A preparation method of flame-retardant and dust-proof porous polyamide fiber composite material
A technology of polyamide fibers and composite materials, which is applied in the field of textile fibers, can solve the problems of unsatisfactory properties of polyamide fibers, and achieve the effects of enhancing fiber strength and toughness, good adsorption, and good dust resistance
- Summary
- Abstract
- Description
- Claims
- Application Information
AI Technical Summary
Problems solved by technology
Method used
Examples
Embodiment 1
[0013] Weigh 6kg of decanediamine and 4kg of butanediamine, and dissolve them in ethanol to obtain solution A; weigh 6k of sebacic acid and 4kg of itaconic acid, dissolve them in ethanol to obtain solution B, mix solution A and solution B, and heat at 60°C Stir, mix and react for 20 minutes, cool to crystallize, wash and dry to obtain amide salt;
[0014] Weigh polyethylene glycol, dimethylacetamide, amide salt, the molar ratio of polyethylene glycol, dimethylacetamide, amide salt is 4:15:25, under nitrogen protection, polyethylene glycol is used as The pore forming agent is added to dimethylacetamide, mixed evenly, added to the amide salt, heated and melted, and reacted at 200°C for 5 hours. After fully reacting, a copolyamide fluid is obtained, and then porous graphene powder is added to form a porous The amount of graphene powder added is 1% of the mass of the copolyamide fluid, stirred evenly, cooled, and then transferred to a spinning machine for spinning to obtain polyam...
Embodiment 2
[0017] Weigh 5kg of decanediamine and 5kg of butanediamine, and dissolve them in ethanol to obtain solution A; weigh 5k of sebacic acid and 5kg of itaconic acid, dissolve them in ethanol to obtain solution B, mix solution A and solution B at 50°C Stir, mix and react for 20 minutes, cool to crystallize, wash and dry to obtain amide salt;
[0018] Weigh polyethylene glycol, dimethylacetamide, amide salt, the molar ratio of polyethylene glycol, dimethylacetamide, amide salt is 5:12:20, under nitrogen protection, polyethylene glycol is used as The pore forming agent is added to dimethylacetamide, mixed evenly, added to the amide salt, heated and melted, reacted at 200°C for 8 hours, and the copolyamide fluid is obtained after full reaction, and then the porous graphene powder is added to make the porous The amount of graphene powder added is 2% of the mass of the copolyamide fluid, stirred evenly, cooled, then transferred to a spinning machine for spinning to obtain polyamide fibe...
Embodiment 3
[0021] Weigh 6kg of decanediamine and 4kg of butanediamine, and dissolve them in ethanol to obtain solution A; weigh 5k of sebacic acid and 5kg of itaconic acid, dissolve them in ethanol to obtain solution B, mix solution A and solution B, and heat at 55°C Stir, mix and react for 20 minutes, cool to crystallize, wash and dry to obtain amide salt;
[0022] Weigh polyethylene glycol, dimethylacetamide, amide salt, the molar ratio of polyethylene glycol, dimethylacetamide, amide salt is 4:12:22, under nitrogen protection, polyethylene glycol is used as The pore forming agent is added to dimethylacetamide, mixed evenly, added to the amide salt, heated and melted, and reacted at 200°C for 5 hours. After fully reacting, a copolyamide fluid is obtained, and then porous graphene powder is added to form a porous The amount of graphene powder added is 3% of the mass of the copolyamide fluid, stirred evenly, cooled, and then transferred to a spinning machine for spinning to obtain polyam...
PUM
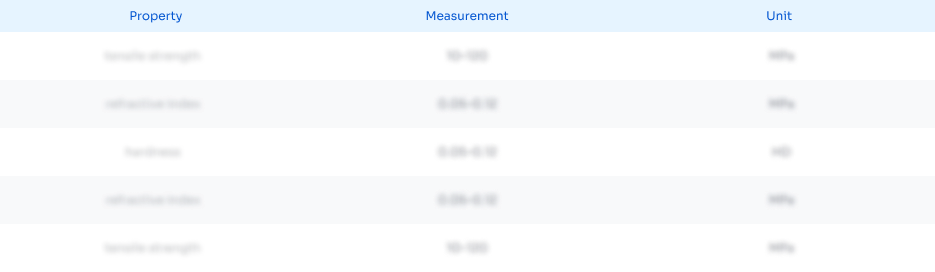
Abstract
Description
Claims
Application Information

- R&D Engineer
- R&D Manager
- IP Professional
- Industry Leading Data Capabilities
- Powerful AI technology
- Patent DNA Extraction
Browse by: Latest US Patents, China's latest patents, Technical Efficacy Thesaurus, Application Domain, Technology Topic, Popular Technical Reports.
© 2024 PatSnap. All rights reserved.Legal|Privacy policy|Modern Slavery Act Transparency Statement|Sitemap|About US| Contact US: help@patsnap.com