Metal mask plate and manufacturing method thereof
A metal mask and mask frame technology, which is applied in metal material coating process, semiconductor/solid-state device manufacturing, ion implantation and plating, etc. The number of times of use, low thermal expansion rate, and the effect of reducing production costs
- Summary
- Abstract
- Description
- Claims
- Application Information
AI Technical Summary
Problems solved by technology
Method used
Image
Examples
Embodiment Construction
[0031] The present invention will be further described below in conjunction with accompanying drawing.
[0032] see figure 1 , which is a schematic structural view of the metal mask of the present invention, wherein the metal mask of the present invention can be used for vapor deposition of an organic light-emitting display (OLED). Such as figure 1 As shown, the metal mask is a fine metal mask, which includes a mask frame 1, on which a diaphragm group with a mesh 3 is fixed, and a layer of magnetic film is arranged on the surface of the diaphragm group. Material coating 21.
[0033] In a specific embodiment of the present invention, the membrane set includes a plurality of membranes 2 with meshes 3 , wherein the plurality of membranes 2 are arranged on the mask frame 1 parallel to each other.
[0034] The mask frame 1 is a specially designed metal frame, which is used to fix the diaphragm 2. The diaphragm 2 is a metal diaphragm with a thickness of only tens of microns. The ...
PUM
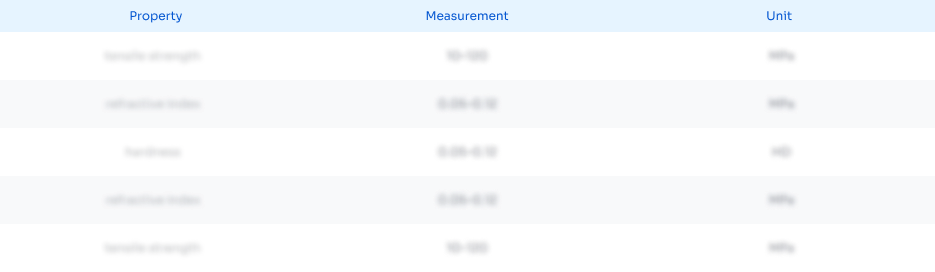
Abstract
Description
Claims
Application Information

- Generate Ideas
- Intellectual Property
- Life Sciences
- Materials
- Tech Scout
- Unparalleled Data Quality
- Higher Quality Content
- 60% Fewer Hallucinations
Browse by: Latest US Patents, China's latest patents, Technical Efficacy Thesaurus, Application Domain, Technology Topic, Popular Technical Reports.
© 2025 PatSnap. All rights reserved.Legal|Privacy policy|Modern Slavery Act Transparency Statement|Sitemap|About US| Contact US: help@patsnap.com