Molded product and production method thereof
A molding product and molding technology, applied in the field of toilet cover and its preparation, can solve the problems of high manufacturing cost, high energy consumption of mold heating, long resin curing reaction time, etc., and achieve low cost, reduced usage, and fast curing and molding process. Effect
- Summary
- Abstract
- Description
- Claims
- Application Information
AI Technical Summary
Problems solved by technology
Method used
Image
Examples
Embodiment 1
[0044] The molded article provided by this embodiment is a toilet seat, and its structure is as follows: figure 1 As shown, it includes a core 141 and a shell 142 that completely surrounds the core. Wherein, the core part 141 is molded from the first mixture comprising the following components: 8 parts by weight of Novalac phenolic resin powder, 92 parts by weight of rice straw powder with a particle size of 10 mesh; the shell part 142 is formed by the second mixture comprising the following components Formed by molding: 8 parts by weight of Novalac phenolic resin powder, 92 parts by weight of rice straw powder with a particle size of 60 mesh. Wherein, the water content of the rice straw powder is 2-9%.
[0045] The toilet cover is formed by a closed molding method, and its specific preparation method includes the following steps:
[0046] (1) Prepare a first mixture for the core 141 and a second mixture for the shell 142;
[0047] (2) laying the second mixture layer, the ...
Embodiment 2
[0053] The difference between this embodiment and Embodiment 1 is that the core part 141 is molded from the first mixture comprising the following components: 30 parts by weight of Novalac phenolic resin powder, 70 parts by weight of rice straw powder with a particle size of 40 mesh; shell part 142 Molded from the second mixture comprising: 30 parts by weight of Novalac phenolic resin powder, 70 parts by weight of rice straw powder with a particle size of 300 mesh and 1 part by weight of zinc stearate.
Embodiment 3
[0055] The difference between this embodiment and Embodiment 1 is that the core part 141 is molded from the first mixture comprising the following components: 8 parts by weight of Novalac phenolic resin powder, 92 parts by weight of rice straw powder with a particle size of 5 mesh; shell part 142 Molded from the second mixture comprising: 20 parts by weight of Novalac phenolic resin powder, 80 parts by weight of rice straw powder with a particle size of 80 mesh and 0.5 part by weight of zinc stearate.
PUM
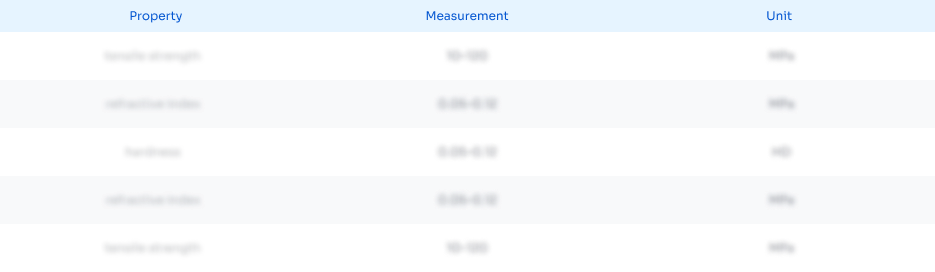
Abstract
Description
Claims
Application Information

- R&D
- Intellectual Property
- Life Sciences
- Materials
- Tech Scout
- Unparalleled Data Quality
- Higher Quality Content
- 60% Fewer Hallucinations
Browse by: Latest US Patents, China's latest patents, Technical Efficacy Thesaurus, Application Domain, Technology Topic, Popular Technical Reports.
© 2025 PatSnap. All rights reserved.Legal|Privacy policy|Modern Slavery Act Transparency Statement|Sitemap|About US| Contact US: help@patsnap.com