Steel Phosphating Process
A steel and process technology, applied in the coating process of metal materials, etc., can solve the problems of coarse phosphating film crystallization, easy rusting of workpieces, long phosphating time, etc., achieve dense and uniform film crystallization, eliminate uneven corrosion, increase The effect of the number of nuclei
- Summary
- Abstract
- Description
- Claims
- Application Information
AI Technical Summary
Problems solved by technology
Method used
Examples
Embodiment 1
[0031] A kind of preparation of surface adjustment fluid: it comprises the following steps:
[0032] (1) Preparation of surface modifier: In parts by weight, 220 parts of deionized water weighed were heated to 70°C. Then, while stirring, 70 parts of disodium hydrogen phosphate, 50 parts of sodium tripolyphosphate and 4 parts of sodium hydroxide were sequentially added to the heated deionization, and then the temperature was raised to about 100°C, and then 6 parts of potassium fluorotitanate and 20 parts of amino trimethylene phosphonic acid, stirred for 25 minutes, then added 4 parts of sodium pyrophosphate, stirred for another 12 minutes to form a uniform mixture and then cooled.
[0033] (2) Take 0.2 kg of the surface regulator prepared in step (1), add it into 50 L of water and stir evenly, and then add an appropriate amount of water to set the volume to 100 L to obtain the surface regulator.
Embodiment 2
[0035] A kind of preparation of surface adjustment fluid: it comprises the following steps:
[0036] (1) Preparation of surface modifier: In parts by weight, 250 parts of deionized water weighed were heated to 65°C. Then, while stirring, 60 parts of disodium hydrogen phosphate, 40 parts of sodium tripolyphosphate and 2 parts of sodium hydroxide were sequentially added to the heated deionization, and then the temperature was raised to about 100°C, and then 5 parts of potassium fluorotitanate and 10 parts of amino trimethylene phosphonic acid, stirred for 20 minutes, then added 2 parts of sodium pyrophosphate, stirred for another 10 minutes to form a uniform mixture and then cooled.
[0037] (2) Take 0.3 kg of the surface regulator prepared in step (1), add it into 50 L of water and stir evenly, and then add an appropriate amount of water to set the volume to 100 L to obtain the surface regulator.
Embodiment 3
[0039] A kind of preparation of surface adjustment fluid: it comprises the following steps:
[0040] (1) Preparation of surface modifier: In parts by weight, 200 parts of deionized water weighed were heated to 68°C. Then, while stirring, 80 parts of disodium hydrogen phosphate, 60 parts of sodium tripolyphosphate and 5 parts of sodium hydroxide were sequentially added to the heated deionization, and then the temperature was raised to about 100°C, and then 8 parts of potassium fluorotitanate and 25 parts of amino trimethylene phosphonic acid, stirred for 30 minutes, then added 5 parts of sodium pyrophosphate, and stirred for another 15 minutes to form a uniform mixture and then cooled.
[0041] (2) Take 0.08 kg of the surface regulator prepared in step (1), add it into 50 L of water and stir evenly, and then add an appropriate amount of water to set the volume to 100 L to obtain the surface regulator.
PUM
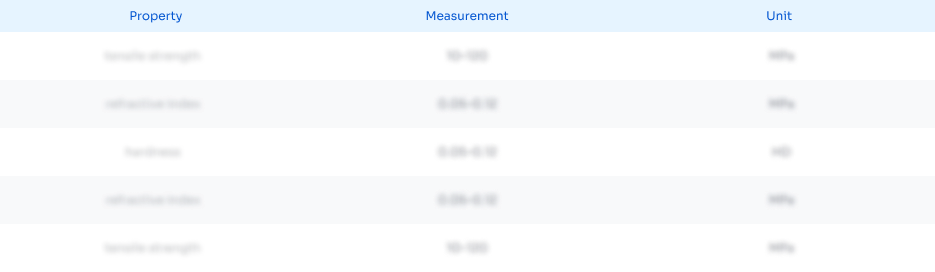
Abstract
Description
Claims
Application Information

- R&D
- Intellectual Property
- Life Sciences
- Materials
- Tech Scout
- Unparalleled Data Quality
- Higher Quality Content
- 60% Fewer Hallucinations
Browse by: Latest US Patents, China's latest patents, Technical Efficacy Thesaurus, Application Domain, Technology Topic, Popular Technical Reports.
© 2025 PatSnap. All rights reserved.Legal|Privacy policy|Modern Slavery Act Transparency Statement|Sitemap|About US| Contact US: help@patsnap.com