Production technology for sliding stop ground mat
A production process and floor mat technology, which is applied in the field of foam products, can solve problems such as blurred lines, skeletal muscle damage, and slippery surface of the floor mat, and achieve the effects of enhanced anti-slip effect, clear lines, and easy laying
- Summary
- Abstract
- Description
- Claims
- Application Information
AI Technical Summary
Problems solved by technology
Method used
Examples
Embodiment 1
[0016] The production process of the present embodiment anti-skid floor mat, this production process comprises the following steps:
[0017] (1) Substrate preparation: Prepare each foaming material, then mix the foaming materials and set aside;
[0018] (2) Foam molding: Pour the mixed foam material into the foam mold, spread it flat, and then foam it at 175°C for 12 minutes to shape the material, then cool it to room temperature, and take out the foamed sheet from the mold material;
[0019] (3) Removing the surface layer: the foamed sheet is cut off the surface layer with a cutting machine according to the actual thickness to be removed;
[0020] (4) Pressed texture: Put the sheet with the surface removed into the integrated mold for hot pressing and cooling forming, close the mold, then heat the mold to 100°C, keep it for 10 minutes according to the thickness of the actual product, and then cool it for 1 minute to Normal temperature, finally forming lines on the surface o...
Embodiment 2
[0023] The production process of the present embodiment anti-skid floor mat, this production process comprises the following steps:
[0024] (1) Substrate preparation: Prepare each foaming material, then mix the foaming materials and set aside;
[0025] (2) Foam molding: Pour the mixed foam material into the foam mold, spread it flat, and then foam it at 185°C for 8 minutes to shape the material, then cool it to room temperature, and take out the foamed sheet from the mold material;
[0026] (3) Removing the surface layer: the foamed sheet is cut off the surface layer with a cutting machine according to the actual thickness to be removed;
[0027] (4) Pressed texture: Put the sheet with the surface removed into the integrated mold for hot pressing and cooling forming, close the mold, then heat the mold to 185°C, keep it for 1min according to the actual product thickness, and then cool it for 10min to Normal temperature, finally forming lines on the surface of the mat;
[00...
Embodiment 3
[0030] The production process of the present embodiment anti-skid floor mat, this production process comprises the following steps:
[0031] (1) Substrate preparation: Prepare each foaming material, then mix the foaming materials and set aside;
[0032] (2) Foam molding: Pour the mixed foam material into the foam mold, spread it flat, and then foam it at 180°C for 10 minutes to shape the material, then cool it to room temperature, and take out the foamed sheet from the mold material;
[0033] (3) Removing the surface layer: the foamed sheet is cut off the surface layer with a cutting machine according to the actual thickness to be removed;
[0034] (4) Pressed texture: Put the sheet with the surface removed into the hot-pressed cooling forming integrated mold, close the mold, then heat the mold to 145°C, keep it for 5 minutes according to the actual product thickness, and then cool it for 5 minutes to Normal temperature, finally forming lines on the surface of the mat;
[0...
PUM
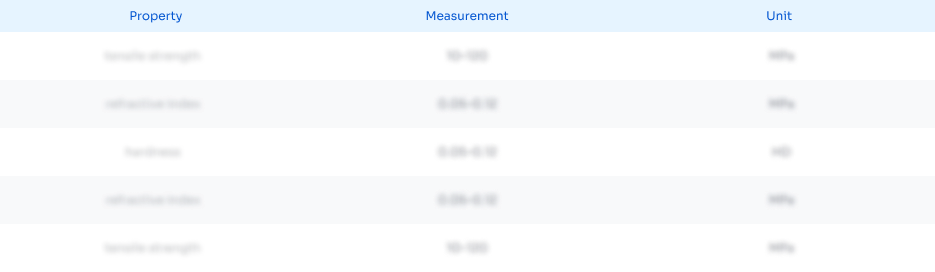
Abstract
Description
Claims
Application Information

- R&D
- Intellectual Property
- Life Sciences
- Materials
- Tech Scout
- Unparalleled Data Quality
- Higher Quality Content
- 60% Fewer Hallucinations
Browse by: Latest US Patents, China's latest patents, Technical Efficacy Thesaurus, Application Domain, Technology Topic, Popular Technical Reports.
© 2025 PatSnap. All rights reserved.Legal|Privacy policy|Modern Slavery Act Transparency Statement|Sitemap|About US| Contact US: help@patsnap.com