Preparation method of carbon nanotube-montmorillonite self-assembled nanopowder grafted glass fiber reinforced resin composite material
A technology of carbon nanotubes and glass fibers, which is applied in the field of fiber-reinforced polymer composite materials, can solve the problems of uneven dispersion of nanofillers, uneven distribution of CNTs at the injection port and the exit port, etc., so as to increase the layer spacing and avoid easy winding , Improve the effect of interface adhesion
- Summary
- Abstract
- Description
- Claims
- Application Information
AI Technical Summary
Problems solved by technology
Method used
Image
Examples
Embodiment 1
[0032] A preparation method of carbon nanotube-montmorillonite self-assembled nano-powder grafted glass fiber reinforced composite material, the specific steps are as follows:
[0033] (1) Aminated carbon nanotubes: Weigh 0.2g of carboxyl multi-walled carbon nanotubes and add 0.02L of N,N'-dimethylformamide solvent, and then add 0.005g of N,N'-diisopropyl Carbodiimide and 1-hydroxybenzotriazole were stirred for 5 min and ultrasonic for 30 min to obtain a 10g / L carbon nanotube dispersion, which was stirred magnetically at a speed of 200r / min; weighed 0.01g diethylene Triamine was added to the carbon nanotube dispersion liquid, reacted at room temperature for 24 hours, washed with deionized water and washed with alcohol twice, and then filtered to obtain diethylenetriamine modified carbon nanotubes;
[0034] (2) Preparation of carbon nanotube ammonium salt: the carbon nanotubes modified by diethylenetriamine in step (1) are stirred in 0.02L of deionized water for 5 minutes and ultras...
Embodiment 2
[0040] A carbon nanotube-montmorillonite self-assembled nanopowder and a preparation method thereof. The difference from Example 1 is that the carboxyl carbon nanotubes in step (1) are changed to 1g, and the N, N' -Diisopropylcarbodiimide and 1-hydroxybenzotriazole were changed to 0.02g, and the organic amine was changed to 0.2g triethylenetetramine; the pH of the solution in step (2) was adjusted to 4; In step (3), add 10g of montmorillonite to 100mL of deionized water, stir at 1000r / min for 3h, and ultrasonic for 1h; the stirring speed of carbon nanotube ammonium salt in the montmorillonite suspension is 800r / min, and Continue stirring for 5 hours; the silane coupling agent described in step (4) becomes 0.03g of 3-(2,3-glycidoxy)propyltriethoxysilane, and the pH of the silane coupling agent solution is adjusted with acetic acid To 4.0; the mass of nano powder is changed to 3g; in step (5), the composite material molding process is changed to a vacuum assisted resin transfer m...
Embodiment 3
[0043] A carbon nanotube-montmorillonite self-assembled nanopowder and a preparation method thereof. The difference from Example 1 is that the carboxyl carbon nanotubes in step (1) are changed to 1 g, and the aprotic organic solvent It becomes carbon tetrachloride, and the dehydrating condensing agent becomes ethyl-(3-dimethylaminopropyl) carbodiimide hydrochloride (EDC) and N-hydroxysuccinimide (NHS), The organic amine becomes 0.05g tetraethylenepentamine; the pH value of the solution in step (2) is adjusted to 3.5 with hydrochloric acid, and the rotation speed is adjusted to 600r / min; the quality of montmorillonite in step (3) is changed The cation exchange capacity of the montmorillonite becomes 100 mmol / 100g, and the stirring speed of the ammonium salt of carbon nanotubes in the montmorillonite suspension is 600 r / min. The silane coupling agent described in step (4) becomes N-(2-aminoethyl)-3-aminopropyltriethoxysilane; the glass fiber material has an areal density of 400g / ...
PUM
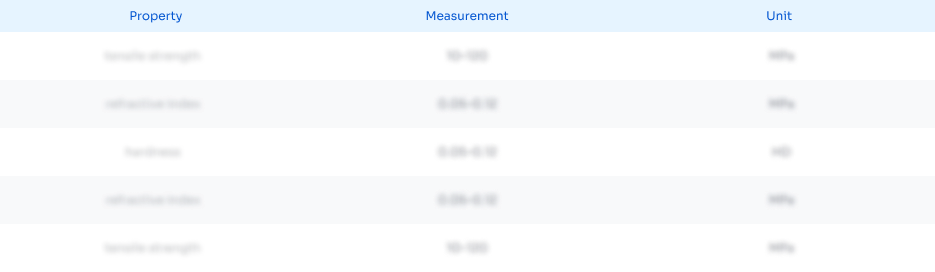
Abstract
Description
Claims
Application Information

- Generate Ideas
- Intellectual Property
- Life Sciences
- Materials
- Tech Scout
- Unparalleled Data Quality
- Higher Quality Content
- 60% Fewer Hallucinations
Browse by: Latest US Patents, China's latest patents, Technical Efficacy Thesaurus, Application Domain, Technology Topic, Popular Technical Reports.
© 2025 PatSnap. All rights reserved.Legal|Privacy policy|Modern Slavery Act Transparency Statement|Sitemap|About US| Contact US: help@patsnap.com