Fuzzy control system for posture of tube push bench based on MEMS gyroscope and method
A fuzzy control system and fuzzy control technology, applied in attitude control, general control system, control/adjustment system, etc., can solve problems such as lateral deflection of pipe jacking machine, poor correction effect, and serpentine deviation
- Summary
- Abstract
- Description
- Claims
- Application Information
AI Technical Summary
Problems solved by technology
Method used
Image
Examples
Embodiment 1
[0078] The specific steps of the design of the attitude fuzzy controller, that is, the controller 3, are as follows.
[0079] ① Define the input and output: the horizontal and vertical position deviation, angular deviation and the rate of change of the deviation are used as the input variables of the controller 3, and the control volume of the correction cylinder 4 is used as the output variable.
[0080] ② Define input / output domain of discourse: select the domain of discourse of each input variable and output variable according to the allowable deviation range stipulated in the construction of the pipe jacking machine and the maximum allowable value of surface uplift and settlement; define the domain of discourse as 13 levels: { -6, -5, -4, -3, -2, -1, 0, 1, 2, 3, 4, 5, 6}.
[0081] ③ Define the input / output fuzzy set: Divide the error, error rate of change and control value of the correction cylinder into seven levels of language value data, which are expressed in terms of w...
PUM
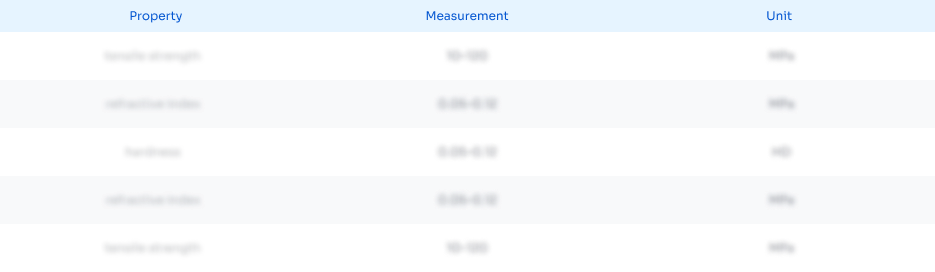
Abstract
Description
Claims
Application Information

- Generate Ideas
- Intellectual Property
- Life Sciences
- Materials
- Tech Scout
- Unparalleled Data Quality
- Higher Quality Content
- 60% Fewer Hallucinations
Browse by: Latest US Patents, China's latest patents, Technical Efficacy Thesaurus, Application Domain, Technology Topic, Popular Technical Reports.
© 2025 PatSnap. All rights reserved.Legal|Privacy policy|Modern Slavery Act Transparency Statement|Sitemap|About US| Contact US: help@patsnap.com