Method for separating and extracting silicon from silicon residue
A technology of silicon slag and mechanical separation, applied in chemical instruments and methods, silicon compounds, inorganic chemistry, etc., can solve problems such as difficulty in achieving ideal effects, and achieve the effects of strong practicability, obvious effects, and simple and easy operation.
- Summary
- Abstract
- Description
- Claims
- Application Information
AI Technical Summary
Problems solved by technology
Method used
Examples
Embodiment 1
[0019] Embodiment 1: the method for separating and extracting silicon from silicon slag, concrete operations are as follows:
[0020] (1) Using industrial silicon slag with Fe, Al, and Ca contents of 0.187%, 0.121%, and 0.083% respectively as raw materials, weigh 80g of silicon slag and put it into a graphite crucible, place the crucible in an intermediate frequency induction furnace, and simultaneously place the furnace Evacuate the inside to 10Pa, and then fill the vacuum chamber with argon until the pressure is 1 atmosphere;
[0021] (2) Adjust the current frequency of the intermediate frequency induction furnace to 2.5kHz and the power to 4.6kW, start the intermediate frequency induction furnace for heating, and measure the temperature with an infrared thermometer;
[0022] (3) After the temperature in the furnace reaches 1450°C, keep the molten silicon slag warm for 30 minutes, and then reduce the power to lower the temperature in the furnace to 20°C at a rate of 35°C / min...
Embodiment 2
[0024] Embodiment 2: the method for separating and extracting silicon from silicon slag, concrete operations are as follows:
[0025] (1) Using industrial silicon slag with Fe, Al, and Ca contents of 0.187%, 0.121%, and 0.083% respectively as raw materials, weigh 100g of silicon slag and put it into a graphite crucible, place the crucible in an intermediate frequency induction furnace, and simultaneously place the furnace Evacuate the inside to 5Pa, and then fill the vacuum chamber with argon until the pressure is 1 atmosphere;
[0026] (2) Adjust the current frequency of the intermediate frequency induction furnace to 2.8kHz, power 5kW, start the intermediate frequency induction furnace for heating, and measure the temperature with an infrared thermometer;
[0027] (3) After the temperature in the furnace reaches 1500°C, keep the molten silicon slag warm for 2 hours, and then reduce the power to lower the temperature in the furnace to 25°C at a rate of 20°C / min;
[0028] (4)...
Embodiment 3
[0029] Embodiment 3: the method for separating and extracting silicon from silicon slag, concrete operations are as follows:
[0030] (1) Using industrial silicon slag with Fe, Al, and Ca contents of 0.187%, 0.121%, and 0.083% respectively as raw materials, weigh 80g of silicon slag and put it into a graphite crucible, place the crucible in an intermediate frequency induction furnace, and simultaneously place the furnace Evacuate the inside to 5Pa, and then fill the vacuum chamber with argon until the pressure is 1 atmosphere;
[0031] (2) Adjust the current frequency of the intermediate frequency induction furnace to 3.0kHz, power 6kW, start the intermediate frequency induction furnace for heating, and measure the temperature with an infrared thermometer;
[0032] (3) After the temperature in the furnace reaches 1700°C, keep the molten silicon slag warm for 1 hour, and then reduce the power to lower the temperature in the furnace to 23°C at a rate of 50°C / min;
[0033] (4) U...
PUM
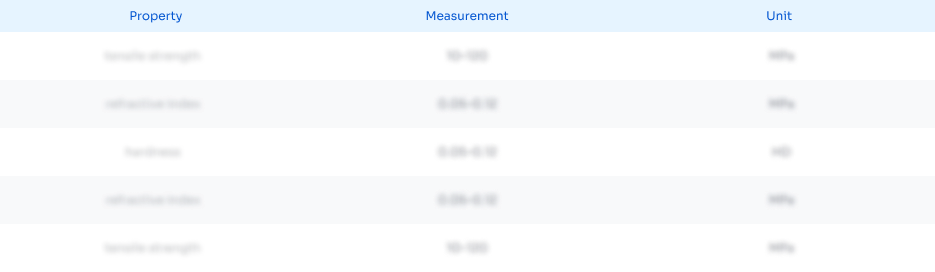
Abstract
Description
Claims
Application Information

- R&D
- Intellectual Property
- Life Sciences
- Materials
- Tech Scout
- Unparalleled Data Quality
- Higher Quality Content
- 60% Fewer Hallucinations
Browse by: Latest US Patents, China's latest patents, Technical Efficacy Thesaurus, Application Domain, Technology Topic, Popular Technical Reports.
© 2025 PatSnap. All rights reserved.Legal|Privacy policy|Modern Slavery Act Transparency Statement|Sitemap|About US| Contact US: help@patsnap.com