A kind of porous silicon/graphene composite material and its preparation method and application
A technology of composite materials and porous silicon, applied in structural parts, electrical components, battery electrodes, etc., can solve problems such as poor electronic conductivity and severe volume effect
- Summary
- Abstract
- Description
- Claims
- Application Information
AI Technical Summary
Problems solved by technology
Method used
Image
Examples
Embodiment 1
[0061] 1. 1L mass fraction of 5.4% Ca(OH) 2 Add the suspension into the reaction vessel, stir the suspension at a rotation speed of 300r / min, add 1.5g of SBA-15 particles after 10min, start the vacuum pump to make the vacuum of the reaction vessel reach -0.06MPa, and turn off the vacuum pump. After continuing to stir for 30 min, CO was introduced into the 2 gas, when H is 7, stop feeding the reaction gas, filter the suspension, and dry it under vacuum at 70°C for 6 hours to obtain a porous silica / calcium carbonate composite material.
[0062] 2. Mix 4 g of porous silica / calcium carbonate composite material with 1 g of polyacrylonitrile in 2 L of dimethyl sulfoxide (DMSO) solvent, and heat to remove the solvent to obtain an organic-coated porous silica / calcium carbonate composite material.
[0063] 3. Mix 1g of organic-coated porous silica / calcium carbonate composite material with 1g of magnesium powder, put it in the muffle furnace, first pass pure argon for 30min, and the fl...
Embodiment 2
[0066] 1. 1L mass fraction of 5.4% Ca(OH) 2 Add the suspension into the reaction vessel, stir the suspension at a rotation speed of 400r / min, add 2.5g of MCM-48 particles after 20min, start the vacuum pump to make the vacuum of the reaction vessel reach -0.06MPa, and turn off the vacuum pump. After continuing to stir for 40 min, CO 2 gas, when the pH is 6, stop feeding the reaction gas, filter the suspension, and dry it in a vacuum environment at 80°C for 7 hours to obtain a porous silica / calcium carbonate composite material.
[0067] 2. Mix 5g of porous silica / calcium carbonate composite with 1g of polyacrylonitrile in 2L nitrogen dimethylformamide (DMF) solvent, heat to remove solvent to obtain organic carbon-coated porous silica / calcium carbonate composite .
[0068] 3. Mix 1g of organic-coated porous silica / calcium carbonate composite material with 1g of magnesium powder, put it in the muffle furnace, first pass pure argon gas for 20min, the flow rate is 300ml / min, and r...
Embodiment 3
[0071] 1. 1L mass fraction of 5.4% Ca(OH) 2 Add the suspension into the reaction vessel, stir the suspension at a rotation speed of 400r / min, add 3.0g of purified diatomite particles after 20min, start the vacuum pump to make the vacuum of the reaction vessel reach -0.06MPa, and turn off the vacuum pump. After continuing to stir for 40 min, CO 2 gas, when the pH is 8, stop feeding the reaction gas, filter the suspension, and dry it in a vacuum environment at 80° C. for 5 hours to obtain a porous silica / calcium carbonate composite material.
[0072] 2. Mix 3 g of porous silica / calcium carbonate composite material with 1 g of polyacrylonitrile in 2 L of dimethylacetamide (DMAC) solvent, and remove the solvent by heating to obtain organic carbon-coated porous silica / calcium carbonate composite material.
[0073] 3. Mix 1g of organic-coated porous silica / calcium carbonate composite material with 1.1g of magnesium powder, place it in a muffle furnace, and feed pure argon for 30 mi...
PUM
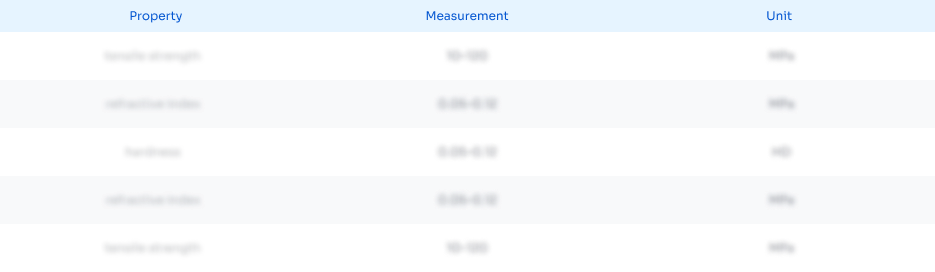
Abstract
Description
Claims
Application Information

- R&D
- Intellectual Property
- Life Sciences
- Materials
- Tech Scout
- Unparalleled Data Quality
- Higher Quality Content
- 60% Fewer Hallucinations
Browse by: Latest US Patents, China's latest patents, Technical Efficacy Thesaurus, Application Domain, Technology Topic, Popular Technical Reports.
© 2025 PatSnap. All rights reserved.Legal|Privacy policy|Modern Slavery Act Transparency Statement|Sitemap|About US| Contact US: help@patsnap.com