Environment-friendly flame-resistant PP material and preparation method thereof
An environmentally friendly, flame retardant technology, applied in the field of PP materials, can solve the problems of unsuitable electricity environment, low CTI value and GWIT value, etc., achieve high tracking index, improve processing fluidity, and short residence time Effect
- Summary
- Abstract
- Description
- Claims
- Application Information
AI Technical Summary
Problems solved by technology
Method used
Image
Examples
Embodiment 3
[0029] A preparation method of high efficiency, high GWIT, high CTI, low density, no precipitation, environment-friendly flame retardant PP material, characterized in that the method is as follows: Weigh the raw materials by weight: PP 93.3%, compound type resistance 3% of fuel, 3% of commercially available POE, 0.1% of antioxidant (1330), 0.6% of iron oxide; put into a high-mixer and mixed for 2 minutes, discharge the material, and then extrude and granulate with a twin-screw extruder, The processing temperature was at 220°C, and the number of screw revolutions was at 300 rpm.
[0030] The compounded flame retardant is compounded by our company and is made up of three components. Its mass percentage is calcium melamine: 50%; high potassium chloride chelate compound: 25%; magnesium sulfate crystal Must: 25%.
Embodiment 4
[0032] A preparation method of high efficiency, high GWIT, high CTI, low density, no precipitation, and environment-friendly flame retardant PP material, characterized in that the method is as follows: Weigh the raw materials by weight: PP 92%, compound type resistance 4% of fuel, 2% of commercially available POE, 1% of antioxidant (1330), 1% of iron oxide; put into a high-mixer and mixed for 5 minutes, discharge, and then extrude and granulate with a twin-screw extruder, The processing temperature was at 220°C, and the number of screw revolutions was at 400 rpm.
[0033] The compounded flame retardant is compounded by our company, and is made up of three components. Whiskers: 25%.
Embodiment 5
[0035] A preparation method of high efficiency, high GWIT, high CTI, low density, no precipitation, and environment-friendly flame retardant PP material, characterized in that the method is as follows: Weigh the raw materials by weight: PP 92%, compound type resistance 5% of fuel, 2% of commercially available POE, 0.5% of antioxidant (1330), 0.5% of iron oxide; put it into a high-mixer and mixed for 3 minutes, discharged, and then extruded and pelletized with a twin-screw extruder, The processing temperature was at 220°C and the number of screw revolutions was at 350 rpm.
[0036] The compounded flame retardant is compounded by our company and is made up of three components. Its mass percentage is calcium melamine: 50%; high chloride zinc chelate: 25%; magnesium sulfate crystal Must: 25%.
PUM
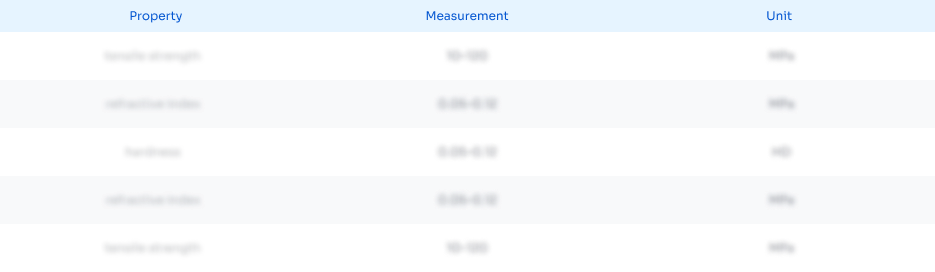
Abstract
Description
Claims
Application Information

- R&D Engineer
- R&D Manager
- IP Professional
- Industry Leading Data Capabilities
- Powerful AI technology
- Patent DNA Extraction
Browse by: Latest US Patents, China's latest patents, Technical Efficacy Thesaurus, Application Domain, Technology Topic, Popular Technical Reports.
© 2024 PatSnap. All rights reserved.Legal|Privacy policy|Modern Slavery Act Transparency Statement|Sitemap|About US| Contact US: help@patsnap.com