Mould coal binder, and preparation method thereof
A technology of binder and briquette, applied in the field of briquette binder and its production, can solve problems such as secondary pollution, and achieve the effects of reducing volatilization, promoting stability and ensuring stability
- Summary
- Abstract
- Description
- Claims
- Application Information
AI Technical Summary
Problems solved by technology
Method used
Image
Examples
Embodiment 1
[0027] A briquette binder comprising the following components: 0.5kg of esterified waste oil, 0.1kg of sodium carbonate, 3kg of smithsonite, 85kg of consolidation agent, 0.3kg of basic zinc carbonate, 1kg of potassium chloride, polyacrylamide 1kg. Wherein, the consolidating agent includes 84.6 kg of water-based cellulose, 0.2 kg of guar gum, and 0.2 kg of xanthan gum.
[0028] The preparation method of above-mentioned briquette binder, comprises the following steps:
[0029] S1: Mix 0.5kg of esterified waste oil, 0.1kg of sodium carbonate, 3kg of smithsonite, 85kg of consolidation agent, 0.3kg of basic zinc carbonate, 1kg of potassium chloride, and 1kg of polyacrylamide, and then place them in a high-pressure reactor Carry out reaction and keep warm for 30 minutes; Wherein the pressure that carries out reaction in autoclave is 20Mpa, and reaction temperature is 60 degrees Celsius;
[0030] S2: Take out the paste mixture obtained in step S1 after natural cooling, which is the...
Embodiment 2
[0032] A briquette binder comprising the following components: 0.75kg of esterified waste oil, 0.5kg of sodium carbonate, 5.5kg of smithsonite, 91kg of consolidation agent, 0.5kg of basic zinc carbonate, 2kg of potassium chloride, polypropylene Amide 3kg. Wherein, the consolidating agent comprises 90.2kg of water-based cellulose, 0.5kg of guar gum, and 0.3kg of xanthan gum.
[0033] The preparation method of above-mentioned briquette binder, comprises the following steps:
[0034] S1: Mix 0.75kg of esterified waste oil, 0.5kg of sodium carbonate, 5.5kg of smithsonite, 91kg of consolidation agent, 0.5kg of basic zinc carbonate, 2kg of potassium chloride, and 3kg of polyacrylamide and place it in a high-pressure reactor React in and be incubated 30 minutes; Wherein the pressure that carries out reaction in autoclave is 30Mpa, and reaction temperature is 70 degrees centigrade;
[0035] S2: Take out the paste mixture obtained in step S1 after natural cooling, which is the brique...
Embodiment 3
[0037] A briquette binder comprising the following components: 0.6kg of esterified waste oil, 0.16kg of sodium carbonate, 4kg of smithsonite, 88kg of consolidation agent, 0.4kg of basic zinc carbonate, 1.5kg of potassium chloride, polypropylene Amide 2kg. Wherein, the consolidating agent includes 88.35kg of water-based cellulose, 0.4kg of guar gum, and 0.25kg of xanthan gum.
[0038] The preparation method of above-mentioned briquette binder, comprises the following steps:
[0039] S1: Mix 0.6kg of esterified waste oil, 0.16kg of sodium carbonate, 4kg of smithsonite, 88kg of consolidation agent, 0.4kg of basic zinc carbonate, 1.5kg of potassium chloride, and 2kg of polyacrylamide, and then place it in a high-pressure reactor React in and be incubated 30 minutes; Wherein the pressure that carries out reaction in autoclave is 25Mpa, and reaction temperature is 65 degrees centigrade;
[0040] S2: Take out the paste mixture obtained in step S1 after natural cooling, which is the...
PUM
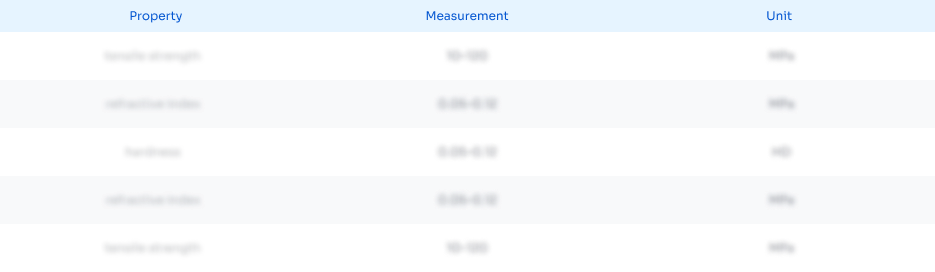
Abstract
Description
Claims
Application Information

- R&D
- Intellectual Property
- Life Sciences
- Materials
- Tech Scout
- Unparalleled Data Quality
- Higher Quality Content
- 60% Fewer Hallucinations
Browse by: Latest US Patents, China's latest patents, Technical Efficacy Thesaurus, Application Domain, Technology Topic, Popular Technical Reports.
© 2025 PatSnap. All rights reserved.Legal|Privacy policy|Modern Slavery Act Transparency Statement|Sitemap|About US| Contact US: help@patsnap.com