Casting mold coating and preparation method thereof
A casting coating and preparation method technology, which is applied in the direction of casting molds, casting mold components, casting molding equipment, etc., can solve problems such as monotonous layers, unreasonable coating composition matching, and the inability of traditional coating methods to exert the maximum effect of coatings. Effects of preventing sand sticking and improving surface quality
- Summary
- Abstract
- Description
- Claims
- Application Information
AI Technical Summary
Problems solved by technology
Method used
Examples
Embodiment 1
[0026] According to the technical scheme of the present invention, a mold coating suitable for sand casting of high chromium steel castings is prepared.
[0027] The mold coating is divided into a primer coated on the surface of the mold and an outer coating coated on the surface of the primer.
[0028] The primer is composed of the following components: 35 parts by weight of zircon powder, 16 parts by weight of titanium oxide, 19 parts by weight of silicon carbide, 20 parts by weight of kaolin, 6 parts by weight of water-soluble phenolic resin, 3 parts by weight of sodium tripolyphosphate, 10 parts by weight Parts by weight of calcium-based bentonite, 25 parts by weight of carrier water;
[0029] The outer coating is composed of the following components: 40 parts by weight of mullite powder, 15 parts by weight of bauxite clinker, 15 parts by weight of talc powder, 15 parts by weight of silicon carbide, 7 parts by weight of water-soluble phenolic resin, 4 parts by weight of th...
Embodiment 2
[0040] According to the technical scheme of the present invention, a mold coating suitable for sand casting of high chromium steel castings is prepared.
[0041] The mold coating is divided into a primer coated on the surface of the mold and an outer coating coated on the surface of the primer.
[0042] The primer is composed of the following components: 30 parts by weight of zircon powder, 21 parts by weight of titanium oxide, 15 parts by weight of silicon carbide, 23 parts by weight of kaolin, 8 parts by weight of water-soluble phenolic resin, 5 parts by weight of aluminum dihydrogen tripolyphosphate , 15 parts by weight of calcium-based bentonite, 35 parts by weight of carrier water;
[0043]The outer coating is composed of the following components: 35 parts by weight of mullite powder, 20 parts by weight of bauxite clinker, 10 parts by weight of talc powder, 10 parts by weight of silicon carbide, 9 parts by weight of polyvinyl alcohol, 6 parts by weight of terpolymer Alum...
Embodiment 3
[0054] The difference between this example and Example 1 is that 3 parts by weight of defoamer are added in step (2) during the preparation of the primer and the outer coating, and the rest are the same as in Example 1. , After unpacking, high-chromium cast steel parts with a flat and smooth appearance, no defects such as sticky sand, sand inclusions, protrusions, etc. can be obtained, and the paint can be easily peeled off.
PUM
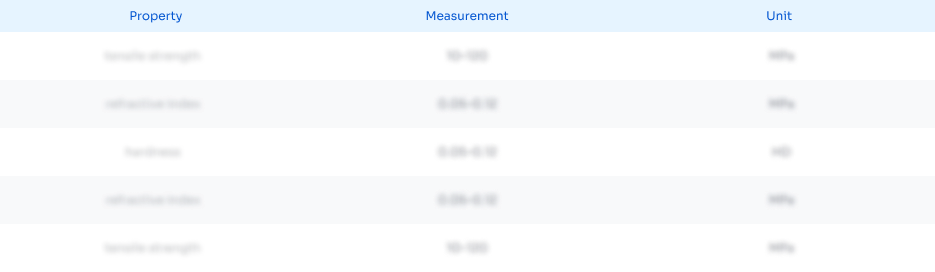
Abstract
Description
Claims
Application Information

- R&D Engineer
- R&D Manager
- IP Professional
- Industry Leading Data Capabilities
- Powerful AI technology
- Patent DNA Extraction
Browse by: Latest US Patents, China's latest patents, Technical Efficacy Thesaurus, Application Domain, Technology Topic, Popular Technical Reports.
© 2024 PatSnap. All rights reserved.Legal|Privacy policy|Modern Slavery Act Transparency Statement|Sitemap|About US| Contact US: help@patsnap.com