Preparation method for acetic acid octanoic acid cellulose ester
A technology of cellulose ester and cellulose, which is applied in the field of preparation of cellulose acetate octanoate, can solve the problems of incomplete solid-phase reaction and long reaction time, and achieve the advantages of improved freeze-thaw stability, obvious viscosity drop, and short time-consuming Effect
- Summary
- Abstract
- Description
- Claims
- Application Information
AI Technical Summary
Problems solved by technology
Method used
Examples
Embodiment 1
[0032] A preparation method of cellulose acetate caprylate, it comprises the following steps:
[0033] (1) Weigh 20g of acetic anhydride, 20g of n-octanoic acid and 0.5g of catalyst concentrated sulfuric acid, and mix and pre-react the three at 90°C for 1 hour to obtain a co-reactant;
[0034] (2) Put the cellulose into a mechanical activation reactor for pretreatment, control the ball milling speed to 350r / min, the ball milling temperature to 50°C, and the ball milling time to 60min to obtain the treated cellulose.
[0035] (3) Weigh 81g of cellulose treated in step (2), mix it with the co-reactant obtained in step (1), put it into a microwave reactor for reaction, control the microwave power to 300W, and the microwave time to 5min, to obtain Crude cellulose acetate octanoate;
[0036] (4) The crude cellulose acetate octanoate obtained in step (3) is washed, filtered under reduced pressure, and dried in an oven at 40-60° C. to obtain the cellulose acetate octanoate product. ...
Embodiment 2
[0039] A preparation method of cellulose acetate caprylate, it comprises the following steps:
[0040] (1) Weigh 20g of acetic anhydride, 30g of n-octanoic acid and 1g of catalyst concentrated hydrochloric acid, and mix and pre-react the three at 80°C for 1 hour to obtain a co-reactant;
[0041] (2) Put the cellulose into a mechanical activation reactor for pretreatment, control the ball milling speed to 300r / min, the ball milling temperature to 60°C, and the ball milling time to 90min to obtain the treated cellulose.
[0042](3) Weigh 102g of cellulose treated in step (2), mix it with the co-reactant obtained in step (1), put it into a microwave reactor for reaction, control the microwave power to 350W, and the microwave time to 10min, to obtain Crude cellulose acetate octanoate;
[0043] (4) The crude cellulose acetate octanoate obtained in step (3) is washed, filtered under reduced pressure, and dried in an oven at 40-60° C. to obtain the cellulose acetate octanoate produc...
Embodiment 3
[0046] A preparation method of cellulose acetate caprylate, it comprises the following steps:
[0047] (1) Weigh 20g of acetic anhydride, 40g of n-octanoic acid and 1g of catalyst nitric acid, and mix and pre-react the three at 70°C for 80min to obtain a co-reactant;
[0048] (2) Put the cellulose into a mechanical activation reactor for pretreatment, control the ball milling at 400r / min, the ball milling temperature at 70°C, and the ball milling time for 50min to obtain the treated cellulose.
[0049] (3) Weigh 183g of cellulose treated in step (2), mix it with the co-reactant obtained in step (1), put it into a microwave reactor for reaction, the microwave power is 400W, and the microwave time is 5min to obtain acetic acid Crude cellulose caprylate;
[0050] (4) The crude cellulose acetate octanoate obtained in step (3) is washed, filtered under reduced pressure, and dried in an oven at 40-60° C. to obtain the cellulose acetate octanoate product.
[0051] The degree of sub...
PUM
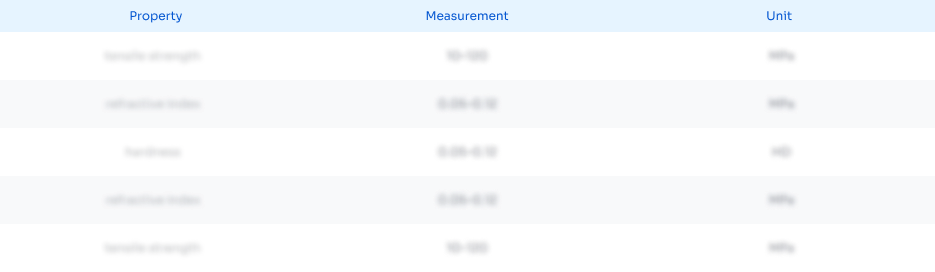
Abstract
Description
Claims
Application Information

- R&D
- Intellectual Property
- Life Sciences
- Materials
- Tech Scout
- Unparalleled Data Quality
- Higher Quality Content
- 60% Fewer Hallucinations
Browse by: Latest US Patents, China's latest patents, Technical Efficacy Thesaurus, Application Domain, Technology Topic, Popular Technical Reports.
© 2025 PatSnap. All rights reserved.Legal|Privacy policy|Modern Slavery Act Transparency Statement|Sitemap|About US| Contact US: help@patsnap.com