Method for manufacturing metallic vanadium
A manufacturing method and metal technology, applied in the field of metal vanadium, can solve the problems of large-scale equipment, difficult treatment of vanadium halides, and failure to achieve practical use, and achieve low-cost effects
- Summary
- Abstract
- Description
- Claims
- Application Information
AI Technical Summary
Problems solved by technology
Method used
Image
Examples
Embodiment 1
[0092] Next, examples will be described.
[0093] In this embodiment, as the molten salt (mixed molten salt) 8, 600 g of calcium chloride (manufactured by Wako Pure Chemical Industries, Ltd., reagent special grade) is obtained by adding 0.5 mol% calcium sulfide (manufactured by Wako Pure Chemical Industries, Ltd., special grade reagent) Put the substance in the crucible 3 (with an inner diameter of 90mm and a depth of 200mm). The crucible 3 was placed in a closed container 4 (inner diameter of 105 mm, depth of 480 mm), flanges were attached and sealed, and after vacuum dehydration treatment, the temperature was raised to 900° C. in an argon atmosphere.
[0094] In addition, the titanium rod 1a and the carbon rod 1b of the anode 1 and the titanium rod 2a of the cathode 2 and the container 2b installed so as to surround the titanium rod are prepared. 1.502 g of vanadium sulfide 12 (purity 99% manufactured by Yauchi Chemical Co., Ltd.) was inserted into the container 2b.
[0095] Afte...
Embodiment 2
[0098] In this embodiment, as molten salt 8, a substance obtained by adding 0.5 mol% calcium sulfide (made by Wako Pure Chemical Industries, Ltd., special grade reagent) to 600 g of calcium chloride (made by Wako Pure Chemical Industries, Ltd., special grade reagent) is placed in a crucible 3 (Inner diameter is 90mm, depth is 200mm). The crucible 3 was placed in a closed container 4 (inner diameter of 105 mm, depth of 480 mm) and flanges were attached to seal the crucible 3, and after vacuum dehydration treatment, the temperature was raised to 900°C in an argon atmosphere.
[0099] In addition, the titanium rod 1a and the carbon rod 1b of the anode 1 and the titanium rod 2a of the cathode 2 and the container 2b installed so as to surround the titanium rod are prepared. In the container 2b, 1.488 g of vanadium trioxide 12 (purity of 99% or more manufactured by Sun Miner) is inserted.
[0100] After the temperature has stabilized, the two electrodes 1 and 2 are inserted into the mol...
Embodiment 3
[0103] In this example, as raw materials (vanadium compound 12), 4 g of ammonium metavanadate (Wako Pure Chemical Special Grade Reagent) and vanadyl sulfate (Xinxing Chemical) were prepared respectively. Then, each prepared raw material was subjected to heat treatment (heating temperature: 600°C, heating time: 10 minutes) as a pretreatment to obtain a treated material. The obtained substances were analyzed, and the results were all vanadium pentoxide oxide (V 2 O 5 ).
[0104] Use each vanadium pentoxide oxide (V 2 O 5 ), respectively, to manufacture metallic vanadium. At this time, put the vanadium oxide (V 2 O 5 The amount of) is 1.500 g in either case. In addition, due to the removal of vanadium oxide (V 2 O 5 The manufacturing conditions other than the amount of) are the same as in Example 2, so the description is omitted here.
[0105] The analysis results of the sulfur content and the oxygen content (oxygen concentration) of the samples (manufactured samples) produced by th...
PUM
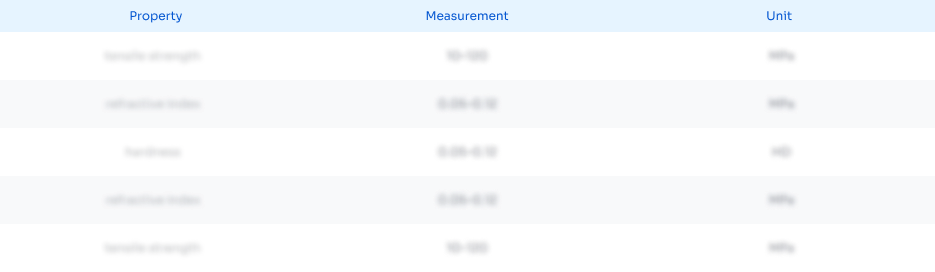
Abstract
Description
Claims
Application Information

- Generate Ideas
- Intellectual Property
- Life Sciences
- Materials
- Tech Scout
- Unparalleled Data Quality
- Higher Quality Content
- 60% Fewer Hallucinations
Browse by: Latest US Patents, China's latest patents, Technical Efficacy Thesaurus, Application Domain, Technology Topic, Popular Technical Reports.
© 2025 PatSnap. All rights reserved.Legal|Privacy policy|Modern Slavery Act Transparency Statement|Sitemap|About US| Contact US: help@patsnap.com