Jun porcelain and preparation method thereof
A production method, the technology of Jun porcelain, applied to clay products, other household utensils, household utensils, etc., can solve the problems of uneven glazing and difficult quality control, so as to achieve vivid and colorful glazed surface, stable and controllable glazing quality, Pure glaze effect
- Summary
- Abstract
- Description
- Claims
- Application Information
AI Technical Summary
Problems solved by technology
Method used
Examples
Embodiment 1
[0028] A method for making Jun porcelain, comprising:
[0029] Step 1. Bake the qualified plain tires that have been cleaned of dust at 35-40°C for 3 hours;
[0030] Step 2. Immediately immerse the baked plain tire in the glaze slurry for glazing;
[0031] Step 3, put the glazed plain tire into the kiln for glaze firing, wherein, the glaze firing includes:
[0032] Pre-firing: Put the plain tire into the kiln, keep the kiln door open 2-3cm, then ignite and fire, so that the temperature in the furnace will rise from room temperature to 590-600°C evenly within 2 hours, and then close the kiln door tightly ;
[0033] Firing in an oxidizing atmosphere: the temperature in the furnace is evenly raised from 590-600°C to 1000-1050°C within 4 hours, and fresh air is supplied to the kiln to ensure sufficient oxygen in the kiln;
[0034] Firing in reducing atmosphere: Make the temperature in the furnace rise uniformly from 1000-1050°C to 1400-1500°C within 8 hours, and stop supplying ...
Embodiment 2
[0043] A method for making Jun porcelain, comprising:
[0044] Step 1. Bake the qualified plain tire at 35-40°C for 3.5 hours after dust removal;
[0045] Step 2. Immediately immerse the baked plain tire in the glaze slurry for glazing;
[0046] Step 3, put the glazed plain tire into the kiln for glaze firing, wherein, the glaze firing includes:
[0047] Pre-firing: Put the plain tire into the kiln, keep the kiln door open 2-3cm, then ignite and fire, so that the temperature in the furnace will rise from room temperature to 590-600°C evenly within 2 hours, and then close the kiln door tightly ;
[0048] Firing in an oxidizing atmosphere: the temperature in the furnace is raised uniformly from 590-600°C to 1000-1050°C within 4 hours, and fresh air is supplied to the kiln to ensure sufficient oxygen in the kiln;
[0049] Firing in a reducing atmosphere: Increase the temperature in the furnace from 1000-1050°C to 1400-1500°C evenly within 8 hours, and stop supplying fresh air to...
Embodiment 3
[0058] A method for making Jun porcelain, comprising:
[0059] Step 1. Bake the qualified plain tires that have been cleaned of dust at 35-40°C for 4 hours;
[0060] Step 2. Immediately immerse the baked plain tire in the glaze slurry for glazing;
[0061] Step 3, put the glazed plain tire into the kiln for glaze firing, wherein, the glaze firing includes:
[0062] Pre-firing: Put the plain tire into the kiln, keep the kiln door open 2-3cm, then ignite and fire, so that the temperature in the furnace will rise from room temperature to 590-600°C evenly within 2 hours, and then close the kiln door tightly ;
[0063] Firing in an oxidizing atmosphere: the temperature in the furnace is evenly raised from 590-600°C to 1000-1050°C within 4 hours, and fresh air is supplied to the kiln to ensure sufficient oxygen in the kiln;
[0064] Firing in reducing atmosphere: Make the temperature in the furnace rise uniformly from 1000-1050°C to 1400-1500°C within 8 hours, and stop supplying ...
PUM
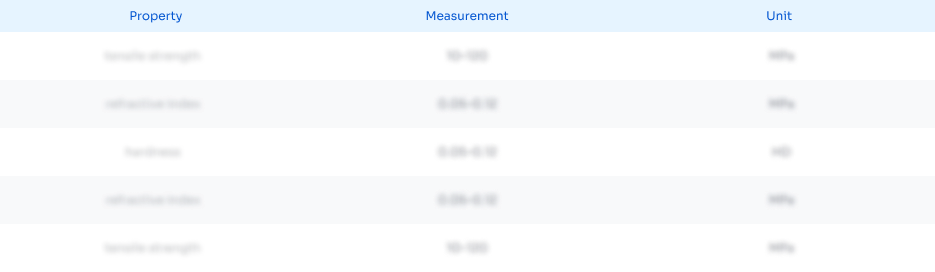
Abstract
Description
Claims
Application Information

- Generate Ideas
- Intellectual Property
- Life Sciences
- Materials
- Tech Scout
- Unparalleled Data Quality
- Higher Quality Content
- 60% Fewer Hallucinations
Browse by: Latest US Patents, China's latest patents, Technical Efficacy Thesaurus, Application Domain, Technology Topic, Popular Technical Reports.
© 2025 PatSnap. All rights reserved.Legal|Privacy policy|Modern Slavery Act Transparency Statement|Sitemap|About US| Contact US: help@patsnap.com