Method for preparing titanium based spherical powder with reduced particle size through gas atomization
A technology of spherical powder and gas atomization, which is applied in the field of powder metallurgy, can solve the problems of high technical requirements, and achieve the effects of increasing the yield of fine powder, improving physical properties and reducing viscosity
- Summary
- Abstract
- Description
- Claims
- Application Information
AI Technical Summary
Problems solved by technology
Method used
Image
Examples
Embodiment 1
[0026] The method of this embodiment is:
[0027] Step 1. Put Ti6Al4V alloy ingots and tin blocks into a water-cooled copper crucible, and then place them in the melting chamber of the vacuum induction melting gas atomization equipment, and evacuate the melting chamber until the vacuum degree in the furnace is not more than 5 Pa. Vacuum induction smelting at a temperature of 1700°C; the amount of the tin material is 2% of the total mass of the titanium alloy raw materials and the tin material;
[0028] Step 2. After the Ti6Al4V alloy raw materials and tin materials described in step one are melted by vacuum induction melting, fill the melting chamber with argon protection, and the pressure of the filled argon is 0.5bar; then the bottom of the water-cooled copper crucible The graphite draft tube is heated, and the Ti6Al4V alloy raw materials and tin material are completely melted to produce a low-viscosity molten liquid. The molten liquid falls freely into the atomization chamber th...
Embodiment 2
[0037] The method of this embodiment is:
[0038] Step 1. Put Ti6Al4V alloy ingots and tin blocks into a water-cooled copper crucible, and then place them in the melting chamber of the vacuum induction melting gas atomization equipment, and evacuate the melting chamber until the vacuum degree in the furnace is not more than 5 Pa. Vacuum induction smelting is performed at a temperature of 1800°C; the amount of the tin material is 1% of the total mass of the titanium alloy raw materials and the tin material;
[0039] Step 2. After the titanium alloy raw material and tin material described in step 1 are melted by vacuum induction melting, they are filled with argon gas for protection, and the pressure of the argon gas is 0.1bar; and then the graphite draft tube located at the bottom of the water-cooled copper crucible When the Ti6Al4V alloy raw materials and tin are completely melted, a low-viscosity molten liquid is produced. The molten liquid falls freely into the atomization chambe...
Embodiment 3
[0042] The method of this embodiment is:
[0043] Step 1. Put Ti6Al4V alloy ingots and tin blocks into a water-cooled copper crucible, and then place them in the melting chamber of the vacuum induction melting gas atomization equipment, and evacuate the melting chamber until the vacuum degree in the furnace is not more than 5 Pa. Vacuum induction melting is performed at a temperature of 1600°C; the amount of the tin material is 3% of the total mass of the titanium alloy raw materials and the tin material;
[0044] Step 2. After the Ti6Al4V alloy raw materials and tin materials described in step 1 are melted by vacuum induction melting, they are filled with argon gas for protection, and the pressure of the argon gas is 0.5bar; and then the graphite draft tube at the bottom of the water-cooled copper crucible When the Ti6Al4V alloy raw materials and tin are completely melted, a low-viscosity molten liquid is produced. The molten liquid falls freely into the atomization chamber throug...
PUM
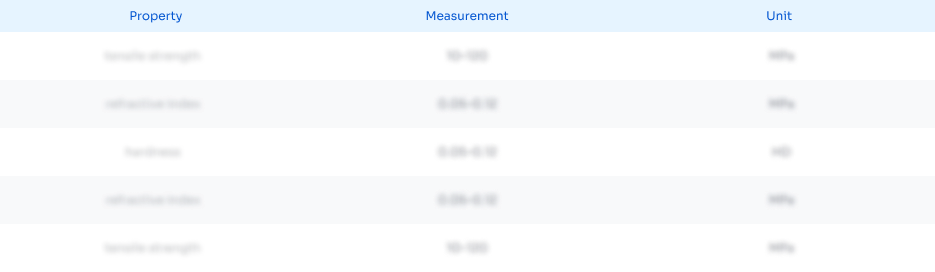
Abstract
Description
Claims
Application Information

- Generate Ideas
- Intellectual Property
- Life Sciences
- Materials
- Tech Scout
- Unparalleled Data Quality
- Higher Quality Content
- 60% Fewer Hallucinations
Browse by: Latest US Patents, China's latest patents, Technical Efficacy Thesaurus, Application Domain, Technology Topic, Popular Technical Reports.
© 2025 PatSnap. All rights reserved.Legal|Privacy policy|Modern Slavery Act Transparency Statement|Sitemap|About US| Contact US: help@patsnap.com