Sintered model resin infiltration method and vacuum infiltration device
A vacuum infiltration and resin technology, which is applied in processing and manufacturing, solid material additive processing, manufacturing auxiliary devices, etc., can solve problems such as unsatisfactory processing effect, and achieve the effect of easy automatic promotion, excellent mechanical properties, and smooth surface.
- Summary
- Abstract
- Description
- Claims
- Application Information
AI Technical Summary
Problems solved by technology
Method used
Image
Examples
Embodiment 1
[0029] This embodiment relates to a vacuum impregnation equipment, such as figure 1 As shown, it includes a tank body 4, a cover body 9 and a material rack 5, the cover body 9 covers the mouth of the tank body 4, the material rack 5 is arranged in the tank body 4, and the side of the tank body 4 is provided with a vacuum interface 2 , the compressed air interface 3 and the impregnating agent interface 6, the bottom of the tank body 4 is provided with a pressure relief valve interface 14, the inner side of the impregnating agent interface 6 is connected with an impregnating agent hose 7, and one end of the impregnating agent hose 7 is set on the top of shelf 5.
[0030] The lid body 9 is tightly closed with the tank body 4 through the locking cylinder 8 .
[0031] The top of the cover body 9 is provided with a pressure sensor 10 , a safety valve port 11 , a pressure gauge 13 and an observation window 12 .
[0032] The upper outer side of the tank body 4 is provided with a tan...
Embodiment 2
[0034] This embodiment relates to a method for impregnating using the vacuum impregnation equipment of Embodiment 1, which includes the following steps:
[0035] 1. The polystyrene model is formed by laser sintering 3D printing process, and the dust on the surface of the model is cleaned with a special blower;
[0036] 2. Calculate the amount of impregnating agent required according to the volume of the tank and the size of the polystyrene model, mix the epoxy resin, amine curing agent and reactive diluent at a ratio of 1:0.5:0.3, and then put it on the booster electric mixer Stir evenly to prepare a sufficient amount of post-treatment agent for impregnation;
[0037] 3. Check whether the control valves and air source pressure of the impregnation equipment are normal, and whether the interfaces are unobstructed, then put the polystyrene model that has removed the surface dust on the material rack, cover the pressure tank cover, and start the locking cylinder to lock the tank ...
PUM
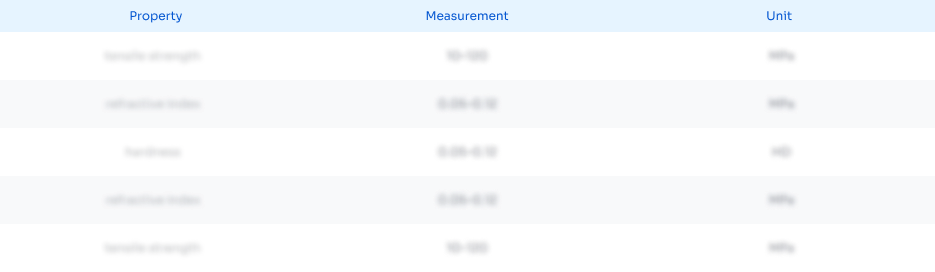
Abstract
Description
Claims
Application Information

- Generate Ideas
- Intellectual Property
- Life Sciences
- Materials
- Tech Scout
- Unparalleled Data Quality
- Higher Quality Content
- 60% Fewer Hallucinations
Browse by: Latest US Patents, China's latest patents, Technical Efficacy Thesaurus, Application Domain, Technology Topic, Popular Technical Reports.
© 2025 PatSnap. All rights reserved.Legal|Privacy policy|Modern Slavery Act Transparency Statement|Sitemap|About US| Contact US: help@patsnap.com