PC bag manufacturing process
A manufacturing process and luggage technology, applied in the direction of coating, etc., can solve the problems of difficult PC materials, and achieve the effects of enhanced fluidity, good abrasion resistance, and high strength
- Summary
- Abstract
- Description
- Claims
- Application Information
AI Technical Summary
Problems solved by technology
Method used
Examples
Embodiment Construction
[0031] The technical scheme that the present invention takes for realizing the above object is:
[0032] A kind of PC luggage manufacturing process, the process steps are:
[0033] (1) After 100% PC material is dehumidified and dried at 120°C for 4-10 hours, it is worth drying the PC material,
[0034] (2) After mixing the coloring material, first pass it through the mixer for 40 to 60 minutes, and then process it through high-temperature dehumidification and drying to obtain the coloring material;
[0035] (3) PC material in step 1, 3-10 parts of styrene-acrylamide copolymer, 0.5-1.5 parts of zirconium phosphate, 1-3 parts of hydrotalcite, 0.5-1.5 parts of boric acid Zinc and 1~3 parts of zirconium borate are thrown into the reaction kettle and stirred thoroughly, then 1~10 parts of the blending material in step 2 are added, and the PC raw material is obtained after fully stirred;
[0036] (4) Put the obtained PC raw material into the injection molding machine, the injectio...
PUM
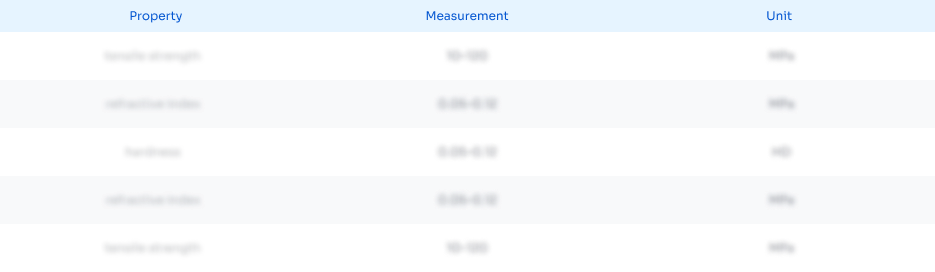
Abstract
Description
Claims
Application Information

- R&D Engineer
- R&D Manager
- IP Professional
- Industry Leading Data Capabilities
- Powerful AI technology
- Patent DNA Extraction
Browse by: Latest US Patents, China's latest patents, Technical Efficacy Thesaurus, Application Domain, Technology Topic, Popular Technical Reports.
© 2024 PatSnap. All rights reserved.Legal|Privacy policy|Modern Slavery Act Transparency Statement|Sitemap|About US| Contact US: help@patsnap.com