A heat-integrated extraction and rectification energy-saving process for separating tetrahydrofuran-methanol
An extractive distillation and tetrahydrofuran technology, which is applied in the field of energy-saving technology for thermally integrated extractive distillation and separation of tetrahydrofuran-methanol, can solve the problems of high separation energy consumption, difficult separation of tetrahydrofuran-methanol mixture, complicated process, etc. The effect of convenience and low investment in equipment
- Summary
- Abstract
- Description
- Claims
- Application Information
AI Technical Summary
Problems solved by technology
Method used
Image
Examples
Embodiment 1
[0032] Attached figure 1 Shown process flow sheet, feed flow rate is 2000kg / h, and feed temperature is 35 ℃, and feed composition is tetrahydrofuran 50% (mass fraction), methyl alcohol 50% (mass fraction); Extractant feed flow rate is 3000kg / h, the supplementary feed flow rate of the extractant is 0.4kg / h, and the feed temperature of the extractant is 55°C. The theoretical plate number of the extractive distillation column is 45, the pressure is 0.3atm (absolute pressure), the feed is from the 20th plate, the feeding position of the extractant is the 3rd plate, and the extraction position of the measuring line is the 40th plate , the reflux ratio is 1.8; the number of theoretical plates of the solvent recovery tower is 12, and the pressure is 1 atm (absolute pressure), fed by the 7th plate, and the position of the measuring line extraction entering the intermediate reboiler is the 4th plate, reflux The ratio is 2.0. After separation, the product concentration of THF is 99.9...
Embodiment 2
[0036] Attached figure 1Shown process flow sheet, feed flow rate is 3000kg / h, and feed temperature is 35 ℃, and feed composition is tetrahydrofuran 50% (mass fraction), methyl alcohol 50% (mass fraction); Extractant feed flow rate is 4000kg / h, the supplementary feed flow rate of the extractant is 0.45kg / h, and the feed temperature of the extractant is 55°C. The theoretical plate number of the extractive distillation column is 50, the pressure is 0.3atm (absolute pressure), the feed is from the 25th plate, the feeding position of the extractant is the 5th plate, and the extraction position of the measuring line is the 42nd plate , the reflux ratio is 1.9; the number of theoretical plates of the solvent recovery tower is 14, and the pressure is 1 atm (absolute pressure). The feed is fed from the 9th plate, and the position of the measuring line to enter the intermediate reboiler is the 6th plate, and the reflux The ratio is 2.4. After separation, the product concentration of ...
Embodiment 3
[0041] Attached figure 1 Shown process flow sheet, feed flow is 2000kg / h, and feed temperature is 35 ℃, and feed is composed of tetrahydrofuran 40% (mass fraction), methyl alcohol 60% (mass fraction); Extractant feed flow is 2800kg / h, the supplementary feed flow rate of the extractant is 0.28kg / h, and the feed temperature of the extractant is 55°C. The theoretical plate number of the extractive distillation column is 48, the pressure is 0.1atm (absolute pressure), the feed is from the 22nd plate, the extraction agent feeding position is the 4th plate, and the extraction position of the measuring line is the 41st plate , the reflux ratio is 2.2; the number of theoretical plates of the solvent recovery tower is 15, and the pressure is 1atm (absolute pressure). The feed is fed from the 10th plate, and the measuring line is extracted into the middle reboiler. The position is the 7th plate, and the reflux The ratio is 2.3. After separation, the product concentration of THF is 99...
PUM
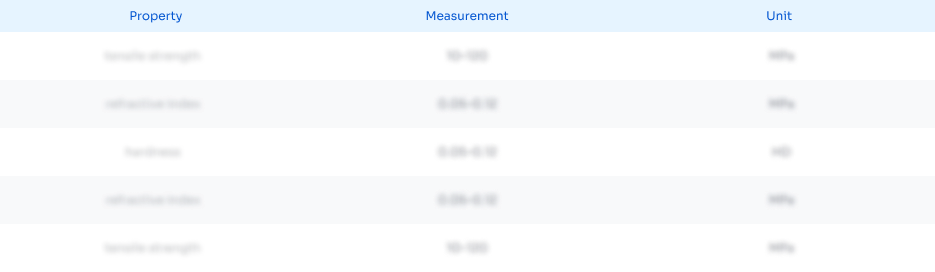
Abstract
Description
Claims
Application Information

- R&D
- Intellectual Property
- Life Sciences
- Materials
- Tech Scout
- Unparalleled Data Quality
- Higher Quality Content
- 60% Fewer Hallucinations
Browse by: Latest US Patents, China's latest patents, Technical Efficacy Thesaurus, Application Domain, Technology Topic, Popular Technical Reports.
© 2025 PatSnap. All rights reserved.Legal|Privacy policy|Modern Slavery Act Transparency Statement|Sitemap|About US| Contact US: help@patsnap.com