Environment-friendly enhanced composite building panel and preparation method thereof
A building board and reinforced technology, applied in the field of environmental protection reinforced composite building board and its preparation, can solve the problems of load-bearing, poor fire resistance, poor safety, easy aging, etc., and achieve excellent thermal insulation performance and mechanical properties. Performance, less consumables, good weather resistance
- Summary
- Abstract
- Description
- Claims
- Application Information
AI Technical Summary
Problems solved by technology
Method used
Examples
preparation example Construction
[0033] A method for preparing an environmentally friendly enhanced composite building board, the preparation steps are as follows:
[0034] S1: 37-40 parts of light active calcium carbonate, 15-23 parts of glass fiber, 8-10 parts of fly ash, 11-18 parts of wollastonite, 16-24 parts of recycled PVC, 13-17 parts of gypsum, 15-25 parts of butyl rubber, 6-10 parts of camphor wood powder, and 2-6 parts of magnesium oxide are respectively mechanically pulverized and ball-milled until the mesh number of each of the above-mentioned components is 200-300 orders, and set aside;
[0035] S2: Add the light activated calcium carbonate, glass fiber, fly ash, wollastonite, PVC recycled material, gypsum, butyl rubber, camphor wood powder and magnesium oxide pulverized in step S1 into the reaction kettle and stir evenly;
[0036] S3: In step S2, add 14-20 parts of polyurethane resin, 2-7 parts of diphenylmethane diisocyanate, 3-5 parts of polybutylene succinate, 11-14 parts of butyl propionate, ...
Embodiment 1
[0041] A method for preparing an environmentally friendly enhanced composite building board, the preparation steps are as follows:
[0042] S1: 40 parts of light active calcium carbonate, 15 parts of glass fiber, 10 parts of fly ash, 18 parts of wollastonite, 16 parts of recycled PVC material, 13 parts of gypsum, 15 parts of butyl rubber, 10 parts of camphor wood powder, 6 parts of magnesium oxide are respectively mechanically pulverized and ball milled, and pulverized until the mesh number of each of the above-mentioned components is 200-300 mesh, for subsequent use;
[0043] S2: Add the light activated calcium carbonate, glass fiber, fly ash, wollastonite, PVC recycled material, gypsum, butyl rubber, camphor wood powder and magnesium oxide pulverized in step S1 into the reaction kettle and stir evenly;
[0044] S3: In step S2, add 20 parts of polyurethane resin, 7 parts of diphenylmethane diisocyanate, 5 parts of polybutylene succinate, 14 parts of butyl propionate, 4 parts ...
Embodiment 2
[0047] A method for preparing an environmentally friendly enhanced composite building board, the preparation steps are as follows:
[0048] S1: 37 parts of light active calcium carbonate, 15 parts of glass fiber, 8 parts of fly ash, 11 parts of wollastonite, 16 parts of recycled PVC, 13 parts of gypsum, 15 parts of butyl rubber, 6 parts of camphor wood powder, 2 parts of magnesium oxide are respectively mechanically pulverized and ball-milled, and pulverized to the mesh number of each above-mentioned component is 200-300 mesh, for subsequent use;
[0049] S2: Add the light activated calcium carbonate, glass fiber, fly ash, wollastonite, PVC recycled material, gypsum, butyl rubber, camphor wood powder and magnesium oxide pulverized in step S1 into the reaction kettle and stir evenly;
[0050] S3: In step S2, add 14 parts of polyurethane resin, 2 parts of diphenylmethane diisocyanate, 3 parts of polybutylene succinate, 11 parts of butyl propionate, 3 parts of lubricant, 3 parts ...
PUM
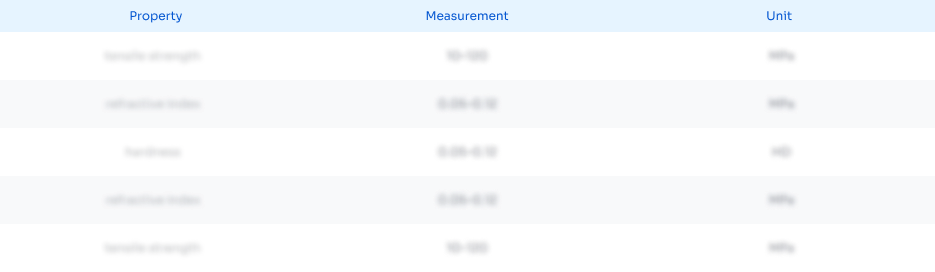
Abstract
Description
Claims
Application Information

- R&D Engineer
- R&D Manager
- IP Professional
- Industry Leading Data Capabilities
- Powerful AI technology
- Patent DNA Extraction
Browse by: Latest US Patents, China's latest patents, Technical Efficacy Thesaurus, Application Domain, Technology Topic, Popular Technical Reports.
© 2024 PatSnap. All rights reserved.Legal|Privacy policy|Modern Slavery Act Transparency Statement|Sitemap|About US| Contact US: help@patsnap.com