Synthesis process of cyclopentyl phenyl ketone
A technology of cyclopentyl phenyl ketone and synthesis process, which is applied in the field of synthesis technology of cyclopentyl phenyl ketone, can solve the problems of harsh operating conditions, unsuitable for industrialized large-scale production, and high low temperature energy consumption, and achieves cost Low, easy to control, high product purity effect
- Summary
- Abstract
- Description
- Claims
- Application Information
AI Technical Summary
Problems solved by technology
Method used
Examples
Embodiment 1
[0015] A kind of synthetic technique of cyclopentyl phenyl ketone of the present invention,
[0016] (1) Add excess 400g of magnesium chips to 1200ml of dry tetrahydrofuran, drop in 30g of bromocyclopentane (this material is the reference material), and heat to initiate the reaction;
[0017] (2) Add 7000ml of tetrahydrofuran and bromocyclopentane (total 1600g) into the reaction system (the amount of solvent is about 4 times that of the reference material), and after the addition, continue to drop 1070g of benzonitrile (the same equivalent as the reference material) ), keep the temperature at 48-50°C, after dripping, keep warm for 2-3 hours, detect 5% remaining benzonitrile by spot plate gas phase (this reaction is slow, and it is more reasonable to have more remaining benzonitrile, and it will not affect the subsequent reaction);
[0018] (3) Use hydrochloric acid to quench the reaction (the exotherm in the early stage of quenching is severe), and the pH value is adjusted to ...
Embodiment 2
[0021] A kind of synthetic technique of cyclopentyl phenyl ketone of the present invention,
[0022] (1) Add excess 4000g of magnesium chips to 12L of dry tetrahydrofuran, drop in 3kg of bromocyclopentane (this material is the reference material), and heat to initiate the reaction;
[0023] (2) Drop 70L tetrahydrofuran and cyclopentane bromide (16kg in total) into the reaction system (the amount of solvent used is about 4 times that of the reference material), and after the addition is completed, continue to drop 10.7kg of benzonitrile (the equivalent of the reference material Same), keep the temperature at 48-50°C, after dropping, keep warm for 2-3 hours, and detect 5% remaining benzonitrile by spot plate gas phase (this reaction is slow, and it is more reasonable to have more remaining benzonitrile, and it will not affect the subsequent reaction);
[0024] (3) Use hydrochloric acid to quench the reaction (the exotherm in the early stage of quenching is severe), and the pH va...
Embodiment 3
[0027] A kind of synthetic technique of cyclopentyl phenyl ketone of the present invention,
[0028] (1) Add 200g of excess magnesium chips to 600ml of dry tetrahydrofuran, drop 30g of bromocyclopentane (this material is the reference material), and heat to initiate the reaction;
[0029] (2) Drop 3.5L tetrahydrofuran and cyclopentane bromide (900g in total) into the reaction system (the amount of solvent used is about 4 times that of the reference material), and after the addition, continue to drop 535g of benzonitrile (the equivalent of the reference material Same), keep the temperature at 48-50°C, after dropping, keep warm for 2-3 hours, and detect 5% remaining benzonitrile by spot plate gas phase (this reaction is slow, and it is more reasonable to have more remaining benzonitrile, and it will not affect the subsequent reaction);
[0030] (3) Use hydrochloric acid to quench the reaction (the exotherm in the early stage of quenching is severe), and the pH value is adjusted ...
PUM
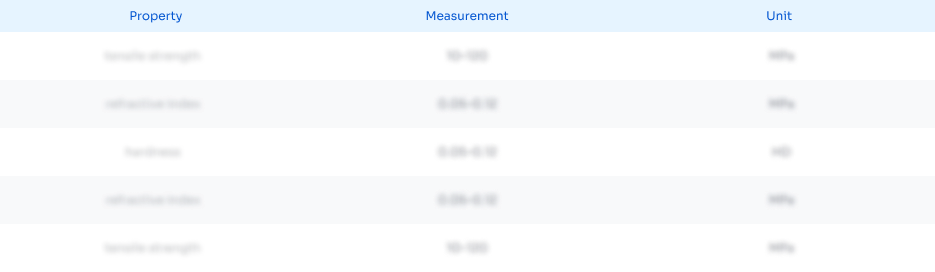
Abstract
Description
Claims
Application Information

- Generate Ideas
- Intellectual Property
- Life Sciences
- Materials
- Tech Scout
- Unparalleled Data Quality
- Higher Quality Content
- 60% Fewer Hallucinations
Browse by: Latest US Patents, China's latest patents, Technical Efficacy Thesaurus, Application Domain, Technology Topic, Popular Technical Reports.
© 2025 PatSnap. All rights reserved.Legal|Privacy policy|Modern Slavery Act Transparency Statement|Sitemap|About US| Contact US: help@patsnap.com