Spiral feeder of cracking furnace for plastic garbage
A technology of screw feeder and plastic waste, which is applied in coking ovens, preparation of liquid hydrocarbon mixtures, special forms of dry distillation, etc., can solve problems such as increased friction, poor sealing of cracking inner chambers, and lack of support structures, etc., to achieve a solution Swing problem, guaranteed service life, guaranteed effect of cracking effect
- Summary
- Abstract
- Description
- Claims
- Application Information
AI Technical Summary
Problems solved by technology
Method used
Image
Examples
Embodiment Construction
[0032]In order to further illustrate the technical solution of the present invention, the specific implementation manner of the present invention is now described in conjunction with the accompanying drawings, as Figure 1-11 , in this example, a common rack in this industry is selected as the rack 1-1, and the rack 1-1 is installed on the equipment foundation to support and install the entire functional components; the shell 1-1 is made of a steel plate with a thickness of 1 mm 2. Install the shell 1-2 on the frame 1-1; choose the chain conveyor belt commonly used in this industry as the conveyor belt 1-3, install the conveyor belt 1-3 on one end of the frame 1-1, and connect it with the The power and control system are connected, and the plastic waste to be processed can be sent from the feed port of the sorting equipment to the 1-4 of the material; in this example, a hollow cylinder is selected as the main body of the 1-4 of the material, and the two ends Rotating shaft is ...
PUM
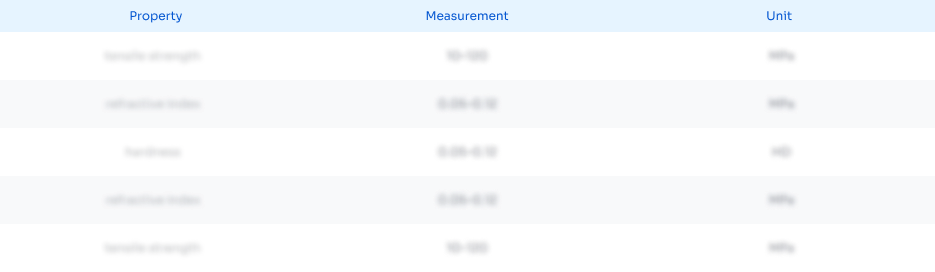
Abstract
Description
Claims
Application Information

- Generate Ideas
- Intellectual Property
- Life Sciences
- Materials
- Tech Scout
- Unparalleled Data Quality
- Higher Quality Content
- 60% Fewer Hallucinations
Browse by: Latest US Patents, China's latest patents, Technical Efficacy Thesaurus, Application Domain, Technology Topic, Popular Technical Reports.
© 2025 PatSnap. All rights reserved.Legal|Privacy policy|Modern Slavery Act Transparency Statement|Sitemap|About US| Contact US: help@patsnap.com