High-temperature pyrolysis gas reclamation system and method
A high-temperature pyrolysis and warm-heating technology, used in climate sustainability, acetylene generators, chemical industry, etc., can solve problems such as underutilization of sensible heat and chemical heat, and improve energy self-sufficiency, improve thermal efficiency, The effect of reducing production costs
- Summary
- Abstract
- Description
- Claims
- Application Information
AI Technical Summary
Problems solved by technology
Method used
Image
Examples
Embodiment 1
[0056] 1. The raw material is pyrolyzed in a pyrolysis furnace with a pyrolysis temperature of 900°C and a pyrolysis time of 1 hour to obtain solid products and high-temperature pyrolysis gas.
[0057] 2. Send the solid product into the calcium carbide furnace and heat it to 2250°C to generate calcium carbide and exhaust gas. The heating time is 40 minutes.
[0058] 3. The calcium carbide is sent to the acetylene generator to react with water to generate acetylene and calcium carbide slag.
[0059] 4. Send the carbide slag into the drying device, pass the high-temperature pyrolysis gas into the drying device, and dry the carbide slag to obtain dry carbide slag and low-temperature pyrolysis gas; adjust the intake of high-temperature pyrolysis gas in the drying device through the air flow valve The amount of high-temperature pyrolysis gas drying the carbide slag is controlled at 60 minutes to fully dry the carbide slag. The temperature of the dried carbide slag is 110°C, and the...
Embodiment 2
[0064] 1. The raw material is pyrolyzed in a pyrolysis furnace with a pyrolysis temperature of 600°C and a pyrolysis time of 1.5 hours to obtain solid products and high-temperature pyrolysis gas.
[0065] 2. Send the solid product into the calcium carbide furnace and heat it to 2200°C to generate calcium carbide and exhaust gas. The heating time is 45 minutes.
[0066] 3. The calcium carbide is sent to the acetylene generator to react with water to generate acetylene and calcium carbide slag.
[0067] 4. Send the carbide slag into the drying device, pass the high-temperature pyrolysis gas into the drying device, and dry the carbide slag to obtain dry carbide slag and low-temperature pyrolysis gas; adjust the intake of high-temperature pyrolysis gas in the drying device through the air flow valve The amount of high-temperature pyrolysis gas drying the carbide slag is controlled at 50 minutes to fully dry the carbide slag. The temperature of the dried carbide slag is 120°C, and ...
Embodiment 3
[0072] 1. The raw material is pyrolyzed in a pyrolysis furnace with a pyrolysis temperature of 500°C and a pyrolysis time of 2 hours to obtain solid products and high-temperature pyrolysis gas.
[0073] 2. Send the solid product into the calcium carbide furnace and heat it to 2100°C to generate calcium carbide and exhaust gas. The heating time is 50 minutes.
[0074] 3. The calcium carbide is sent to the acetylene generator to react with water to generate acetylene and calcium carbide slag.
[0075] 4. Send the carbide slag into the drying device, pass the high-temperature pyrolysis gas into the drying device, and dry the carbide slag to obtain dry carbide slag and low-temperature pyrolysis gas; adjust the intake of high-temperature pyrolysis gas in the drying device through the air flow valve The amount of high-temperature pyrolysis gas drying the carbide slag is controlled at 30 minutes to fully dry the carbide slag. The temperature of the dried carbide slag is 130°C, and th...
PUM
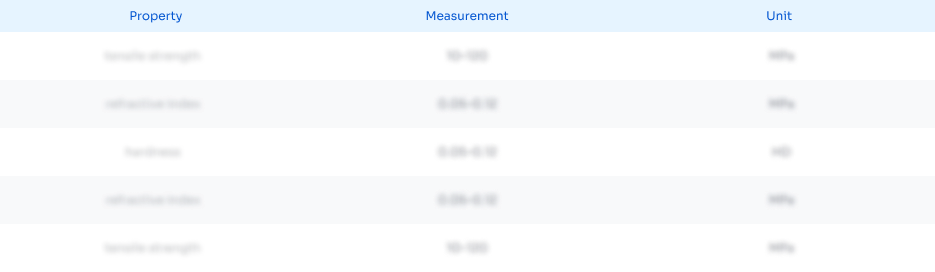
Abstract
Description
Claims
Application Information

- R&D Engineer
- R&D Manager
- IP Professional
- Industry Leading Data Capabilities
- Powerful AI technology
- Patent DNA Extraction
Browse by: Latest US Patents, China's latest patents, Technical Efficacy Thesaurus, Application Domain, Technology Topic, Popular Technical Reports.
© 2024 PatSnap. All rights reserved.Legal|Privacy policy|Modern Slavery Act Transparency Statement|Sitemap|About US| Contact US: help@patsnap.com