000rpm, the temperature is 80°C, and the talcum powder is peeled off step by step under the shearing action of the rotating blade to obtain the primary product of monolithic talc powder;
[0032] (3) The monolithic talc primary product obtained in step (2) is washed with water and acetone respectively and dried to obtain monolithic talc.
Embodiment 3
[0034] (1) In parts by weight, 20 parts of talcum powder and 1 part of silane coupling agent are added to a high-speed mixing mixer, the speed is controlled at 1500 rpm, and the premix is obtained by dispersing for 30 minutes;
[0035] (2) Add the premix obtained in step (1) and the foaming agent composed of sodium lauryl sulfate, ammonium oxide, and water mixed in a mass ratio of 1:5:4 into a rotary homogenizer, and rotate The speed of the homogenizer is controlled at 5000rpm, the temperature is 100°C, and the talc powder is peeled off step by step under the shearing action of the rotating blade to obtain the primary product of monolithic talc powder;
[0036] (3) The monolithic talc primary product obtained in step (2) is washed with water and acetone respectively and dried to obtain monolithic talc.
PUM
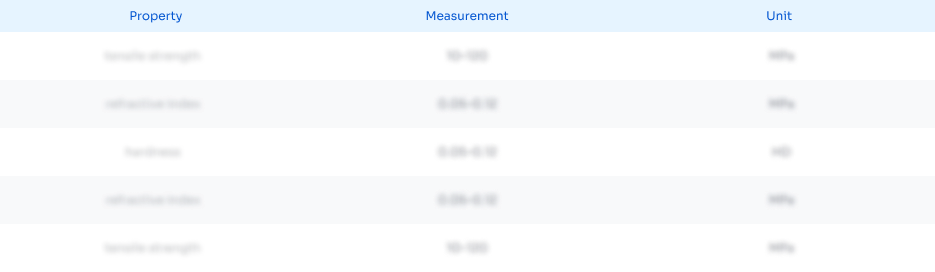
Abstract
Description
Claims
Application Information

- R&D
- Intellectual Property
- Life Sciences
- Materials
- Tech Scout
- Unparalleled Data Quality
- Higher Quality Content
- 60% Fewer Hallucinations
Browse by: Latest US Patents, China's latest patents, Technical Efficacy Thesaurus, Application Domain, Technology Topic, Popular Technical Reports.
© 2025 PatSnap. All rights reserved.Legal|Privacy policy|Modern Slavery Act Transparency Statement|Sitemap|About US| Contact US: help@patsnap.com