A kind of equipment and method for preparing composite steel ingot
A composite steel and equipment technology, which is applied in metallurgy and casting fields, can solve problems such as insufficient cooling strength, low production efficiency, and excessive size, and achieve the effects of simplifying production equipment, increasing productivity, and improving quality
- Summary
- Abstract
- Description
- Claims
- Application Information
AI Technical Summary
Problems solved by technology
Method used
Image
Examples
Embodiment 1
[0076] A device for preparing a composite steel ingot, comprising a conductive crystallizer, a consumable electrode assembly, a first power source, such as figure 1 Its front sectional view is shown, wherein the conductive crystallizer 1 is a cylindrical structure with an upper opening and a lower opening with a first diameter, a plurality of consumable electrodes 2 constitute a consumable electrode assembly, and a plurality of consumable electrodes Stretch into this tubular structure from the upper opening of the conductive crystallizer 1, and have a certain distance from the inner circumferential surface of the tubular structure, and this distance is recorded as the first distance; the first distance is less than half of the first diameter, so as to ensure The consumable electrode moves up and down along the inner circumferential surface of the cylindrical structure; the conductive crystallizer 1 and the consumable electrode assembly are electrically connected through the fir...
Embodiment 2
[0103] This embodiment is on the basis of embodiment 1, the equipment for preparing composite steel ingot prepares composite steel ingot, as Figure 4a As shown in , the first cable 5 is connected to the dummy plate on the ingot drawing device 4 , and the first switch 14 controls the connection and disconnection of the dummy plate on the ingot drawing device 4 with the first power supply 9 and the conductive section 7 .
[0104] The difference between the preparation method and Example 1 is that after the molten slag is poured into the conductive crystallizer, as Figure 4a As shown, the consumable electrode 2 is not lowered earlier, and the switch 14 is closed to form the circuit of the slag pool, the conductive section of the conductive crystallizer, the first power supply, the dummy plate and the mandrel of the ingot pulling device. Now, the mandrel 8 can be preheated again due to the Joule heat of the slag pool. After the mandrel 8 is preheated to a certain temperature, t...
Embodiment 3
[0110] This embodiment is on the basis of Embodiment 1, and adopts a dual-power supply and dual-circuit power supply mode, such as Figure 5a As shown, in the equipment for preparing composite steel ingots, the conductive section 7 is connected to the dummy plate on the ingot drawing device 4 through a second cable provided with a second power supply 15 and a second switch 16 . Since the single power supply and dual circuits cannot match the power distribution of the upper and lower circuits well, dual power supplies are used for power supply. Regulate the power of the two loops.
[0111] On the basis of the preparation method of Example 1, the preparation is carried out, wherein the difference from Example 1 is: after pouring slag into the conductive crystallizer 1, as Figure 5a As shown in , do not lower the consumable electrode 2 first, but first close the second switch 16 to form the conductive section 7, the slag pool 12, the mandrel 8 and the dummy plate of the ingot d...
PUM
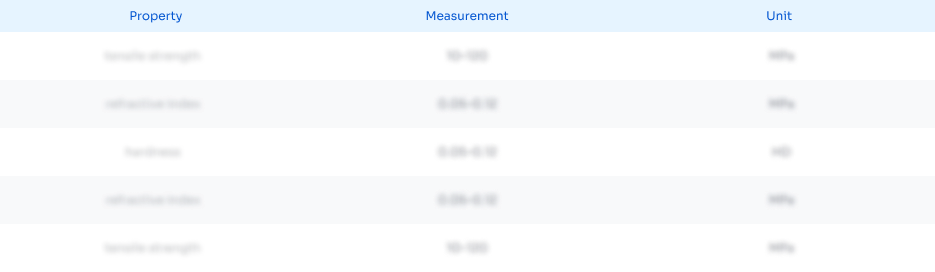
Abstract
Description
Claims
Application Information

- R&D
- Intellectual Property
- Life Sciences
- Materials
- Tech Scout
- Unparalleled Data Quality
- Higher Quality Content
- 60% Fewer Hallucinations
Browse by: Latest US Patents, China's latest patents, Technical Efficacy Thesaurus, Application Domain, Technology Topic, Popular Technical Reports.
© 2025 PatSnap. All rights reserved.Legal|Privacy policy|Modern Slavery Act Transparency Statement|Sitemap|About US| Contact US: help@patsnap.com