Preparation method of zero shrinkage LTCC multi-layer ceramic substrate
A technology of multilayer ceramics and porous ceramics, which is applied in the preparation of zero-shrinkage LTCC multilayer ceramic substrates in the plane X\Y direction, and in the field of preparation of zero-shrinkage LTCC multilayer ceramic substrates, which can solve the difficulty of consistency control and shrinkage control. Poor precision, high material cost and other problems, to achieve the effect of loose material and equipment performance requirements, solve thermal uniformity, and simple preparation process
- Summary
- Abstract
- Description
- Claims
- Application Information
AI Technical Summary
Problems solved by technology
Method used
Image
Examples
Embodiment 1
[0033] A preparation method of a zero-shrinkage LTCC multilayer ceramic substrate of the present invention, such as figure 1 shown, including the following steps:
[0034] (1) Prepare dupont 951 LTCC raw ceramic sheets, and perform the pre-processing operations of punching, printing, and positioning.
[0035] (2) Cut the LTCC green ceramic sheet 5 obtained by the previous process operation into small pieces of 70mm×70mm, stack the small pieces in turn into 10 layers, and then place two 0.1mm thick AlN ceramic green sheets on the upper and lower sides of the stack. Put one layer, and heat-press for 2 hours at a temperature of 80°C and a pressure of 15 MPa to form a green porcelain body.
[0036] (3) First place a porous ceramic pressing plate 3 isolation layer on the upper and lower surfaces of the green porcelain body, and then place a porous silicon carbide pressing plate 2 on the upper and lower surfaces of the porous ceramic pressing plate 3 holding the green porcelain bod...
Embodiment 2
[0042] A preparation method of a zero-shrinkage LTCC multilayer ceramic substrate of the present invention, such as figure 1 shown, including the following steps:
[0043] (1) Prepare the Ferro A6 LTCC green ceramic sheet, and carry out the pre-processing work of punching, printing and positioning.
[0044] (2) Cut the green ceramic sheet obtained in step (1) into small pieces of 70mm×70mm, and stack them sequentially in 20 layers, and then put two 0.1mm thick AlN ceramic green sheets on the top and bottom of the stack, and place them on the The temperature is 90°C, and the pressure is 20MPa, and the hot pressing is carried out for 1 hour to form a green porcelain body.
[0045] (3) First place a porous ceramic press plate 3 on the upper and lower surfaces of the green porcelain body, and then place a porous silicon carbide press plate 2 on the upper and lower surfaces of the porous ceramic press plate 3 holding the green porcelain body, and place under pressure on the devic...
Embodiment 3
[0051] A preparation method of a zero-shrinkage LTCC multilayer ceramic substrate of the present invention comprises the following steps:
[0052] (1) Prepare the dupont 951 LTCC green ceramic sheet, and carry out the pre-processing work of punching, printing and positioning.
[0053] (2) Cut the green ceramic sheet obtained in step (1) into small pieces of 70mm×70mm, stack them in sequence with 10 layers, and then put two pieces of 0.1mm thick Al 2 o 3 Ceramic green porcelain sheets are placed on the upper and lower layers of the laminate, and hot-pressed at a temperature of 100°C and a pressure of 15MPa for 1 hour to form a green porcelain body.
[0054] (3) First place a porous ceramic press plate 3 on the upper and lower surfaces of the green porcelain body, and then place a porous silicon carbide press plate 2 on the upper and lower surfaces of the porous ceramic press plate 3 holding the green porcelain body, and place under pressure on the device.
[0055] (4) Start ...
PUM
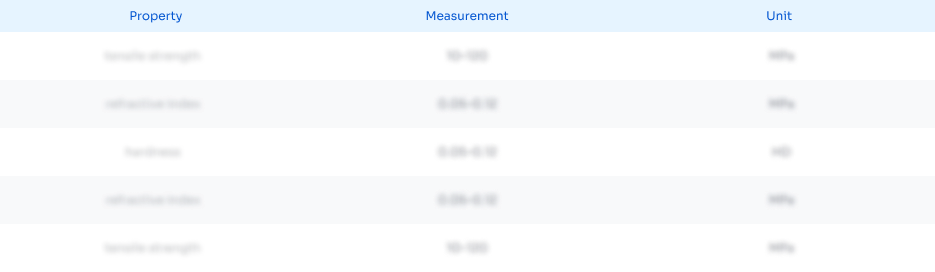
Abstract
Description
Claims
Application Information

- R&D
- Intellectual Property
- Life Sciences
- Materials
- Tech Scout
- Unparalleled Data Quality
- Higher Quality Content
- 60% Fewer Hallucinations
Browse by: Latest US Patents, China's latest patents, Technical Efficacy Thesaurus, Application Domain, Technology Topic, Popular Technical Reports.
© 2025 PatSnap. All rights reserved.Legal|Privacy policy|Modern Slavery Act Transparency Statement|Sitemap|About US| Contact US: help@patsnap.com