Continuous preparation technology of sulfur dioxide from fuming sulphuric acid and equipment thereof
A fuming sulfuric acid and sulfur dioxide technology, applied in sustainable manufacturing/processing, sulfur compounds, chemical industry, etc., can solve the problems of long process route, hidden safety hazards, high energy consumption, etc., and achieve simple process, low production and operation cost, high quality high effect
- Summary
- Abstract
- Description
- Claims
- Application Information
AI Technical Summary
Problems solved by technology
Method used
Image
Examples
Embodiment 1
[0032] 1) After the gas phase of the sulfuric acid production process 1, 2, and 3 converters is passed through the gas phase input line 1 into the nicotinic acid tower 2 for absorption, the gas phase enters the external absorption system to continue the absorption, and the liquid phase obtained by absorption is fuming sulfuric acid ( Concentration is 106%), enters in the circulation tank 3, is driven into the primary reaction tower 6 continuously through the mechanical pump A4, simultaneously, feeds liquid sulfur through the liquid sulfur pipeline A8 and reacts under 100 ℃, 0.05MPa, keeps the liquid sulfur all the time The state of sulfur deficiency; wherein, the mass ratio of liquid sulfur input to fuming sulfuric acid is 1:260;
[0033] 2) The reaction solution produced by the reaction in step 1) is continuously returned to the circulation tank 3 through the machine pump B5, wherein, in the reaction solution, the concentration of oleum is 104%;
Embodiment 2
[0037] 1) After the gas phase of the sulfuric acid production process 1, 2, and 3 converters is passed through the gas phase input line 1 into the nicotinic acid tower 2 for absorption, the gas phase enters the external absorption system to continue the absorption, and the liquid phase obtained by absorption is fuming sulfuric acid ( Concentration is 110%), enters in the circulating tank 3, is driven into the primary reaction tower 6 continuously through the mechanical pump A4, meanwhile, feeds the liquid sulfur through the liquid sulfur pipeline A8 and reacts under 70 ℃, normal pressure, keeps the liquid sulfur all the time The state of sulfur deficiency; wherein, the mass ratio of liquid sulfur to fuming sulfuric acid is 1:12;
[0038] 2) The reaction solution produced by the reaction in step 1) is continuously returned to the circulation tank 3 through the machine pump B5, wherein, in the reaction solution, the concentration of oleum is 106%;
[0039] 3) The mixed gas gener...
Embodiment 3
[0042] 1) After the gas phase of the sulfuric acid production process 1, 2, and 3 converters is passed through the gas phase input line 1 into the nicotinic acid tower 2 for absorption, the gas phase enters the external absorption system to continue the absorption, and the liquid phase obtained by absorption is fuming sulfuric acid ( Concentration is 102%), enters in the circulating tank 3, is driven into the primary reaction tower 6 continuously through the mechanical pump A4, simultaneously, feeds the liquid sulfur through the liquid sulfur pipeline A and reacts under 135 ℃, 0.1MPa, keeps the liquid sulfur all the time The state of sulfur deficiency; wherein, the mass ratio of liquid sulfur input to fuming sulfuric acid is 1:500;
[0043] 2) The reaction solution produced by the reaction in step 1) is continuously returned to the circulation tank 3 through the machine pump B5; wherein, in the reaction solution, the concentration of oleum is 101%;
[0044] 3) The mixed gas ge...
PUM
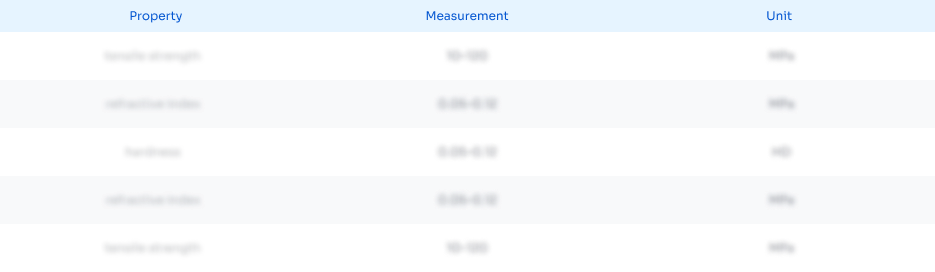
Abstract
Description
Claims
Application Information

- R&D Engineer
- R&D Manager
- IP Professional
- Industry Leading Data Capabilities
- Powerful AI technology
- Patent DNA Extraction
Browse by: Latest US Patents, China's latest patents, Technical Efficacy Thesaurus, Application Domain, Technology Topic, Popular Technical Reports.
© 2024 PatSnap. All rights reserved.Legal|Privacy policy|Modern Slavery Act Transparency Statement|Sitemap|About US| Contact US: help@patsnap.com