Compound finishing agent for improving antistatic performance of polyester fabrics
An antistatic and polyester fiber technology, which is applied in the field of compound finishing agents, achieves the effects of good durability, easy static charging, and poor moisture permeability of clothing
- Summary
- Abstract
- Description
- Claims
- Application Information
AI Technical Summary
Problems solved by technology
Method used
Examples
Embodiment 1
[0019] (1) Mix 20g of chopped cactus with 3 times the weight of deionized water, and use a 1.5kW refiner to refine repeatedly for 3 times, pass through a 100-mesh sieve, and send the resulting filtrate into a ball mill, and ball mill to the output particle size Less than 50μm, that is, cactus extract;
[0020] (2) Add 0.5g of rice bran wax and 0.5g of polydimethyldiallylammonium chloride to 5g of hydroxypropyl methylcellulose, heat up to 80-90°C and mix for 30min, and wait for natural cooling to room temperature Utilize the superfine pulverizer to make fine powder to obtain modified cellulose;
[0021] (3) Add 3g of polyaspartic acid / glucosamine, modified cellulose, 0.5g of cationic polyacrylamide and 0.05g of sodium gluconate to the cactus extract, mix well and let stand for 10min, then send the resulting mixture into a ball mill , ball milled until the output particle size is less than 30μm, the compound finishing agent is obtained.
[0022] Preparation of polyaspartic aci...
Embodiment 2
[0025] (1) Mix 25g of chopped cactus with 3 times the weight of deionized water, and use a 1.5kW refiner to repeatedly refine the pulp for 3 times, pass through a 100-mesh sieve, send the resulting filtrate into a ball mill, and ball mill to the output particle size Less than 50μm, that is, cactus extract;
[0026] (2) Add 0.5g of rice bran wax and 0.3g of polydimethyldiallyl ammonium chloride to 3g of hydroxypropyl methylcellulose, heat up to 80-90°C and mix for 30min, and wait for natural cooling to room temperature Utilize the superfine pulverizer to make fine powder to obtain modified cellulose;
[0027] (3) Add 5g of polyaspartic acid / glucosamine, modified cellulose, 0.5g of cationic polyacrylamide and 0.05g of sodium gluconate to the cactus extract, mix well and let stand for 15min, then send the resulting mixture into a ball mill , ball milled until the output particle size is less than 30μm, the compound finishing agent is obtained.
[0028] Preparation of polyaspart...
Embodiment 3
[0031] (1) Mix 25g of chopped cactus with 3 times the weight of deionized water, and use a 1.5kW refiner to repeatedly refine the pulp for 3 times, pass through a 100-mesh sieve, send the resulting filtrate into a ball mill, and ball mill to the output particle size Less than 50μm, that is, cactus extract;
[0032] (2) Add 0.5g of rice bran wax and 0.3g of polydimethyldiallyl ammonium chloride to 3g of hydroxypropyl methylcellulose, heat up to 80-90°C and mix for 30min, and wait for natural cooling to room temperature Utilize the superfine pulverizer to make fine powder to obtain modified cellulose;
[0033] (3) Add 5g of polyaspartic acid / glucosamine, modified cellulose, 0.5g of cationic polyacrylamide and 0.05g of sodium gluconate to the cactus extract, mix well and let stand for 15min, then send the resulting mixture into a ball mill , ball milling until the output particle size is less than 30μm, the compound finishing agent is obtained.
[0034] Preparation of polyaspar...
PUM
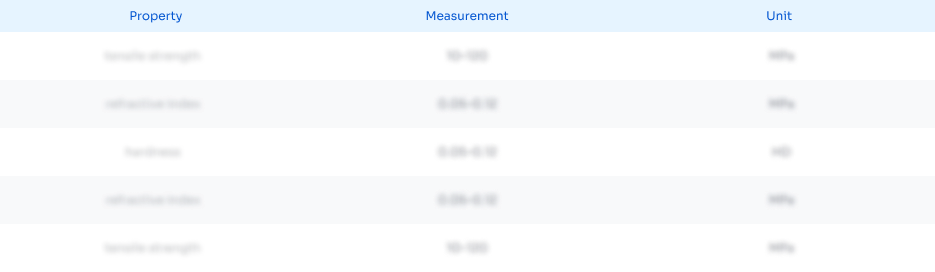
Abstract
Description
Claims
Application Information

- R&D
- Intellectual Property
- Life Sciences
- Materials
- Tech Scout
- Unparalleled Data Quality
- Higher Quality Content
- 60% Fewer Hallucinations
Browse by: Latest US Patents, China's latest patents, Technical Efficacy Thesaurus, Application Domain, Technology Topic, Popular Technical Reports.
© 2025 PatSnap. All rights reserved.Legal|Privacy policy|Modern Slavery Act Transparency Statement|Sitemap|About US| Contact US: help@patsnap.com