Preparation method of toughening conducting material
A conductive material and toughening technology, which is applied in the field of preparation of toughened conductive materials, can solve the problems of unstable mechanical properties of materials, decline of mechanical properties of materials, difficulty in processing and molding, etc., achieve excellent electrical conductivity and mechanical properties, and meet market demand Effect
- Summary
- Abstract
- Description
- Claims
- Application Information
AI Technical Summary
Problems solved by technology
Method used
Examples
Embodiment 1
[0019] S1: Weigh 5 parts of carbon fibers and 3 parts of carbon nanotubes into 50 parts of hydrochloric acid solution with a concentration of 2 mol / L, treat at 30°C for 1 hour, then ultrasonically stir for 1 hour, and filter to obtain a filter cake;
[0020] S2: Add 10 parts of N-methylolphthalimide and 8 parts of n-butyl isocyanate to the filter cake obtained in step S1, adjust the pH value to 7.5, and continue stirring for 30 minutes;
[0021] S3: Add 25 parts of polypropylene / polyethylene mixture to the substance obtained in step S2, the mass ratio of polypropylene and polyethylene is 1:1, mix and stir for 40min at a temperature of 70°C; then put it into a mold for thermocompression molding , the toughened conductive material can be obtained, wherein the hot pressing temperature is 180° C., the pressure is 15 MPa, and the holding time is 20 minutes.
Embodiment 2
[0023] S1: Weigh 10 parts of carbon fibers and 7 parts of carbon nanotubes into 60 parts of hydrochloric acid solution with a concentration of 5 mol / L, treat at 50°C for 3 hours, then ultrasonically stir for 2 hours, and filter to obtain a filter cake;
[0024] S2: Add 20 parts of N-methylolphthalimide and 15 parts of n-butyl isocyanate to the filter cake obtained in step S1, adjust the pH value to 8.5, and continue stirring for 40 minutes;
[0025] S3: Add 35 parts of polypropylene / polyethylene mixture to the material obtained in step S2, the mass ratio of polypropylene and polyethylene is 3:1, mix and stir for 60 minutes at a temperature of 80°C; then put it into a mold for thermocompression molding , the toughened conductive material can be obtained, wherein the hot pressing temperature is 200° C., the pressure is 20 MPa, and the holding time is 30 minutes.
Embodiment 3
[0027] S1: Weigh 7 parts of carbon fibers and 5 parts of carbon nanotubes and add them to 52 parts of hydrochloric acid solution with a concentration of 3mol / L, treat at a temperature of 35°C for 1.5h, then ultrasonically stir for 1.5h, and filter to obtain a filter cake;
[0028] S2: Add 12 parts of N-methylolphthalimide and 10 parts of n-butyl isocyanate to the filter cake obtained in step S1, adjust the pH value to 7.8, and continue stirring for 32 minutes;
[0029] S3: Add 30 parts of polypropylene / polyethylene mixture to the substance obtained in step S2, the mass ratio of polypropylene and polyethylene is 1.5:1, mix and stir for 45min at a temperature of 72°C; then put it into a mold for thermocompression molding , the toughened conductive material can be obtained, wherein the hot pressing temperature is 185° C., the pressure is 18 MPa, and the holding time is 22 minutes.
PUM
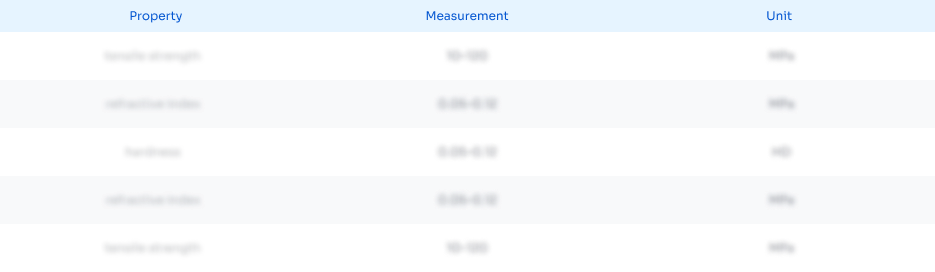
Abstract
Description
Claims
Application Information

- R&D Engineer
- R&D Manager
- IP Professional
- Industry Leading Data Capabilities
- Powerful AI technology
- Patent DNA Extraction
Browse by: Latest US Patents, China's latest patents, Technical Efficacy Thesaurus, Application Domain, Technology Topic, Popular Technical Reports.
© 2024 PatSnap. All rights reserved.Legal|Privacy policy|Modern Slavery Act Transparency Statement|Sitemap|About US| Contact US: help@patsnap.com