Regenerative modification method of thermoset unsaturated polyester resin waste material
A polyester resin and unsaturated technology, applied in the field of regeneration and modification of thermosetting unsaturated polyester resin waste, can solve the problem that thermosetting unsaturated polyester resin waste cannot be effectively recycled and reused, and achieve good plasticity and reduce cross-linking. The effect of density
- Summary
- Abstract
- Description
- Claims
- Application Information
AI Technical Summary
Problems solved by technology
Method used
Image
Examples
Embodiment 1
[0048] Stir 200 kg of the above-mentioned modified matrix, 300 kg of water, and 5 kg of alcoholysis agent ethylene glycol in an enamel kettle equipped with a 20kw high-shear emulsifying disperser to raise the temperature to 80-90°C, stirring intermittently, each time Run for 5 minutes with an interval of 2 minutes. After the temperature reaches 80°C, 0.8 kg of catalyst 1,5,7-triazabicyclo[4.4.0]dec-5-ene (TBD) is added, and the surface of the modified substrate is activated under high-speed shear stirring to activate the catalyst The time is 30-60 minutes.
[0049] Put the catalytically activated thermosetting resin waste slurry into a 1-ton enamel polymerization kettle, add 140 kg of water, 0.8 kg of dispersant calcium hydroxyphosphate, 0.2 kg of initiator azobisisobutyronitrile, and 10 kg of styrene (St) 20 kg of butyl acrylate (BA), heat up to 80°C, carry out suspension polymerization while stirring, polymerize for 3 hours, add a small amount of tert-butyl hydroperoxide, h...
Embodiment 2
[0052] The proportioning and process of this embodiment are as in embodiment 1, the only difference is that the catalyst is zinc acetylacetonate.
Embodiment 3
[0054] The proportioning and process of the present embodiment are as in embodiment 1, the only difference is that the catalyst is zinc acetate.
PUM
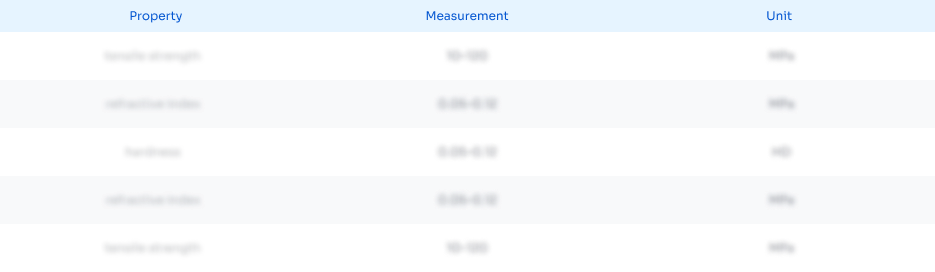
Abstract
Description
Claims
Application Information

- R&D
- Intellectual Property
- Life Sciences
- Materials
- Tech Scout
- Unparalleled Data Quality
- Higher Quality Content
- 60% Fewer Hallucinations
Browse by: Latest US Patents, China's latest patents, Technical Efficacy Thesaurus, Application Domain, Technology Topic, Popular Technical Reports.
© 2025 PatSnap. All rights reserved.Legal|Privacy policy|Modern Slavery Act Transparency Statement|Sitemap|About US| Contact US: help@patsnap.com