A kind of preparation method of ag-yag electric contact material
A technology for electrical contact materials and sheets, applied in chemical instruments and methods, contacts, circuits, etc., can solve problems such as harm to the human body, toxic Cd metal vapor, environmental pollution, etc., and achieve low cost, excellent mechanical properties, and preparation technology. simple effect
- Summary
- Abstract
- Description
- Claims
- Application Information
AI Technical Summary
Problems solved by technology
Method used
Image
Examples
Embodiment 1
[0025] Y(NO 3 ) 3 ·6H 2 O and Al (NO 3 ) 3 ·9H 2 O was added to 50ml deionized water to dissolve, so that the total concentration of metal ions in the solution was 0.5mol / L, where Y(NO 3 ) 3 ·6H 2 O and Al(NO 3 ) 3 ·9H 2 The molar ratio of O is 3:5; then, hexamethylenetetramine is added with sufficient stirring, the amount of which is 2.6g; the reaction is carried out at 85°C in a water bath for 100 minutes to obtain YAG sol; the YAG sol is dried, A dry gel is formed; moved into a muffle furnace and sintered in an air atmosphere: the temperature is raised to 950°C at a rate of 15°C / min, and the temperature is kept for 4 hours to obtain YAG powder. After mixing YAG powder and Ag powder with a mass ratio of 12:88 in a ball milling method, they are cold pressed to form a sheet; then the sheet is sintered to obtain an Ag-YAG electrical contact material. The sintering is first heating up The temperature is kept at 500°C for 3 hours; then the temperature is raised to 900°C for 3 hours...
Embodiment 2
[0027] Y(NO 3 ) 3 ·6H 2 O and Al (NO 3 ) 3 ·9H 2 O was added to 50ml deionized water to dissolve, so that the total concentration of metal ions in the solution was 0.5mol / L, where Y(NO 3 ) 3 ·6H 2 O and Al(NO 3 ) 3 ·9H 2 The molar ratio of O is 3:5; then, hexamethylenetetramine is added with sufficient stirring, the amount of which is 4.2g; the reaction is carried out in a water bath at 90°C for 80 minutes to obtain YAG sol; the YAG sol is dried, A dry gel is formed; moved into a muffle furnace and sintered in an air atmosphere: the temperature is raised to 950°C at a rate of 15°C / min, and the temperature is kept for 4 hours to obtain YAG powder. After mixing YAG powder and Ag powder with a mass ratio of 12:88 in a ball milling method, they are cold pressed to form a sheet; then the sheet is sintered to obtain an Ag-YAG electrical contact material. The sintering is first heating up The temperature is kept at 500°C for 3 hours; then the temperature is raised to 900°C for 5 hours;...
Embodiment 3
[0029] Y(NO 3 ) 3 ·6H 2 O and Al (NO 3 ) 3 ·9H 2 O was added to 50ml deionized water to dissolve, so that the total concentration of metal ions in the solution was 0.5mol / L, where Y(NO 3 ) 3 ·6H 2 O and Al(NO 3 ) 3 ·9H 2 The molar ratio of O is 3:5; then, hexamethylenetetramine is added with sufficient stirring, the amount of which is 6.3g; the reaction is carried out at 100°C in a water bath for 70 minutes to obtain YAG sol; the YAG sol is dried, A dry gel is formed; moved into a muffle furnace and sintered in an air atmosphere: the temperature is raised to 950°C at a rate of 15°C / min, and the temperature is kept for 4 hours to obtain YAG powder. After mixing YAG powder and Ag powder with a mass ratio of 12:88 in a ball milling method, they are cold pressed to form a sheet; then the sheet is sintered to obtain an Ag-YAG electrical contact material. The sintering is first heating up The temperature is kept at 500°C for 3 hours; then the temperature is raised to 900°C for 3 hours...
PUM
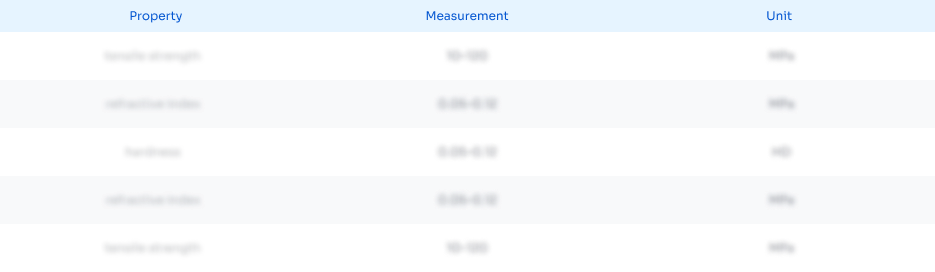
Abstract
Description
Claims
Application Information

- Generate Ideas
- Intellectual Property
- Life Sciences
- Materials
- Tech Scout
- Unparalleled Data Quality
- Higher Quality Content
- 60% Fewer Hallucinations
Browse by: Latest US Patents, China's latest patents, Technical Efficacy Thesaurus, Application Domain, Technology Topic, Popular Technical Reports.
© 2025 PatSnap. All rights reserved.Legal|Privacy policy|Modern Slavery Act Transparency Statement|Sitemap|About US| Contact US: help@patsnap.com