Superfine aluminum-calcium phosphate anticorrosion pigment preparation method
A technology of fine calcium aluminum phosphate and anti-corrosion pigment, which is applied in anti-corrosion coatings, inorganic pigment treatment, chemical instruments and methods, etc., to achieve the effect of improving solubility
- Summary
- Abstract
- Description
- Claims
- Application Information
AI Technical Summary
Problems solved by technology
Method used
Examples
Embodiment 1
[0018] a, weigh 0.78 g Al(OH) 3 (0.01 mol) and 1.7 mL of phosphoric acid (0.025 mol) with a density of 1.69 g / mL (to make the molar ratio of P and Al 2.5: 1), placed in a porcelain crucible, placed in a 90°C water bath and stirred for 15 min , until the mixture turns into a translucent viscous liquid; b, put the porcelain crucible in an oven at 90°C, and let the mixture continue to undergo neutralization reaction for 2 h; c, after the reaction of the mixture is complete, immediately transfer the porcelain crucible to 300°C In a muffle furnace, the condensation reaction was carried out for 4 h to obtain system A; d, 0.5 g CaCO 3 (0.005 mol) and 0.1 g of aluminate coupling agent used as a surface treatment agent were uniformly dispersed in a watering can filled with 20 mL of 60 °C deionized water to obtain dispersion system B; e, after the condensation reaction was completed, the Dispersion system B is sprayed on the hot aluminum tripolyphosphate condensate, and the condensate...
Embodiment 2
[0020] a, weigh 0.78 g Al(OH) 3 (0.01 mol) and 1.7 mL of phosphoric acid (0.025 mol) with a density of 1.69 g / mL (to make the molar ratio of P and Al 2.5: 1), placed in a porcelain crucible, placed in a 90 °C water bath and stirred for 15 min , until the mixture turns into a translucent viscous liquid; b, put the porcelain crucible in an oven at 90 °C, and let the mixture continue to undergo neutralization reaction for 2 h; c, after the reaction of the mixture is complete, transfer the porcelain crucible to a 320 °C oven In the muffle furnace, the condensation reaction was carried out for 2 h to obtain system A; d, 0.5 g CaCO 3(0.005 mol) and 0.1 g of aminosilane coupling agent used as a surface treatment agent were uniformly dispersed in a watering can filled with 20 mL of 60 °C deionized water to obtain dispersion system B; e, after the condensation reaction was completed, the dispersed System B is sprayed on the hot aluminum tripolyphosphate condensate, and the condensate ...
Embodiment 3
[0022] a, weigh 0.78 g Al(OH) 3 (0.01 mol) and 1.7 mL of phosphoric acid (0.025 mol) with a density of 1.69 g / mL (to make the molar ratio of P and Al 2.5: 1), placed in a porcelain crucible, placed in a 90 °C water bath and stirred for 15 min , until the mixture turns into a translucent viscous liquid; b, put the porcelain crucible in an oven at 90 °C, and let the mixture continue to undergo neutralization reaction for 2 h; c, after the reaction of the mixture is complete, transfer the porcelain crucible to a 290 °C oven In the muffle furnace, the condensation reaction was carried out for 4 h, and the system A was obtained; d, 0.5 g CaCO 3 (0.005 mol) and 0.1 g of phthalate coupling agent used as a surface treatment agent were uniformly dispersed in a watering can filled with 20 mL of 60 °C deionized water to obtain dispersion system B; e, after the condensation reaction was completed, immediately The dispersion system B is sprayed on the hot aluminum tripolyphosphate conden...
PUM
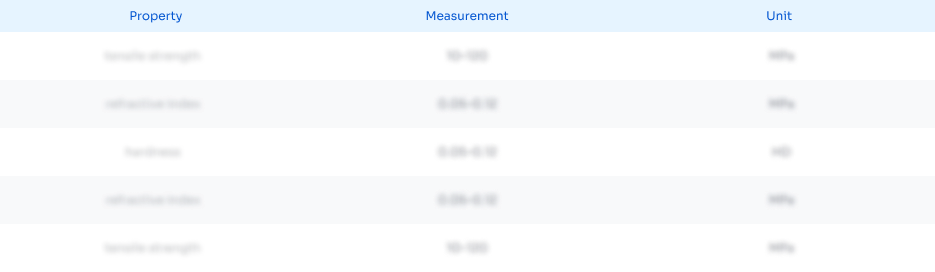
Abstract
Description
Claims
Application Information

- R&D Engineer
- R&D Manager
- IP Professional
- Industry Leading Data Capabilities
- Powerful AI technology
- Patent DNA Extraction
Browse by: Latest US Patents, China's latest patents, Technical Efficacy Thesaurus, Application Domain, Technology Topic, Popular Technical Reports.
© 2024 PatSnap. All rights reserved.Legal|Privacy policy|Modern Slavery Act Transparency Statement|Sitemap|About US| Contact US: help@patsnap.com