Flame retardant, polyester, flame-retarding epoxy resin cured material and preparation method thereof
A flame-retardant epoxy resin, epoxy resin curing technology, applied in the direction of chemical instruments and methods, manufacture of fire-resistant and flame-retardant filaments, compounds of Group 5/15 elements of the periodic table, etc. Elongation strength and mechanical properties are greatly affected, and the effects of mechanical strength improvement, easy realization of conditions and simple operation are achieved.
- Summary
- Abstract
- Description
- Claims
- Application Information
AI Technical Summary
Problems solved by technology
Method used
Image
Examples
preparation example Construction
[0023] The embodiment of the present invention also provides a method for preparing a cured flame-retardant epoxy resin, comprising the following steps:
[0024] S1, synthesis of intermediates;
[0025] The addition accelerator and 2-hydroxybenzaldehyde undergo a catalytic reaction under the action of a catalyst, and what actually occurs between the addition accelerator and 2-hydroxybenzaldehyde is a condensation reaction. The reaction mechanism is: the carbonyl of 2-hydroxybenzaldehyde undergoes nucleophilic addition reaction with the amino group to form a secondary amine with a hydroxyl group, and under the action of a catalyst, a part of water is removed to form an imine.
[0026] A further specific operation process is that the addition accelerator and the solvent are mixed under the atmosphere of protective gas, and then mixed with 2-hydroxybenzaldehyde and a catalyst to undergo a catalytic reaction. The use of protective gas is to prevent the oxygen in the air from affe...
Embodiment 1
[0052] A flame retardant provided in this embodiment has a structural formula as shown below.
[0053]
[0054] The embodiment of the present invention also provides a method for preparing a flame retardant:
[0055] S1. Synthesis of intermediates: After mixing 1mol 4,4'-diaminophenylsulfone and 100ml tetrahydrofuran, under the protection of nitrogen, heat to the reflux temperature of tetrahydrofuran, then add 2mol 2-hydroxybenzaldehyde and 0.2g acetic acid, and react 6 Hour. After the reaction was completed, it was cooled, filtered, washed three times with tetrahydrofuran, and then dried to obtain 0.96 mol of an orange-red intermediate, ie, the yield of the intermediate was 96.5%.
[0056] S2, the synthesis of flame retardant: after mixing 1.3mol intermediate with 1mol 9,10-dihydro-9-oxa-10-phosphaphenanthrene-10-oxide, add tetrahydrofuran as reaction solvent, and in tetrahydrofuran Reaction at reflux temperature for 12 hours. After the reaction, the reaction solution w...
Embodiment 2
[0063] Embodiments of the present invention provide a method for preparing a flame retardant:
[0064] S1. Synthesis of intermediates: After mixing 1mol 4,4'-diaminophenylsulfone and 200ml chloroform, under the protection of nitrogen, heat to the reflux temperature of chloroform, and then add 2.5mol 2-hydroxybenzaldehyde and 0.1g p-toluenesulfonic acid, and reacted for 8 hours. After the reaction was completed, it was cooled, filtered, washed with chloroform for 3 times, and then dried to obtain 0.97 mol of an orange-red intermediate, that is, the yield of the intermediate was 97.1%.
[0065] S2, synthesis of flame retardant: after mixing 1.4mol intermediate with 1mol 9,10-dihydro-9-oxa-10-phosphaphenanthrene-10-oxide, add chloroform as reaction solvent, and The reaction was carried out at the reflux temperature of chloroform for 10 hours. After the reaction, the reaction solution was naturally cooled to room temperature, and the flame retardant was precipitated from the rea...
PUM
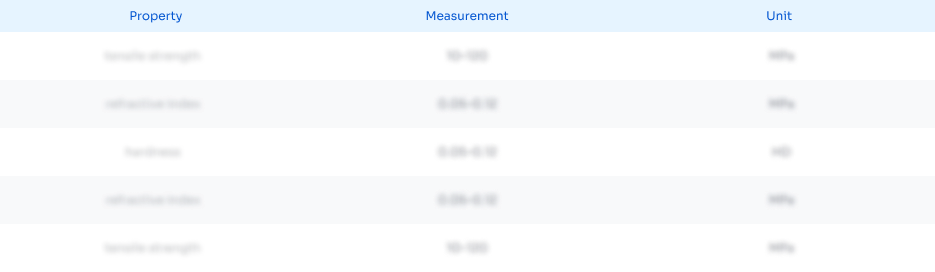
Abstract
Description
Claims
Application Information

- R&D Engineer
- R&D Manager
- IP Professional
- Industry Leading Data Capabilities
- Powerful AI technology
- Patent DNA Extraction
Browse by: Latest US Patents, China's latest patents, Technical Efficacy Thesaurus, Application Domain, Technology Topic, Popular Technical Reports.
© 2024 PatSnap. All rights reserved.Legal|Privacy policy|Modern Slavery Act Transparency Statement|Sitemap|About US| Contact US: help@patsnap.com