Heating treatment technology for aluminum alloy castings
A technology of aluminum alloy castings and preheating, which is applied in the field of metal casting, can solve the problems of not meeting practical needs, insufficient mechanical properties of aluminum alloy castings, and potential safety hazards in impact resistance, and achieves easy promotion and use, and improved mechanical strength , Improve the effect of mechanical properties and impact toughness
- Summary
- Abstract
- Description
- Claims
- Application Information
AI Technical Summary
Problems solved by technology
Method used
Examples
Embodiment 1
[0023] A heat treatment process for aluminum alloy castings is carried out according to the following steps:
[0024] (1) Vacuum homogenization preheating treatment: place the cast aluminum alloy casting in a vacuum high-temperature furnace for homogenization preheating treatment for 2.5 hours, the preheating temperature is controlled at 240°C, and the preheating heating rate is set at 10°C / min;
[0025] The above aluminum alloy castings include the following components by weight percentage: C 0.48%, Fe 3.20%, Si 1.45%, Mn3.35%, Cu 2.10%, Mg 1.70%, Zn 2.70%, Ni 0.24%, Ti 0.28%, Sb 0.15%, the balance is Al, and the content of non-removable trace elements is ≤0.01%;
[0026] (2) Primary normalizing: transfer the preheated aluminum alloy castings to the normalizing furnace for primary normalizing treatment, the heating rate of the above normalizing furnace is 15°C / min, and the temperature of the primary normalizing treatment is controlled at 640°C , the holding time is set to ...
Embodiment 2
[0032] A heat treatment process for aluminum alloy castings is carried out according to the following steps:
[0033] (1) Vacuum homogenization preheating treatment: place the cast aluminum alloy casting in a vacuum high-temperature furnace for homogenization preheating treatment for 3 hours, the preheating temperature is controlled at 260°C, and the preheating heating rate is set at 15°C / min ;
[0034] The above aluminum alloy castings include the following components by weight percentage: C 0.60%, Fe 3.60%, Si 1.80%, Mn3.95%, Cu 2.50%, Mg 2.00%, Zn 3.15%, Ni 0.36%, Ti 0.32%, Sb 0.15%, the balance is Al, and the content of non-removable trace elements is ≤0.01%;
[0035] (2) Primary normalizing: transfer the preheated aluminum alloy castings to the normalizing furnace for primary normalizing treatment, the heating rate of the above normalizing furnace is 20°C / min, and the temperature of the primary normalizing treatment is controlled at 650°C , the holding time is set to 1....
Embodiment 3
[0041] A heat treatment process for aluminum alloy castings is carried out according to the following steps:
[0042] (1) Vacuum homogenization preheating treatment: place the cast aluminum alloy castings in a vacuum high-temperature furnace for homogenization preheating treatment for 3.5 hours, the preheating temperature is controlled at 280°C, and the preheating heating rate is set at 15°C / min;
[0043] The above aluminum alloy castings include the following components by weight percentage: C 0.80%, Fe 4.00%, Si 2.00%, Mn4.15%, Cu 2.60%, Mg 2.10%, Zn 3.40%, Ni 0.42%, Ti 0.35%, Sb 0.20%, the balance is Al, and the non-removable trace element content is ≤0.01%;
[0044] (2) Primary normalizing: transfer the preheated aluminum alloy castings to the normalizing furnace for primary normalizing treatment, the heating rate of the above normalizing furnace is 20°C / min, and the temperature of the primary normalizing treatment is controlled at 660°C , the holding time is set to 2h; ...
PUM
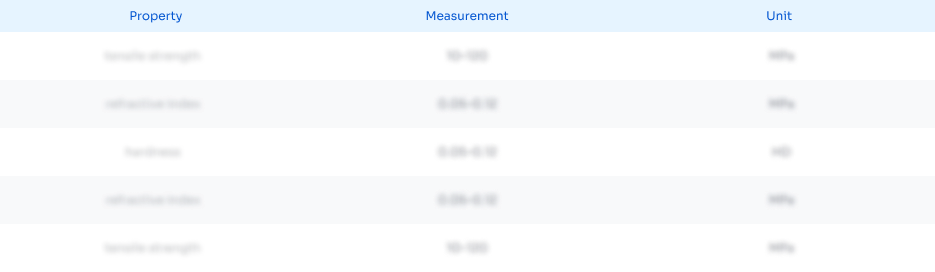
Abstract
Description
Claims
Application Information

- R&D Engineer
- R&D Manager
- IP Professional
- Industry Leading Data Capabilities
- Powerful AI technology
- Patent DNA Extraction
Browse by: Latest US Patents, China's latest patents, Technical Efficacy Thesaurus, Application Domain, Technology Topic, Popular Technical Reports.
© 2024 PatSnap. All rights reserved.Legal|Privacy policy|Modern Slavery Act Transparency Statement|Sitemap|About US| Contact US: help@patsnap.com