Rubber plastic and multiwalled carbon nanotube compound elastic matrix and preparation method thereof
A technology of multi-walled carbon nanotubes and elastic substrates is applied in the fields of rubber-plastic and multi-walled carbon nanotube composite elastic substrates and their preparation, improving quality, and modifying and optimizing the main material of textile aprons, and can solve the problem of shortening spinning aprons. The problems of service life, tearing, and broken ends increase, so as to achieve the effect of improving running stability and wear resistance, strong resistance to thermal deformation, and small thermal expansion coefficient
- Summary
- Abstract
- Description
- Claims
- Application Information
AI Technical Summary
Problems solved by technology
Method used
Image
Examples
Embodiment 1
[0024] Embodiment 1 A kind of composite elastic matrix of rubber-plastic and multi-walled carbon nanotubes
[0025] Parts by weight are as follows: 100 parts of nitrile rubber, 45 parts of high-polymerization PVC, 30 parts of multi-walled carbon nanotubes (former powder), 18 parts of plasticizer DOP, 1.5 parts of stabilizer dibutyltin laurate, lubricating and dispersing agent mustard 3 parts of acid acyl, 1.5 parts of antioxidant 2246-S and 1 part of antioxidant RD.
[0026] (1) Prefabricated dispersion: first weigh high-polymerization degree PVC, multi-walled carbon nanotubes, lubricating dispersant, 1.5 parts of antioxidant, and 1 part of anti-aging agent according to the weight ratio, put them into a vertical plastic mixer and stir for 2 minutes , then take the stabilizer and plasticizer by weight ratio and add to the mixer and stir for 4 minutes, control the discharge temperature to be 60°C, after stirring, pack it into bags and cool it for standby;
[0027] (2) Mixing th...
Embodiment 2
[0028] Embodiment 2 A composite elastic matrix of rubber, plastic and multi-walled carbon nanotubes
[0029] 100 parts of nitrile rubber, 60 parts of high-polymerization PVC, 25 parts of multi-walled carbon nanotubes, 22 parts of plasticizer, 2 parts of stabilizer, 3 parts of lubricating and dispersing agent, 2 parts of antioxidant and 1.5 parts of anti-aging agent.
[0030] (1) Prefabricated dispersion: first weigh high-polymerization degree PVC, multi-walled carbon nanotubes, lubricating dispersant, 1.5 parts of antioxidant, and 1 part of anti-aging agent according to the weight ratio, put them into a vertical plastic mixer and stir for 3 minutes , and then take the stabilizer and plasticizer according to the weight ratio, add them to the mixer and stir for 5 minutes, control the discharge temperature to 65 ° C, and pack them into bags for cooling after stirring;
[0031] (2) Mixing thermal plasticization: first weigh the nitrile rubber in the first stage of plastication acc...
Embodiment 3
[0032] Embodiment 3 A composite elastic matrix of rubber, plastic and multi-walled carbon nanotubes
[0033] The formula ratio is as follows in parts by weight: 100 parts of nitrile rubber, 75 parts of high-polymerization PVC, 20 parts of multi-walled carbon nanotubes, 125 parts of plasticizer, 2.5 parts of stabilizer, 2 parts of lubricating and dispersing agent, 1 part of antioxidant 2 parts and 2 parts of anti-aging agent.
[0034] (1) Prefabricated dispersion: first weigh high-polymerization degree PVC, multi-walled carbon nanotubes, lubricating dispersant, 1.5 parts of antioxidant, and 1 part of anti-aging agent according to the weight ratio, put them into a vertical plastic mixer and stir for 4 minutes , and then take the stabilizer and plasticizer according to the weight ratio, add them to the mixer and stir for 6 minutes, control the discharge temperature to 70 ° C, and pack them into bags for cooling after stirring;
[0035] (2) Mixing thermal plasticization: first we...
PUM
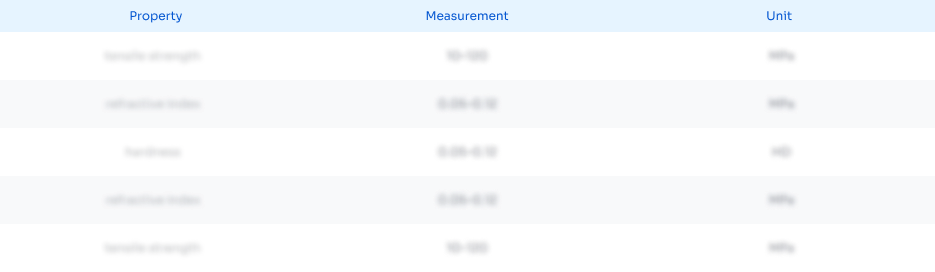
Abstract
Description
Claims
Application Information

- R&D Engineer
- R&D Manager
- IP Professional
- Industry Leading Data Capabilities
- Powerful AI technology
- Patent DNA Extraction
Browse by: Latest US Patents, China's latest patents, Technical Efficacy Thesaurus, Application Domain, Technology Topic, Popular Technical Reports.
© 2024 PatSnap. All rights reserved.Legal|Privacy policy|Modern Slavery Act Transparency Statement|Sitemap|About US| Contact US: help@patsnap.com