A kind of method that microreactor synthesizes methyl nitrite
A technology of methyl nitrite and microreactor, which is applied in nitrite preparation, chemical instruments and methods, chemical/physical/physical-chemical reactors, etc., can solve the problem of low reactor operation efficiency, increase reaction time and residence time Long and other problems, to achieve the effect of high gas-liquid mixing efficiency, simple capacity amplification, and low N2 content
- Summary
- Abstract
- Description
- Claims
- Application Information
AI Technical Summary
Problems solved by technology
Method used
Image
Examples
Embodiment 1
[0022] In the tubular reactor ① inlet NO / O 2 The molar ratio is 4, the gas phase N 2 The volume content is 40%, the pre-reaction temperature is normal temperature, and the reaction residence time is 10 minutes. Single-channel microreactor ②The hydraulic diameter is 1000 microns, and the gas phase space velocity is 13000h -1 , the methanol / NO molar ratio is 2, the microreactor reaction temperature is 50°C, and the system pressure is normal pressure, the gas phase outlet methyl nitrite volume content is 43%, based on O 2 The product yield was 84.6%.
Embodiment 2
[0024] In the tubular reactor ① inlet NO / O 2 The molar ratio is 5, the gas phase N 2 The volume content is 60%, the pre-reaction temperature is normal temperature, and the reaction residence time is 8 minutes. Single-channel microreactor ②The hydraulic diameter is 300 microns, and the gas phase space velocity is 50000h -1 , the methanol / NO molar ratio is 2, the reaction temperature of the microreactor is 30°C, and the system pressure is 0.2MPa, the volume content of methyl nitrite at the outlet of the gas phase is 27.3%, based on O 2 The product yield is 85.3%.
Embodiment 3
[0026] In the tubular reactor ① inlet NO / O 2 The molar ratio is 4, the gas phase N 2 The volume content is 60%, the pre-reaction temperature is 100°C, and the reaction residence time is 1.2s. Parallel multi-channel (parallel number 30) microreactor ②The hydraulic diameter is 1000 microns, and the gas phase space velocity is 50000h -1 , gas phase N 2 Volume content 60%, NO / O 2 =4, the methanol / NO molar ratio is 2, the reaction temperature of the microreactor is 30° C., and the system pressure is normal pressure, the volume content of methyl nitrite at the outlet of the gas phase is 31.6%, and the product yield based on oxygen is 80.2%.
PUM
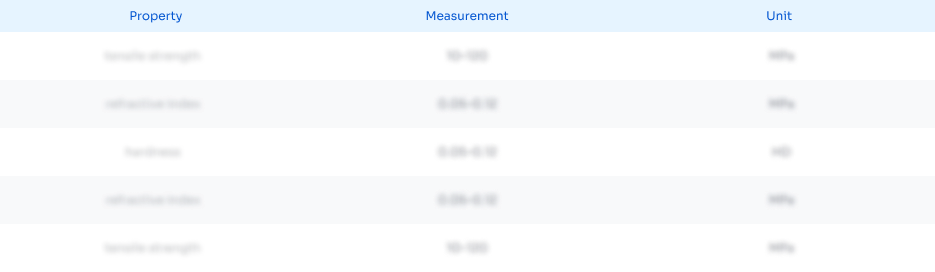
Abstract
Description
Claims
Application Information

- R&D
- Intellectual Property
- Life Sciences
- Materials
- Tech Scout
- Unparalleled Data Quality
- Higher Quality Content
- 60% Fewer Hallucinations
Browse by: Latest US Patents, China's latest patents, Technical Efficacy Thesaurus, Application Domain, Technology Topic, Popular Technical Reports.
© 2025 PatSnap. All rights reserved.Legal|Privacy policy|Modern Slavery Act Transparency Statement|Sitemap|About US| Contact US: help@patsnap.com