Molten iron dephosphorizing agent, refining agent, and dephosphorization method
A dephosphorization agent and refining agent technology, applied in the direction of improving process efficiency, manufacturing converters, etc., can solve problems such as limited reuse of slag
- Summary
- Abstract
- Description
- Claims
- Application Information
AI Technical Summary
Problems solved by technology
Method used
Image
Examples
Embodiment
[0067] The dephosphorization treatment using the converter was performed using various calcium ferrites shown in Table 1. For the conditions of dephosphorization treatment, [P] before dephosphorization is 0.1%, the injection time is 3-4 minutes, the loading alkalinity is 1.8, and the calcium ferrite usage is 10kg / t. The finished product [P] in the table is [P] in the slab stage. In addition, the state of splashing from the converter mouth during the dephosphorization spraying was investigated, and the case where the spraying was interrupted in the middle due to the spattering was regarded as "present", and the case where it was not interrupted was regarded as "absence". In addition, the input timing means the timing of injecting calcium ferrite into the converter, and it is set as "before charging molten iron" or "after charging molten iron".
[0068] [Table 1]
[0069]
[0070] It can be seen that No.1 to No.9 as examples of the present invention have achieved finished p...
PUM
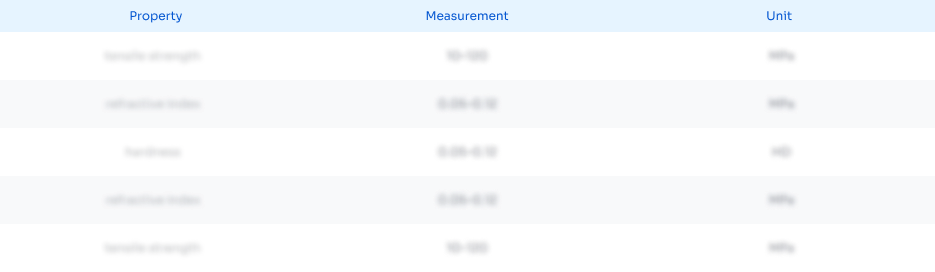
Abstract
Description
Claims
Application Information

- R&D Engineer
- R&D Manager
- IP Professional
- Industry Leading Data Capabilities
- Powerful AI technology
- Patent DNA Extraction
Browse by: Latest US Patents, China's latest patents, Technical Efficacy Thesaurus, Application Domain, Technology Topic, Popular Technical Reports.
© 2024 PatSnap. All rights reserved.Legal|Privacy policy|Modern Slavery Act Transparency Statement|Sitemap|About US| Contact US: help@patsnap.com