A method for recovering iron from 3-4 electric field dedusting ash of sintering head
A four-electric-field, iron-recycling technology, applied in chemical instruments and methods, wet separation, solid separation, etc., can solve problems such as insignificant and non-effective effects, achieve considerable economic benefits, simple technological process, and is suitable for promotion and popularization Effect
- Summary
- Abstract
- Description
- Claims
- Application Information
AI Technical Summary
Problems solved by technology
Method used
Examples
Embodiment 1
[0020] Embodiment 1, a method for reclaiming iron from sintering head three or four electric field dust removal, comprising the following steps:
[0021] 1) Slurry mixing: add dust from the three or four electric fields of the machine head into the mixing tank, add water at the same time, control the total liquid-solid ratio at 1.3, control the stirring speed at 120 rpm, and at the same time pass compressed air and Steam to obtain a uniformly dispersed slurry; specific liquid-solid ratio, specific rotational speed, and compressed air to make the slurry more uniform;
[0022] 2) Weak magnetic separation: the slurry is transported to the magnetic separator through the pipeline, and the magnetic field strength is controlled at 1500 Oersted ~, and the iron grade is 52.83% crude iron concentrate and tailings of weak magnetic separation; the slurry can be separated by weak magnetic separation Part of the iron in the iron is selected in advance to reduce the amount of subsequent proc...
Embodiment 2
[0024] Embodiment 2, a method for reclaiming iron from sintering head three or four electric field dust removal, comprising the following steps:
[0025] 1) Slurry mixing: Add dust from the three or four electric fields of the machine head into the mixing tank, add water at the same time, control the total liquid-solid ratio at 2.2, control the stirring speed at 240 rpm, and at the same time, pass compressed air and Steam to obtain a uniformly dispersed slurry; specific liquid-solid ratio, specific rotational speed, and compressed air to make the slurry more uniform;
[0026] 2) Weak magnetic separation: the slurry is transported to the magnetic separator through the pipeline, and the magnetic field strength is controlled at 2000 Oersted, and the iron grade is 56.69% crude iron concentrate and weak magnetic separation tailings; Part of the iron is selected in advance to reduce the amount of subsequent processing;
[0027] 3) Centrifugal separation: Send the weak magnetic sepa...
Embodiment 3
[0028] Embodiment 3, a method for recovering iron from sintering head three or four electric field dedusting, comprising the following steps:
[0029] 1) Slurry mixing: Add dust from the three or four electric fields of the machine head into the mixing tank, add water at the same time, control the total liquid-solid ratio at 1.8, control the stirring speed at 180 rpm, and at the same time pass compressed air and Steam to obtain a uniformly dispersed slurry; specific liquid-solid ratio, specific rotational speed, and compressed air to make the slurry more uniform;
[0030] 2) Weak magnetic separation: the slurry is transported to the magnetic separator through the pipeline, and the magnetic field strength is controlled at 1800 Oersted, and the iron grade is 54.76% crude iron concentrate and tailings of weak magnetic separation; Part of the iron is selected in advance to reduce the amount of subsequent processing;
[0031] 3) Centrifugal separation: send the weak magnetic separ...
PUM
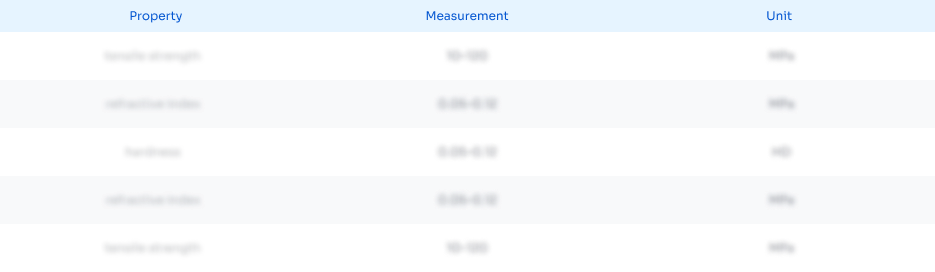
Abstract
Description
Claims
Application Information

- R&D Engineer
- R&D Manager
- IP Professional
- Industry Leading Data Capabilities
- Powerful AI technology
- Patent DNA Extraction
Browse by: Latest US Patents, China's latest patents, Technical Efficacy Thesaurus, Application Domain, Technology Topic, Popular Technical Reports.
© 2024 PatSnap. All rights reserved.Legal|Privacy policy|Modern Slavery Act Transparency Statement|Sitemap|About US| Contact US: help@patsnap.com