Preparation method of 3D printing material
A 3D printing and material technology, applied in the direction of additive processing, tungsten/molybdenum carbide, carbide, etc., can solve the problems of wide particle size distribution, low hardness and strength, low bulk density, etc., to achieve narrow particle size distribution, High hardness and strength, high bulk density
- Summary
- Abstract
- Description
- Claims
- Application Information
AI Technical Summary
Problems solved by technology
Method used
Examples
preparation example Construction
[0029] A kind of preparation method of 3D printing material, it is the following steps:
[0030] (1) Cobalt chloride and nickel chloride are mixed evenly with pure water according to a molar ratio of 8-10:1, and an organic extractant is added to extract cobalt nickel into the organic extractant, washed with pure water, and the Wash the chloride ion until the content is less than 10ppm, the concentration of cobalt and nickel is 0.2-0.3mol / L, add metatungstic acid to 70-80℃ hot water and dissolve it until the concentration is 0.2-0.3mol / L;
[0031] (2) The cobalt-nickel-containing extractant and metatungstic acid solution are sprayed into the spray chamber. The droplet diameter of the cobalt-nickel extractant is 0.1-0.2mm, and the speed of entering the spray chamber is 5-10m / s. The droplet diameter of the metatungstic acid solution is 0.05-0.1mm, the speed of entering the spray chamber is 5-10m / s, and the temperature in the spray chamber is maintained at 50-60°C. The ratio is 1...
Embodiment 1
[0041] A kind of preparation method of 3D printing material, it is the following steps:
[0042] (1) Mix cobalt chloride and nickel chloride with pure water according to the molar ratio of 8.5:1, add an organic extractant to extract cobalt nickel into the organic extractant, wash with pure water, and remove the chloride ions in the organic extractant Wash until the content is less than 10ppm, the concentration of cobalt and nickel is 0.25mol / L, add metatungstic acid to 73°C hot water and dissolve until the concentration is 0.3mol / L;
[0043] (2) The cobalt-nickel-containing extractant and metatungstic acid solution are sprayed into the spray chamber. The droplet diameter of the cobalt-nickel extractant is 0.15mm, and the speed of entering the spray chamber is 8m / s. The metatungstic acid solution The particle diameter of the spray droplet is 0.07mm, and the speed of entering the spray chamber is 9m / s. There is an updraft with a speed of 3m / s, and the spray chamber rotates at a...
Embodiment 2
[0055] A kind of preparation method of 3D printing material, it is the following steps:
[0056] (1) Mix cobalt chloride and nickel chloride with pure water according to the molar ratio of 8.3:1, add an organic extractant to extract cobalt nickel into the organic extractant, wash with pure water, and remove the chloride ions in the organic extractant Wash until the content is less than 10ppm, the concentration of cobalt and nickel is 0.25mol / L, add metatungstic acid to 75℃ hot water and dissolve until the concentration is 0.25mol / L;
[0057] (2) The cobalt-nickel-containing extractant and metatungstic acid solution are sprayed into the spray chamber. The droplet diameter of the cobalt-nickel extractant is 0.15mm, and the speed of entering the spray chamber is 8m / s. The metatungstic acid solution The particle diameter of the spray droplet is 0.065mm, and the speed of entering the spray chamber is 7m / s. There is an updraft with a speed of 3m / s, and the spray chamber rotates at ...
PUM
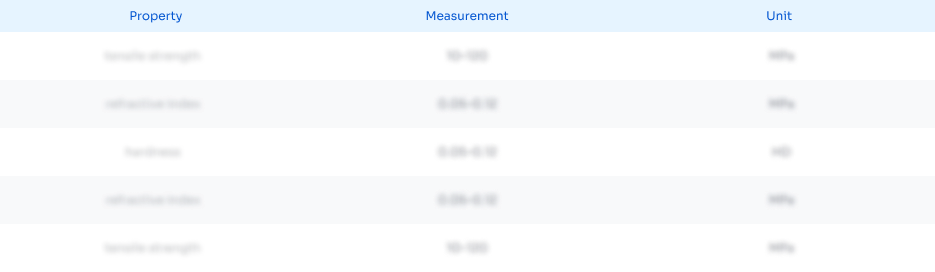
Abstract
Description
Claims
Application Information

- R&D
- Intellectual Property
- Life Sciences
- Materials
- Tech Scout
- Unparalleled Data Quality
- Higher Quality Content
- 60% Fewer Hallucinations
Browse by: Latest US Patents, China's latest patents, Technical Efficacy Thesaurus, Application Domain, Technology Topic, Popular Technical Reports.
© 2025 PatSnap. All rights reserved.Legal|Privacy policy|Modern Slavery Act Transparency Statement|Sitemap|About US| Contact US: help@patsnap.com