Method for continuously preparing block/star-shaped polymer on basis of tubular reaction device
A tubular reaction device and a star-shaped polymer technology are applied in the field of continuous preparation of block/star polymers based on a tubular reaction device, and can solve the problems of low conversion rate and complex method.
- Summary
- Abstract
- Description
- Claims
- Application Information
AI Technical Summary
Problems solved by technology
Method used
Image
Examples
Embodiment 1
[0043] The refined first monomer isoprene distilled from the raw material tank, the refined n-hexane distilled from the raw material tank and the n-butyllithium solution (concentration 1.6mol / L) were respectively adjusted according to the flow rate of 1L / H, 60L / H, 10mL / H enters the first static reactor from the respective raw material tanks, and reacts at 50°C for 120 minutes to obtain an active polymer; the inner diameter of the first static reactor is 3 mm, and the length is 20 meters. In a static reactor, the included angle of the first 5 meters of mixing blades is 90°, and the angle of the rear 15 meters of mixing blades is 45°;
[0044] The active polymer obtained is continuously entered into the second static reactor, and the coupling agent divinylbenzene in the second monomer or the coupling agent tank is added at the same time, the flow rate is 50mL / H, and the reaction is carried out at 50°C for 60min, the product After flowing out, the polyisoprene star-shaped polyme...
Embodiment 2
[0047] Isoprene, n-hexane and catalyst n-butyllithium (concentration 1.6mol / L) are respectively entered in the first static reactor according to the flow rate of 15L / H, 90L / H, and 150mL / H from respective raw material tanks, React at 50°C for 90 minutes to obtain an active polymer; the inner diameter of the first static reactor is 3 mm and the length is 20 meters. In the first static reactor, the angle of the first 5 meters of mixing blades is positive Intersection 90°, the angle of the last 15 meters of mixing blades is 45°;
[0048] The obtained active polymer is continuously put into the second static reactor, and the second monomer butadiene in the second monomer tank is added at the same time, the flow rate is 500mL / H, and the reaction is carried out at 50°C for 45min. After the product flows out, it is passed through methanol The block polymer is obtained after settling out; the inner diameter of the second static reactor is 3 millimeters, and the length is 12 meters. In ...
Embodiment 3
[0051] Isoprene, butadiene, n-hexane and catalyst n-butyllithium (concentration 1.6mol / L) are respectively according to the flow rate of 10L / H, 10L / H, 120L / H, 100mL / H from the respective raw material tanks Enter the first static reactor and react at 50°C for 60 minutes to obtain active polymer; the inner diameter of the first static reactor is 3 mm and the length is 20 meters. In the first static reactor, the first 5 The included angle of the mixing blade for 1m is 90°, and the angle of the mixing blade for the last 15m is 45°;
[0052] The active polymer obtained is continuously entered into the second static reactor, and the coupling agent divinylbenzene in the second monomer or the coupling agent tank is added at the same time, the flow rate is 500mL / H, and the reaction is carried out at 50°C for 30min, the product Obtain the star-shaped polymer after flowing out through methanol precipitation; The inner diameter of the second static reactor is 3 millimeters, and the length...
PUM
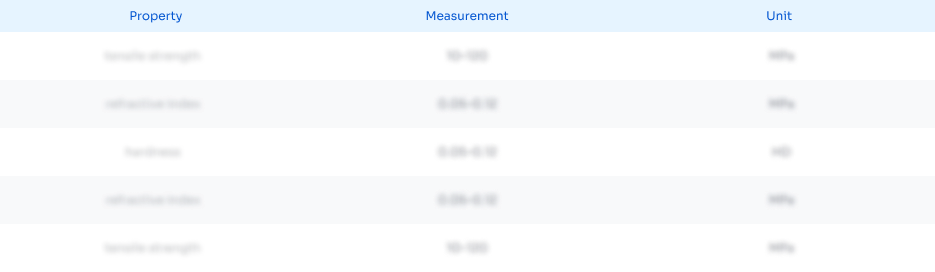
Abstract
Description
Claims
Application Information

- R&D
- Intellectual Property
- Life Sciences
- Materials
- Tech Scout
- Unparalleled Data Quality
- Higher Quality Content
- 60% Fewer Hallucinations
Browse by: Latest US Patents, China's latest patents, Technical Efficacy Thesaurus, Application Domain, Technology Topic, Popular Technical Reports.
© 2025 PatSnap. All rights reserved.Legal|Privacy policy|Modern Slavery Act Transparency Statement|Sitemap|About US| Contact US: help@patsnap.com